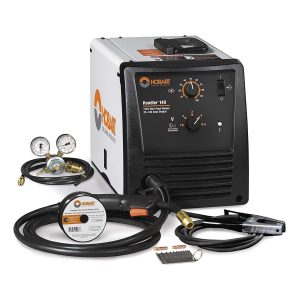
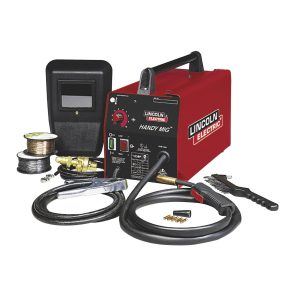
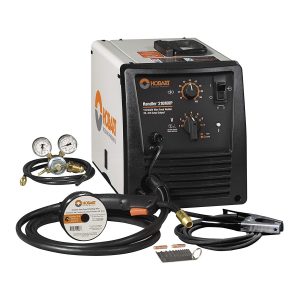
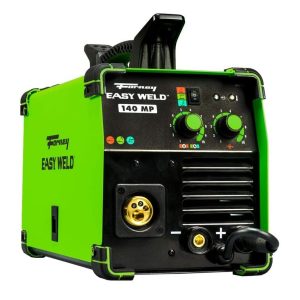
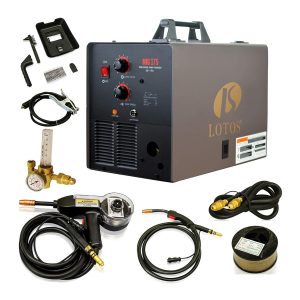
Choose the Best MIG Welders for Aluminum
Customer’s Choice: the Best Rated MIG Welders for Aluminum
18 users answered this survey. Please help us improve this review!
MIG Welders are an important tool for any welder. They offer a lot of benefits, such as being easy to use and versatile. When it comes to welding aluminum, you need to have a MIG Welder that is designed specifically for the task. This epic guide will discuss everything you need to know about MIG Welders for aluminum welding! It will cover common questions, such as “What is the best MIG Welder for aluminum?” and “What are the benefits of using a MIG Welder for aluminum?” The article will also provide reviews of some of the best MIG Welders for aluminum on the market today!
Hobart Handler 140 MIG Welder, 115 V
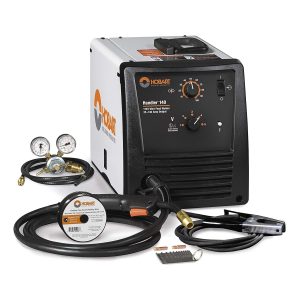
And since it’s compatible with 115-V standard household current, you won’t need to worry about special equipment or permits. So, whether you’re looking to weld steel, aluminum, or stainless steel, the Hobart Handler 140 MIG Welder is the perfect tool for the job.
Lincoln Electric K2185-1 Handy MIG Welder
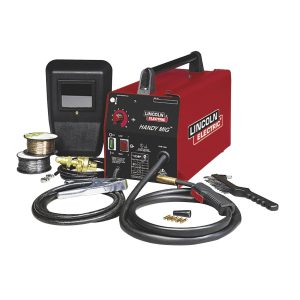
The included work cable and clamp make it easy to connect to your power source, and the gas nozzle, gas regulator and hose make it easy to set up gas-assisted welding. This welder comes with everything you need to get started on your next project, making it the perfect choice for any home handyman or woman.
Hobart – 500553 Handler 210 MVP MIG Welder
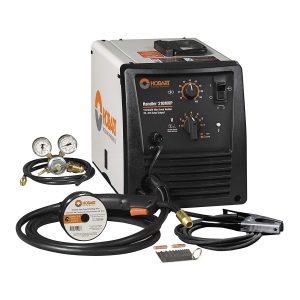
Plus, the built-in gas solenoid keeps wire electrically “cold” until the trigger is pulled, allowing you to fine control the output parameters. This welder is suitable for material thicknesses from 6.35 mm to 9.5 mm.
