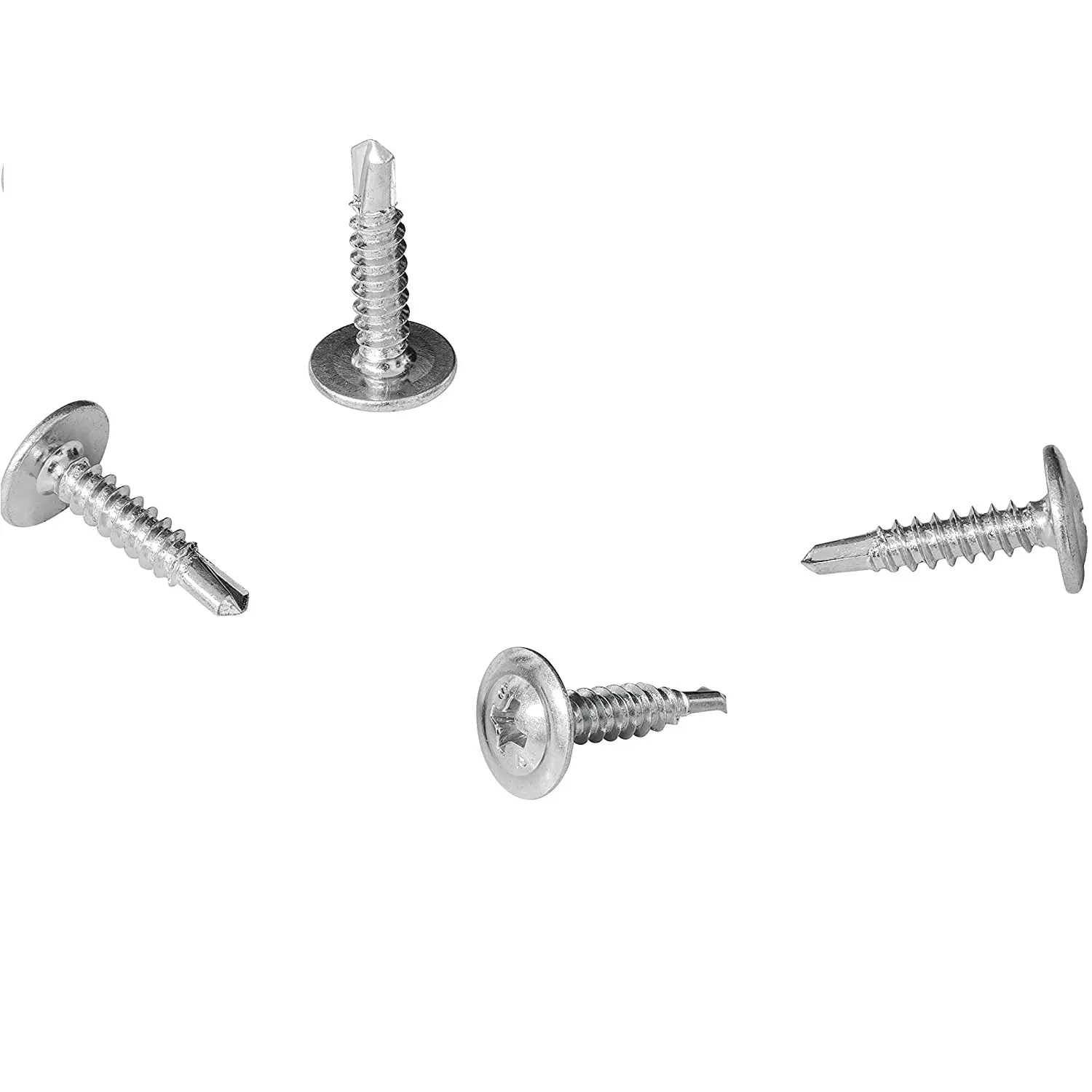
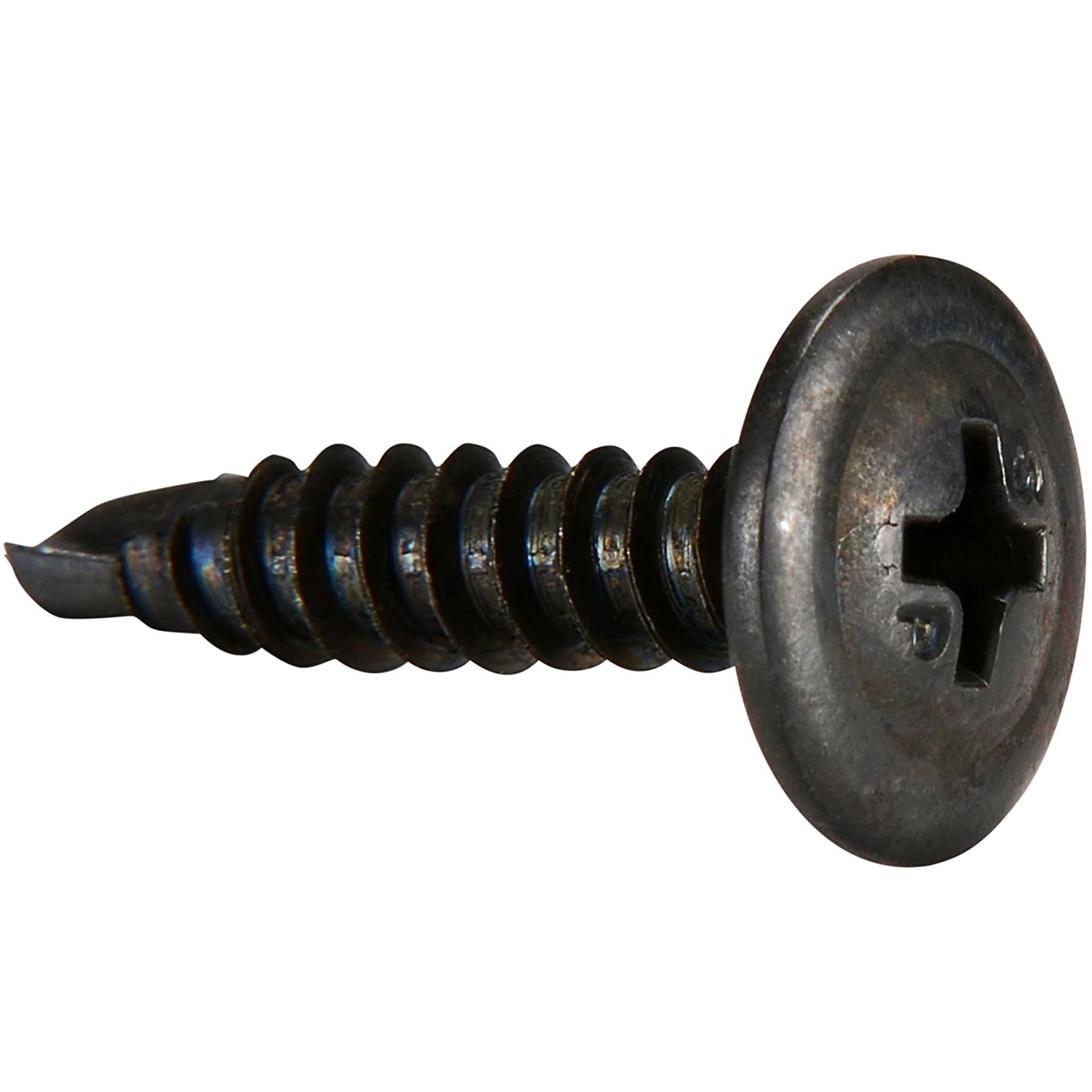
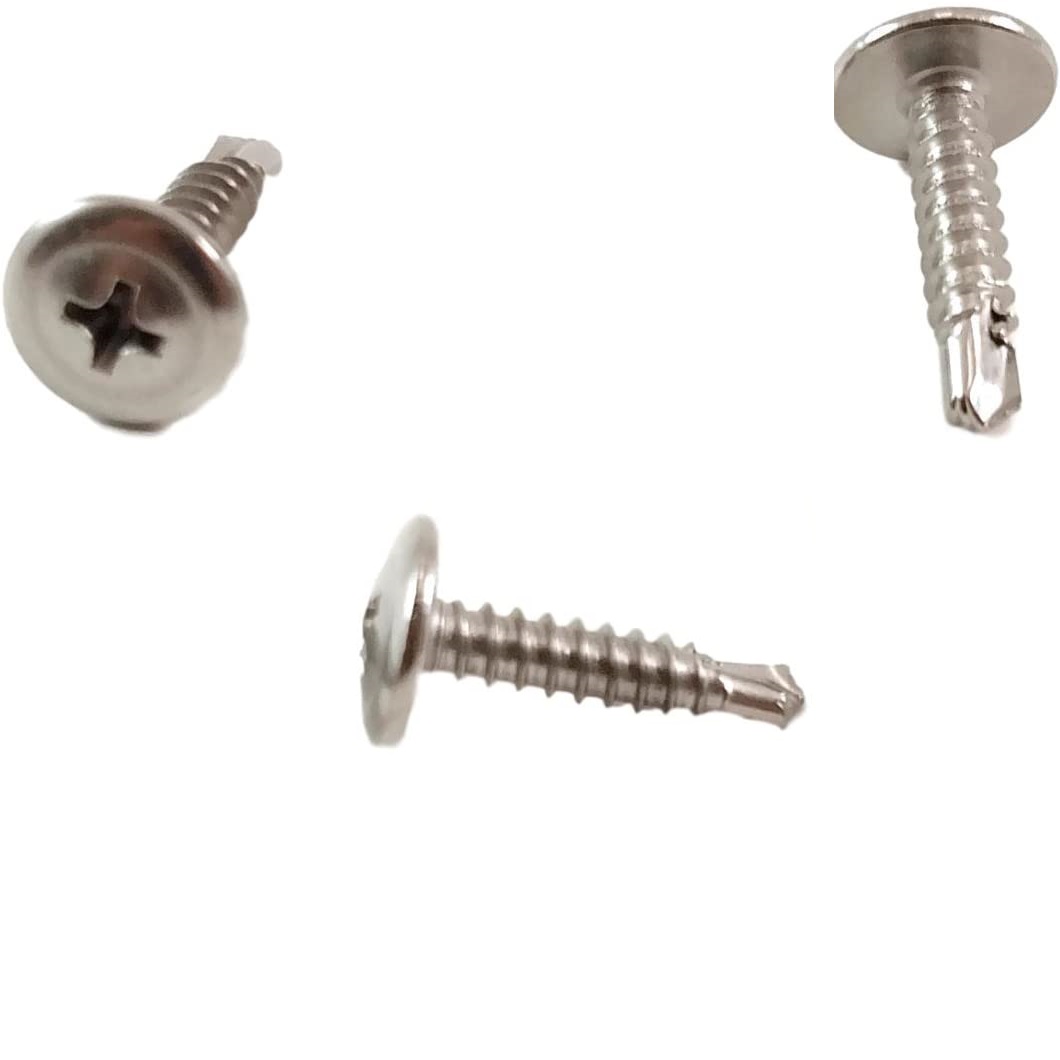

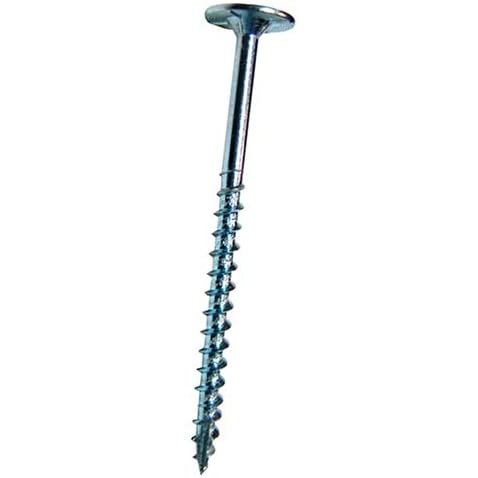
Choose the Best Screw for Metal Studs
Customer’s Choice: the Best Rated Screws
607 users answered this survey. Please help us improve this review!
When you’re mounting something to metal studs, the wrong screws can lead to disaster. You need screws that will hold tight and not easily strip, and that’s why we’ve put together this comprehensive guide on the best screws for metal studs. In it, you’ll find reviews of some of our favorite products as well as tips on how to use them for your own projects. So whether you’re a beginner or a seasoned pro, read on for the information you need to make the right choice!
8 x 1″ Phillips Modified Truss Head Self-Drilling Tek Screw
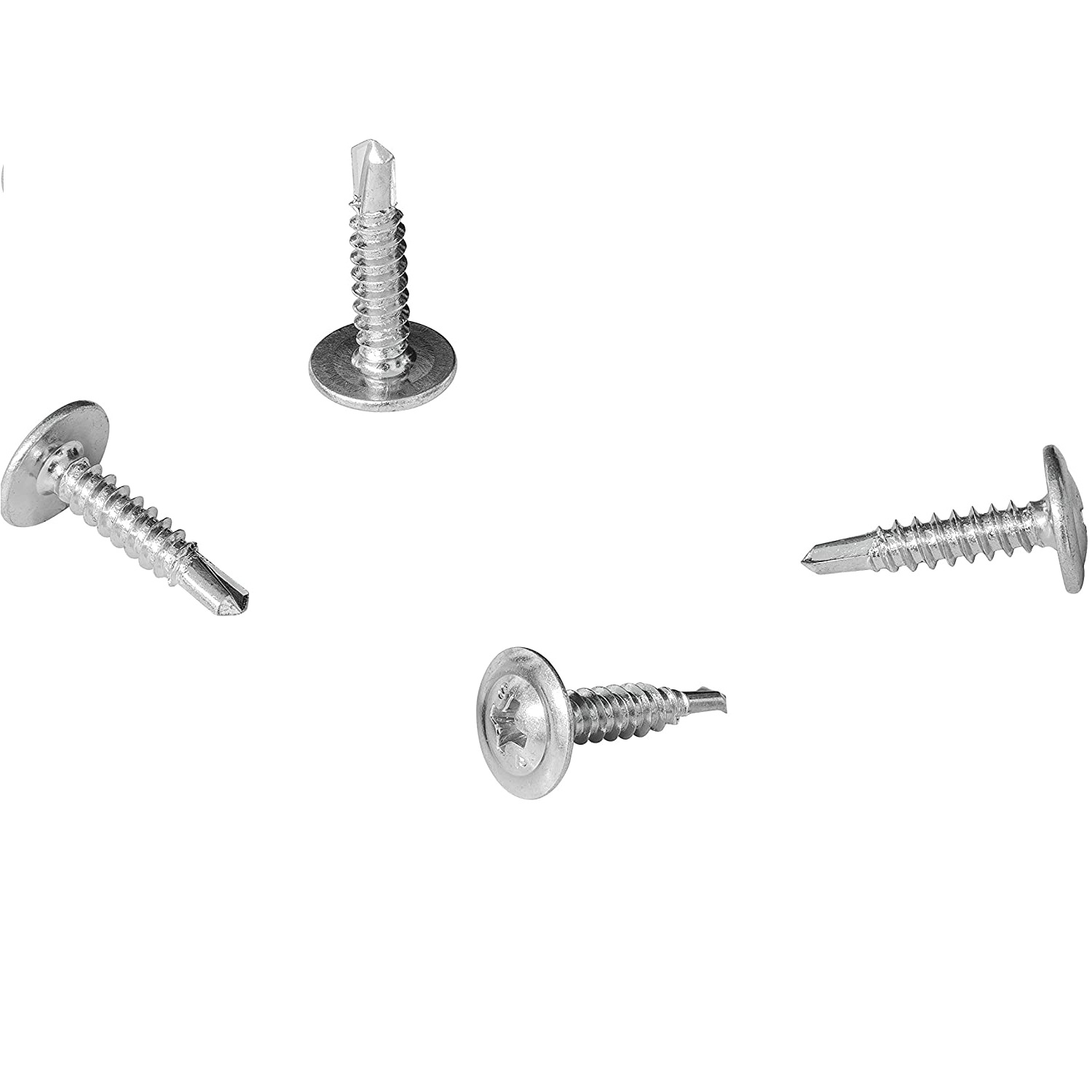
This screw is perfect for use in a variety of applications, but be careful – it may break when drilling into thicker metals. So if you’re looking for a reliable, sturdy screw for steel, this one might not be right for you.