Forney Multi-Process Welder, 140 MP
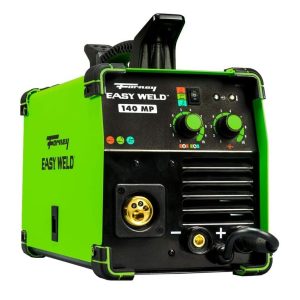
This welder can be used as a stick welder, MIG Welder and DC TIG Welder, making it the perfect tool for any welding project. The three-position switch allows for quick change between processes, and the 20-cm ground clamp ensures a secure connection. With a rated output current range of 43 – 110 A, the Forney Multi-Process Welder can handle any job.
The integrated handle and torch wrap make it easy to transport and use, while the all-metal case ensures durability. This welder also includes a 20A – 15A adapter and a 20-cm electrode holder. Forney is a trusted name in welding, so you can be confident in the quality of this product.
LOTOS MIG175 175AMP MIG Welder, Brown
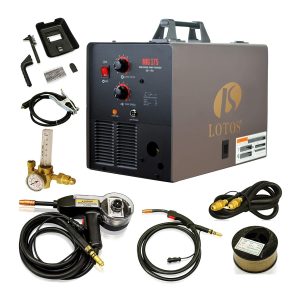
The mask and 3.1-m cable make it easy to stay safe while you work. This welding machine is based on durable and reliable transformer technology, making it a great choice for anyone looking for a long-lasting and reliable welding solution.
Buyer’s Guide
What type of welding can you use to weld aluminum?
TIG welding
This type of welding is best for welding aluminum. TIG welders use a non-consumable tungsten electrode to create the arc. This type of welder is also good for welding other metals, such as stainless steel and copper.
To use TIG welding, you will need to have a gas tank and an Argon gas regulator. You will also need a TIG welding torch, which is available at most welding supply stores.
The main advantage of TIG welding is that it produces very little spatter and can be used to weld thin materials. It is also a very clean type of welding, which means there is less cleanup after the job is done.
MIG welding
MIG welding is another type of welding that can be used to weld aluminum. MIG welders use a wire that is fed through a gun, which melts and fuses the metal together.
MIG welding is a good choice for projects where speed is important. It is also less expensive than TIG welding, which makes it a good choice for beginners.
The main disadvantage of MIG welding is that it produces more spatter than TIG welding. This means that there will be more cleanup after the job is done.
Torch welding
Torch welding is a type of welding that uses a torch to create an arc. This type of welding is best for thick materials, such as aluminum.
To use torch welding, you will need a gas tank and an oxygen regulator. You will also need a torch, which is available at most welding supply stores.
It is also a good choice for projects where speed is important.
The disadvantage of torch welding is that it can be difficult to control the heat, which can lead to the warping of the metal [1].
How does MIG Welder for Aluminum work?
MIG welding is an arc welding process that uses a wire electrode and an inert gas to weld metal. The “wire” part of MIG welding refers to the fact that a thin, continuous wire electrode is fed through the welding gun and into the weld pool. This wire electrode can be made of different metals, including aluminum.
The “inert gas” part of MIG welding refers to the fact that an inert gas (usually – argon) is used to shield the weld pool from contaminants in the air. This protects the weld pool from oxygen and other impurities that can weaken or destroy the weld.
When you pull the trigger on a MIG welder, two things happen:
- An electrical current is passed through the wire electrode, which heats the metal and creates an arc.
- The inert gas is released from the welding gun, which surrounds the weld pool and protects it from impurities.
The heat of the arc melts the aluminum wire electrode and the base metal, and the inert gas shielding prevents oxygen and other impurities from contaminating the weld pool. This produces a strong, high-quality weld.
MIG welding is a great choice for welding aluminum because it’s fast, easy to learn, and relatively inexpensive. It’s also possible to get great results with MIG welding if you have access to quality equipment and know how to use it properly [2].
How can you clean aluminum workpieces?
There are a few ways to clean aluminum workpieces before welding. You can use a wire brush, sandpaper, or a chemical degreaser. If you’re using a chemical degreaser, make sure to follow the manufacturer’s instructions and wear gloves and protective eyewear. To clean with a wire brush, attach the brush to the power drill and hold it at a slight angle to the aluminum surface. Use light pressure and make sure to brush in the direction of the grain. For sandpaper, use 220-grit or higher and sand in the direction of the grain.
After you’ve cleaned the aluminum workpieces, it’s important to remove any debris before welding. The best way to do this is with compressed air. Hold the nozzle about six inches from the surface of the workpiece and move it back and forth until all of the debris has been removed.