PARTS EXPRESS #8 x 3/4″ Self-Tapping Truss Head Screws
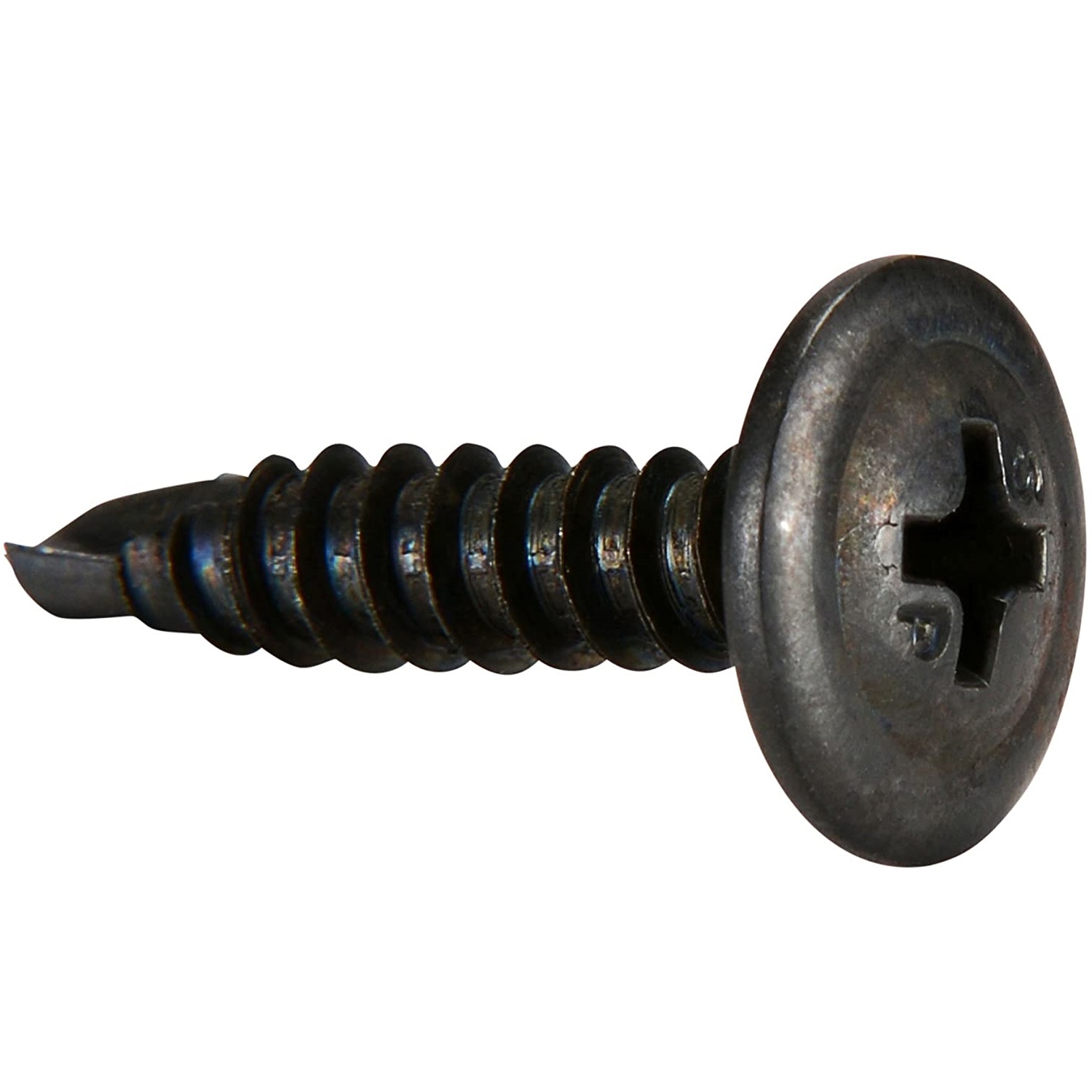
These Parts Express #8 x 3/4″ Self-Tapping Truss Head Screws are just the thing you need for a sturdier hold. But beware, they’re known to rust in humid environments and the manual can be misleading. Still, if you’re looking for extra support, these screws are perfect for the job.
410 Stainless #8 x 3/4″ Wafer Head Phillips Self Drilling Sheet Metal Tek Screws
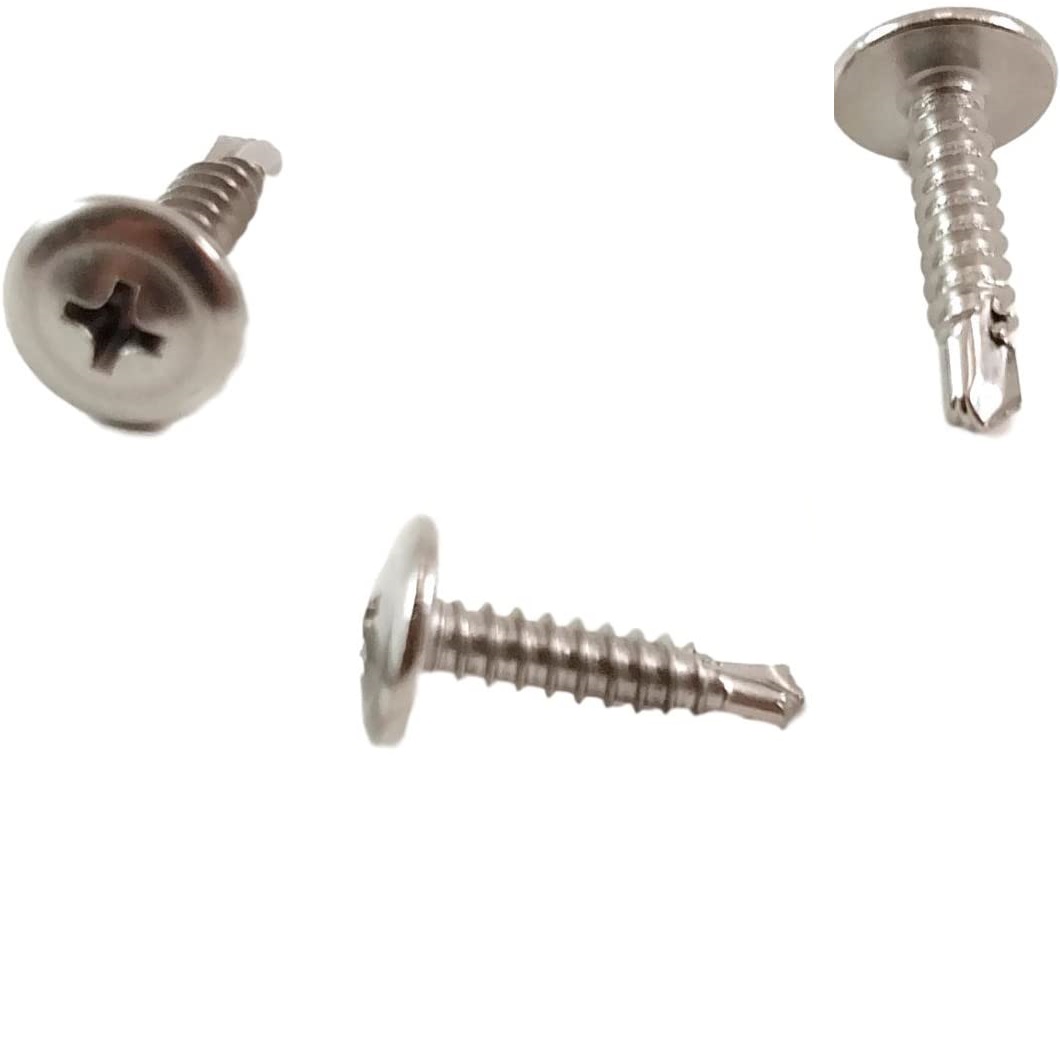
If you’re looking for an expensive way to screw things together, then look no further than these 410 Stainless #8 x 3/4″ Wafer Head Phillips Self Drilling Sheet Metal Tek Screws! The heads on these screws are soft and they may break when drilling.
What really sets our screws apart is the price. We know that quality comes at a cost, and these will be pricier than alternatives on the market. But watch out – some of the screws in this pack may not be made of stainless steel! Still, it is worth giving them a try. We’re sure you’ll be satisfied with the results.