What to Search for When Purchasing a MIG Welder for Aluminum?
Wire Feed Speed and Amperage
The next thing you need to take into account is the wire feed speed and amperage. The wire feed speed is how fast the electrode is pushed through the machine. This setting is important because it can affect how well the weld penetrates the metal. The amperage is also important because it determines how hot the arc is. If the arc is too hot, it can cause the metal to distort.
There are a few things that you need to keep in mind when setting the wire feed speed and amperage. First, you need to make sure that the wire feed speed is fast enough so that the electrode doesn’t melt before it reaches the workpiece. Second, you need to set the amperage high enough so that the weld penetrates the metal but not so high that it causes distortion.
The average amperage for aluminum welding is between 150 and 200 amps.
Duty Cycle
The duty cycle is the amount of time that the welder can be used before it needs to be turned off to cool down. The duty cycle is important because it determines how long you can weld before you need to take a break.
Most MIG welders have a duty cycle of 20%. This means that you can weld for two minutes and then you need to turn the welder off for eight minutes so that it can cool down.
Some MIG welders have a higher duty cycle, which means that they can be used for longer periods without needing to be turned off. The highest duty cycle can be found on industrial MIG welders and is 60% [3].
Heat Control
The last thing you need to take into account is heat control. The heat control determines how hot the arc is. If the arc is too hot, it can cause the metal to distort. The heat control on MIG welders is usually adjustable. This means that you can set it to the level that you need for the particular job that you’re doing. The lowest level is usually around 50% and the highest level is around 100%.
Most MIG welders have a heat control that goes from low to high. However, some MIG welders have a two-stage heat control. The average heat control for aluminum welding is between 50% and 70%.
Output Power
The output power is the amount of power that the welder can produce. The output power is important because it determines how hot the arc is. If the arc is too hot, it can cause the metal to distort.
The output power on MIG welders is usually between 100 and 200 amps. The higher the output power, the hotter the arc will be.
Keep in mind that you need to set the amperage high enough so that the weld penetrates the metal but not so high that it causes distortion.
Digital display
A digital display is a nice feature to have on a MIG welder. The digital display shows the current settings for the welder. This can be helpful when you’re trying to set the welder to the correct settings. Mostly it can show the welding speed, amperage, and wire feed speed.
Most MIG welders have an analog control panel. This means that you need to use a knob to set the welding speed, amperage, and wire feed speed.
Material Thickness
The material thickness is important because it determines how much heat the welder can handle. If the material thickness is too thick, it can cause the welder to overheat.
Most MIG Welders can weld materials that are up to 6,36 mm thick. Some MIG Welders can weld materials that are up to 12,7 mm thick. Moreover, some MIG Welders can weld materials that are up to 25,40 mm thick. These welders are usually more expensive.
You should always check the owner’s manual to see what the maximum material thickness is for the welder. When welding aluminum, you need to use a wire that is specifically made for aluminum. The most common sizes are .035 and .045. The size of the wire will determine how thick the metal can be that you’re welding.
For example, if you’re using a .035 wire, you can weld materials that are up to 24 ga thick. If you’re using a .045 wire, you can weld materials that are up to 12 ga thick.
Gas or Gasless
The last thing you need to take into account is whether you want a gas or gasless welder. Gas welders use a shielding gas to protect the weld from oxygen. This makes them more expensive than gasless welders. However, they’re also more versatile because you can use them on a variety of materials.
Gasless welders don’t use a shielding gas. They’re less expensive than gas welders but they’re not as versatile.
Portability
Portability is another factor to consider when choosing a welder.
Most MIG welders are portable but some are not. The portability of the MIG Welders is provided by wheels or a handle.
Some MIG welders have both wheels and a handle. This makes them very easy to move around. Other MIG welders only have one or the other. The wheels are usually made of plastic and the handle is usually made of metal. If you’re going to be welding in different locations, then you need to get a portable welder. Otherwise, you can get a welder that is not portable.
Additional Features
Some MIG Welders come with additional features that can be helpful. These features include:
- A spool gun: This is a gun that is specifically designed for welding aluminum. It’s not necessary but it can make the job easier.
- A built-in wire feeder: This is a feature that allows you to feed the wire through the welder without having to use an external wire feeder.
- A carrying case: This is a nice feature to have if you plan on taking the welder with you to different locations.