Powerhead, Cab Screw, 10, 3 in, PK150
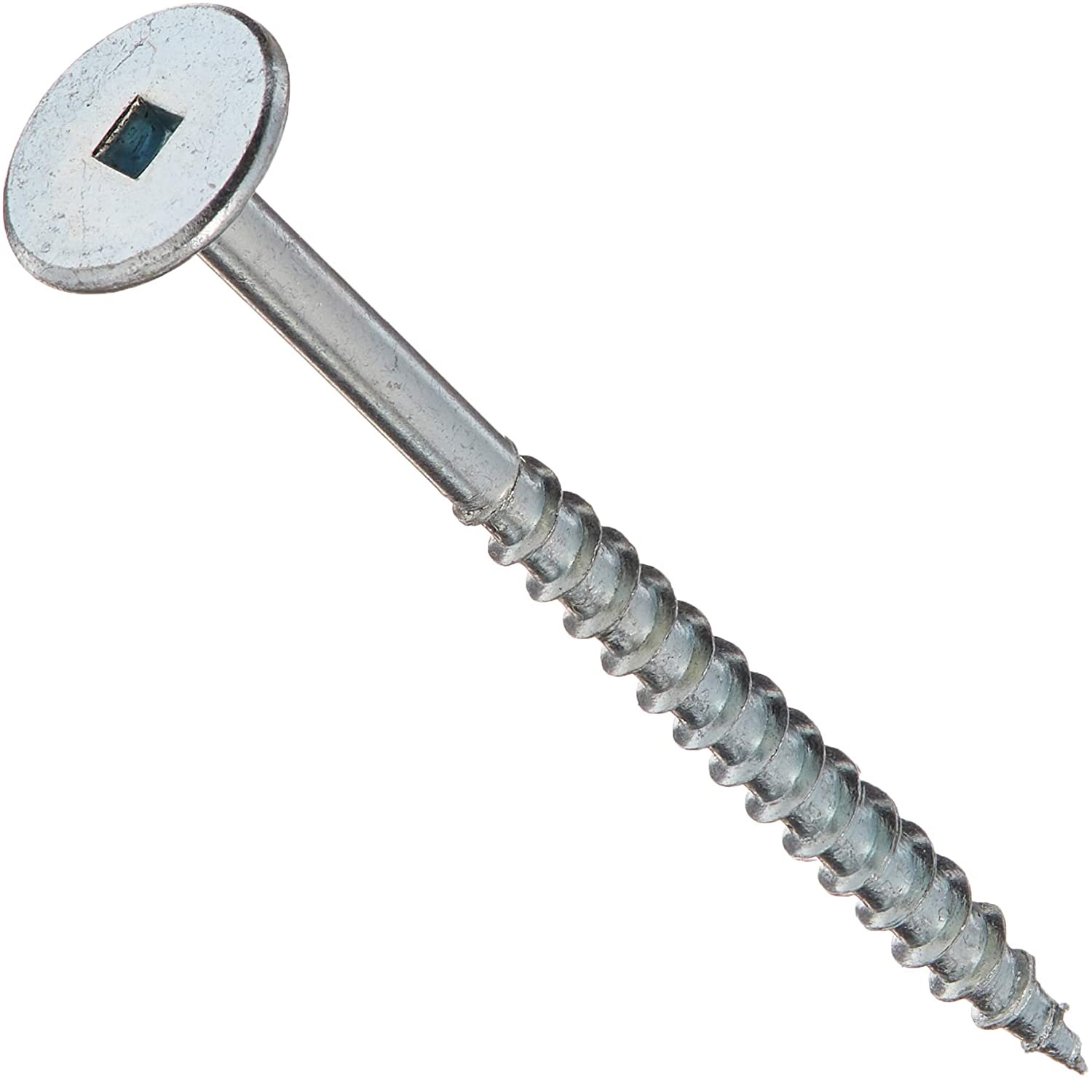
The Powerhead is a hard to drill screw. Its structure is not very durable so it might be prone to sptripping at times. Despite its many flaws, it is still used by many people because it is one of the only products available that can perform its specific function.
FASTCAP PHZ8.3-inch-50PC PowerHead 3-Inch Cabinet Installation Screws
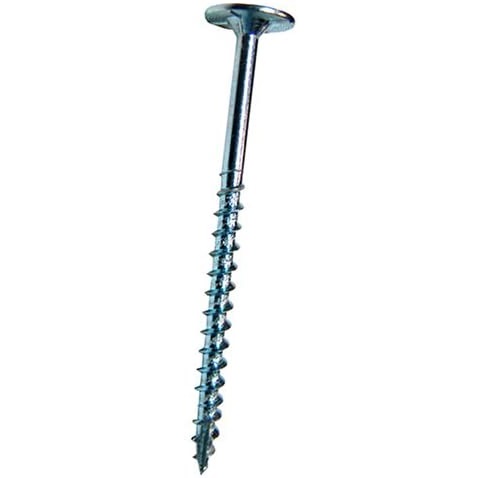
Buyers Guide
When Do You Need to Drill Your Metal Studs?
You need to drill your metal studs when you’re creating a hole for either functional or aesthetic purposes. For example, you might need to drill a hole in order to run some wiring, or you might want to hang a picture on the wall.
Before you start drilling, it’s important to take some time to figure out exactly where you want the hole to be. Once you’ve done that, mark the spot with a pencil so that you know where to drill. [1]
Will Every Screw Work for the Job?
No, not every screw will work well for drilling metal studs. In fact, you need to be very careful about which screws you use in order to avoid damaging your metal studs.
You should use screws that are specifically designed for metal studs. These screws will have a sharp point that can penetrate the metal and a strong grip so that they don’t slip out.
The best screws for metal studs are the ones that have a sharp point and are made of hardened steel. There are many different types of screws available, but the most important thing to consider is the type of head on the screw. The head should be able to grip the metal firmly without slipping.
Another important consideration is the length of the screw. Metal studs are often very thin, so it is important to choose a screw that is long enough to grip the stud securely, but not so long that it protrudes through the other side. If the screw is too long, it could come out the other side of the stud and cause damage. On the other hand, if the screw is too short, it might not grip the stud securely enough.
Finally, make sure that you get a set of screws that are the right size for your drill bit. If the screws are too big or too small, they could get stuck in the drill or strip the threading.
If you’re not sure which screws to use, ask a hardware store employee for help. They should be able to point you in the right direction. [1][2]
What Kind of Screws Are Ideal for Metal Studs?
There are a few different types of screws that can be used for metal studs. Let’s take a look at some of them.
Drywall screws
Drywall screws are a possible type of screw that is used for metal studs. Drywall screws come in a variety of lengths, so you should be able to find ones that are the perfect size for your project, but they aren’t the best choice for metal studs because they aren’t as strong as special screws for the job.
If you have no other choice however, for metal, fine drywall screws are usually the way to go.
They have a sharp point and can grip the metal firmly.Self-Tapping Screws
Self-tapping screws are a type of screw that can be used for a variety of materials, including metal. These screws have a sharp point that allows them to penetrate the surface without the need for a pre-drilled hole. They tap into the surface as they’re being screwed in, which creates a tight and secure hold.
Self-tapping screws also have threads that grip the material tightly. This ensures that the screw doesn’t loosen over time and fall out.
One advantage of self-tapping screws is that they’re relatively easy to use. You can simply insert them into the surface and turn them until they’re tight.
Another advantage is that they come in a variety of sizes and lengths, so you can find ones that are just right for you.
The main disadvantage of self-tapping screws is that they’re not always as strong as other types of screws. This is because the threads can strip easily, especially if you’re not careful. For this reason they should be drilled at slower speeds and may require pilot holes to be drilled beforehand.
If you’re going to be using self-tapping screws, make sure to get ones that are specifically designed for metal surfaces. These will be stronger and less likely to strip the threading.
Self-drilling screws
Self-drilling screws are a kind of self-tapping screws. These screws are intended to drill their own holes, as the name implies. This makes them very easy to use and saves you the trouble of having to pre-drill a hole.
The point is in the form of a sharp drill bit and this helps the screw to penetrate the metal surface. Threads being small ensures that less metal will be stripped down when drilling.
Self-drilling screws have several benefits. For example, they are extremely flexible and may be used on a variety of materials including wood, plastic, and, of course, metal.
Another advantage is that they’re relatively easy to use. You don’t need any special tools or knowledge in order to use them, which makes them a great option for DIY projects.
However, there are a few disadvantages to using self-drilling screws. One of the biggest problems is that they can be difficult to remove once they’ve been installed. This is because the sharp point can cause the screw to grip onto the metal surface very tightly.
What Can Happen If I Choose the Wrong Screw?
If you use the wrong screw when working with metal studs, a few things can happen. First, the screw might not penetrate the metal properly. This will cause it to slip out and strip the hole, making it impossible to get a good grip. Second, the wrong screw could break inside the metal stud, leaving you with a mess to clean up and a wasted piece of material. Third, using the wrong screw could cause damage to the surrounding materials, like drywall or wood framing. Choose your screws carefully to avoid these problems!
Choosing a proper drill bit is important as well. We recommend using twist bits made of carbide or cobalt for the best results. [1],[2],[3]
How to Drill Screws Into Metal Studs?
Once you have chosen the right screws, you need to drill pilot holes into the studs before driving in the screws. This will help to prevent stripping and ensure that the screws are driven in straight.
In most cases, you’ll want to use a power drill to make the job go faster. Just make sure to pick a good drill bit for the better results.
Locate the Metal Studs
Before you can start drilling, you need to find the studs. The easiest way to do this is with a stud finder. If you don’t have one, you can also try tapping on the wall until you hear a solid sound instead of a hollow one.
There are a few different types of stud finders, but the most common is the magnetic stud finder. These work by detecting the change in density when they pass over a stud. Or you can simply find one by knocking on the wall applying light force.
Find the Edge and Center of the Stud
Now that you’ve found the studs, you need to find the edges and center of each one. This will help you know where to drill the pilot holes and not compromise power by drilling them in the wrong places.
To find the edge of the stud, you can use either manual calculations or use your stud finder again, as it can identify the stud center.
Once you’ve found the edges and center of each stud, mark these locations with a pencil so that you know where to drill.
Use framing screws
It’s not a requirement to drill pivot holes with framing screws, as they can be self-drilling. This is probably the most secure option. If you decide to do this, make sure that you’re using the right drill bit.
When drilling with a power drill, start slowly and then increase the speed as needed.
Tighten each screw until it’s flush with the surface of the metal stud, but no further.If you decide on drilling the pilot holes however, use a drill bit that is slightly smaller than the diameter of the screw. This will allow the screw to grip the metal more securely. It’s recommended to drill at the slow speed to have more control over the process and the results.
Once all of the pilot holes have been drilled, you can start driving in the screws. Start with the longest screws first and work your way down to shorter screws. Use a power drill or impact driver to drive in the screws quickly and easily.
Be sure to countersink each screw so that the head is flush with or below the surface of the metal. This will ensure a smooth, finished appearance and prevent snagging on clothing or skin. [3],[4],[5]
Buyers Guide for the Best Screws for Metal Studs
Now it’s time to decide which screws are best for your project. With so many options on the market, it can be tough to know where to start. Here are a few things to keep in mind as you shop for the best screws for metal studs.
Quantity
First, consider how many screws you’ll need. This will depend on the size of your project and the type of screw you choose. If you’re not sure, it’s always better to buy more than you think you’ll need. It’s easier to return unused screws than it is to run out in the middle of a project. [1]
Compatibility With Material of the Stud
One of the most important corrosionings to consider when choosing screws for metal studs is the compatibility between the screw and the material of the stud.