These are just some of the features that you may want to look for in a welder. Not all welders have these features so you’ll need to decide which ones are important to you [4].
How to use the MIG Welders in steps?
The MIG Welders can be used by different home projects or commercial purposes. Here are the steps on how to use it:
- Choose the right welder. You need a welder that has enough power to weld thick aluminum. If you’re not sure, ask an expert or read reviews online.
- Get the correct gas. Argon gas is typically used for welding aluminum.
- Set up your welder. Follow the instructions in your welder’s manual to set up your machine properly.
- Clean your materials before welding them together. This will help create a stronger bond between the two pieces of metal.
- Weld your materials together using the MIG welder following all safety precautions listed in your welder’s manual [5].
How to maintain the MIG Welders?
It is important to maintain your MIG Welder to ensure its longevity and performance. Here are some tips on how to do so:
- Regularly clean the machine, including the torch, tip, gas cup, and work cable. This will prevent dirt and debris from building up and affecting the quality of your welds.
- Check for any damaged or worn parts that need to be replaced.
- Make sure that all connections are tight and secure.
- Store the machine in a dry and well-ventilated area when not in use.
By following these simple tips, you can keep your MIG Welder in good condition for years to come. The manufacturers can offer different warranties for the product if you maintain the welder in perfect condition. On average, a MIG Welder can last for about 3000 hours before any major maintenance is required [6].
Comparison of Key Indicators for Choosing MIG Welders for Aluminum
When selecting a MIG welder for aluminum, it’s crucial to consider various indicators that will impact the welding process and end results. This table provides a comparison of important factors to consider when choosing a MIG welder specifically for aluminum welding. The indicators include amperage range, wire feed speed range, duty cycle, and gas requirements.
Indicator | Ideal Range |
---|---|
Amperage Range (A) | 30 – 500 |
Wire Feed Speed Range (IPM) | 50 – 1500 |
Duty Cycle (%) | 30% – 60% |
Gas Requirement | Argon or Argon-Helium mixture |
Explanation:
- Amperage Range (A): For aluminum welding, an ideal MIG welder should have an amperage range between 30 and 500 amps. This wide range allows for versatility in welding different thicknesses of aluminum.
- Wire Feed Speed Range (IPM): The ideal wire feed speed range for aluminum MIG welding typically falls between 50 and 1500 inches per minute (IPM). This range provides flexibility in controlling the deposition rate of the welding wire.
- Duty Cycle (%): The duty cycle represents the percentage of time a welder can operate within a 10-minute period without overheating. For aluminum welding, a MIG welder with a duty cycle between 30% and 60% is recommended to ensure continuous operation and minimize downtime.
- Gas Requirement: Aluminum MIG welding typically requires the use of shielding gas such as argon or an argon-helium mixture. The specific gas requirement may vary depending on the welding process and material thickness.
Please note that the values provided in the table are general guidelines and may vary depending on the specific requirements of your welding project.
FAQ
What type of welder is best for aluminum?
There is no definitive answer to this question as it depends on several factors, such as the thickness of the aluminum being welded and the type of welding being done. However, MIG welders are generally considered to be the best type of welder for aluminum welding.
MIG welders are easy to use and can be used for a variety of different applications. They are also relatively inexpensive, which makes them a good choice for those who are just starting with aluminum welding.
Can you use any MIG welder for aluminum?
Not all MIG welders are suitable for welding aluminum. Some MIG welders do not have a setting that is specifically designed for welding aluminum, which means that they may not be able to produce the correct amount of heat needed to weld aluminum properly.
It is important to check the specifications of a MIG welder before purchasing it to make sure that it can be used for welding aluminum. MIG Welding Aluminum requires special techniques, torch angle, gas, and wire feed speed. If you don’t have the right machine or settings, you will most likely create lots of spatter and frustration.
What’s the difference between MIG and TIG welding?
MIG welding is a type of welding that uses an electric arc to weld metal together. The metal is fed through a wire that is melted by the heat of the arc and then joins the two pieces of metal together.
TIG welding is a type of welding that uses a tungsten electrode to weld metal together. The tungsten electrode produces an electric arc that heats the metal, which melts and joins the two pieces of metal together.
Both MIG and TIG welding can be used for aluminum welding, but TIG welding is generally considered to be better suited for aluminum because it produces a cleaner weld.