Each type of metal has its own unique set of characteristics, so it’s important to choose a screw that will work well with the specific type of stud you’re using.For example, some studies have thicker gauge metal than others, which will require different types of screws. Be sure to check the thickness of your metal studs before selecting screws, and consult the manufacturer’s recommendations if possible.
Weight Capacity
One of the most important things to consider when choosing screws is the weight capacity. How much weight will the screw need to hold? If you’re hanging a heavy mirror or piece of artwork, you’ll need a screw that can handle the weight. Metal studs are strong, but they’re not indestructible. Choose a screw with a high weight capacity to be safe.
Usually you will want screws with a weight capacity of at least 50 pounds. Pick a screw that can hold more weight that you’re planning on using it for for extra safety.
Another important factor to keep in mind is the thickness of the metal stud. Thicker metal studs can handle more weight than thinner ones, so it’s important to choose a screw that will work well with the specific type of stud you’re using.
In general, screws with a thicker gauge are stronger and can handle more weight. But they also require more force to drive into the stud, so make sure you have a good drill or impact driver before attempting to install them.
Once you’ve considered all of these factors, you’re ready to choose the best screws for your project. Here are our top picks for the best screws for metal studs. [1]
Material of the Screw
The most important factor to consider when choosing a screw is the material. Metal screws are made from a variety of metals, including steel, brass, and aluminum. Each type of metal has its own advantages and disadvantages.
Steel screws are the strongest option and come at an affordable price. If you need a screw that’s going to stand up to a lot of wear and tear, then steel is the way to go. For these reasons, steel screws are extremely common.
Aluminum screws are the weakest option but they’re also the most affordable and lightweight. If you’re not concerned about strength, then aluminum is a good choice.
Stainless steel screws are the best choice for outdoor use because they’re both strong and corrosion resistant. However, they are more expensive than other options.
Titanium screws are the strongest and most expensive option. They’re often used in aerospace applications because of their high strength-to-weight ratio.
Keep in mind that different metals will have different degrees of corrosion resistance. If you’re using your metal studs outdoors or in humid conditions, you’ll want to choose a screw with good corrosion resistance. Stainless steel screws are the most resistant to corrosion. Aluminum screws are the least resistant to corrosion but they’re still suitable for most indoor applications. [6]
Size and Length
One of the most important factors to consider when choosing screws is size. Metal studs are typically thinner than wood studs, so you’ll need a screw that’s long enough to penetrate the metal and reach the wallboard or other material behind it.
Another factor to consider is head size. The head of the screw should be large enough to grip the metal firmly, but not so large that it prevents the screw from being driven all the way into the stud. A Phillips or flat head screw is typically best for metal studs.
Thread count is also important. The higher the thread count, the more holding power the screw will have. [1]
Read related guide: Best Metal Roofing Screws
FAQ
How do you screw into metal studs?
To screw into metal studs, you will need to use a drill and a screwdriver bit that is compatible with the type of screws you are using. First, drill a pilot hole into the stud using a small drill bit. Next, insert the screwdriver bit into the chuck of your drill and then carefully insert the tip of the screw into the pilot hole. Finally, use the drill to drive the screw into the stud until it is tight. Repeat this process for each screw you need to install.
If you’re working with particularly hard or thick metal studs, you may need to use self-tapping screws. These screws have sharp threads that can cut their own way through metal as they’re being installed. However, self-tapping screws are more likely to strip out, so be sure to use a lower speed when installing them.
Do you need special screws for metal studs?
The short answer is not really. You can use drywall screws if you want to, but there are certain screws that will make your life a lot easier when working with metal studs.
For better security, you should use screws that are specifically designed for metal studs. These screws have sharp points and threads that grip the metal well. They also have special coatings that prevent rusting.
If you plan on using drywall screws, make sure they are fine-threaded and long. Shorter screws will not grip the metal as well and will strip more easily.
Can you use lag screws in metal studs?
Yes, you can use lag screws in metal studs, but make sure to use the proper size and length screw for the job. It is also important to note that lag screws are not meant to be removed and reused, so be sure you have the correct size and type of screw before beginning your project.
Lag screws are typically used in woodworking projects, but can also be used in metal studs when attaching heavier objects such as cabinets or shelves.
Useful Video: Which screw to use… wood and metal screws introduction
Conclusion
So, what’s the best screw for metal studs? The answer to that question depends on a variety of factors, including the size of the screw, weight capacity, material and quantity. We’ve covered 5 of the most popular screws for metal studs on the market in this blog post, but there are many more options available. Do your research before making a purchase and always consult with a professional if you have any questions or concerns. By following these tips and choosing the right screws for your project, you can rest assured that your metal stud installation will be successful.
References:
- https://drilling-it.com/screws-for-metal-studs-reviews/
- https://allpointsfasteners.com/blog/screws-for-metal-studs.html
- https://topcordlesstools.com/blog/how-to-drill-into-metal-studs/
- https://www.hunker.com/13418484/how-to-drill-into-metal-studs
- https://www.handymanjoes.com/a-quick-guide-to-drilling-through-metal-studs/
- https://allpointsfasteners.com/blog/four-common-materials-screws-are-made-of-which-to-use.html