How do I set up a MIG welder?
Most MIG welders are easy to set up and use. The first thing you need to do is connect the welder to an electrical outlet and then turn it on.
Next, you need to select the correct wire speed and gas flow rate for the aluminum being welded. The correct settings will vary depending on the thickness of the aluminum being welded.
Once the welder is turned on and set to the correct settings, you can start welding!
Which metals can I meld with a MIG welder?
MIG welders can be used to weld a variety of different metals, including aluminum, steel, and stainless steel. You should check the specifications of your welder to see which metals it is designed to weld. Some welders are only suitable for welding one type of metal, while others can weld a variety of different metals.
What is flux-core wiring, and can my welder use it?
Flux-core welding is a type of welding that uses a wire that is coated in flux. The flux helps to protect the weld from contamination and also provides extra heat to the weld, which can help to improve the quality of the weld.
Not all MIG welders can use flux-core wire. Some MIG welders are only designed for use with solid wire. If you are not sure whether your welder can use flux-core wire, you should check the specifications of your welder or consult the manufacturer.
Why should I avoid live torches?
Live torches are a type of welding torch that produces an electric arc between the electrode and the workpiece. This can be dangerous because the electric arc can cause serious injuries if it comes into contact with your skin.
You should avoid using live torches unless you are experienced in welding and know how to use them safely. If you are not experienced, you should use a MIG welder instead.
MIG welders do not produce an electric arc between the electrode and the workpiece, so they are much safer to use than live torches.
What are weld strength requirements?
The weld strength requirements will vary depending on the application. For example, if you are welding a load-bearing joint, the weld must be strong enough to support the weight of the load.
You should consult an engineer or other expert to determine the weld strength requirements for your specific application.
What to consider when choosing MIG Welders?
There are a few things you should consider when choosing a MIG welder, such as the amperage range, duty cycle, wire feed speed, and price.
The amperage range is the range of amperages that the welder can produce. The larger the amperage range, the more versatile the welder will be.
The duty cycle is the percentage of time that the welder can be used before it needs to be turned off to cool down. A higher duty cycle means that the welder can be used for longer periods without needing to be turned off.
The wire feed speed is the rate at which the wire is fed through the welder. A higher wire feed speed means that the welder can weld faster.
The price is another important consideration. MIG welders can range in price from a few hundred dollars to several thousand dollars. You should choose a welder that fits your budget and needs. On average, the effective MIG Welder for Aluminum can cost you around 600 euros.
What are the easiest types of welding to learn?
MIG welding and flux-core welding are generally the easiest types of welding to learn. This is because they do not require as much skill as other types of welding, such as TIG welding.
If you are a beginner, you should start with MIG or flux-core welding. Once you have mastered these techniques, you can move on to more difficult types of welding.
Why do aluminum welds crack?
Aluminum welds can crack for a variety of reasons, such as improper welding techniques, contamination, or excessive heat. If you are having trouble with your aluminum welds cracking, you should consult a welding expert to determine the cause of the problem and how to fix it.
There are a few things you can do to prevent your aluminum welds from cracking, such as using the proper welding technique, keeping your work area clean, and avoiding excessive heat.
How many times can you weld aluminum?
There is no definitive answer to this question because it will depend on the thickness of the aluminum, the type of weld, and the welding conditions.
In general, you can weld aluminum multiple times without causing any damage. However, if you are welding thick aluminum or using a high-heat weld, you may need to limit the number of times you weld to prevent damage.
What is the recommended voltage and wire speed setting for welding aluminum with a MIG welder?
To achieve successful aluminum welding with a MIG welder, it is important to set the voltage and wire speed correctly. Typically, for aluminum welding, a higher voltage and wire speed are required compared to welding other metals. The recommended starting point for voltage is around 18-20 volts, but it may vary depending on the specific welder and aluminum thickness. Similarly, the wire speed should be set higher than when welding steel or other materials. It is advisable to consult the welder’s manual or follow the manufacturer’s recommendations for the specific model you are using.
What shielding gas should I use for MIG welding aluminum?
When MIG welding aluminum, it is crucial to use the appropriate shielding gas to protect the weld from contamination and ensure proper fusion. The most commonly used shielding gas for aluminum MIG welding is 100% argon. Argon provides excellent coverage and minimizes the risk of porosity in the weld. It is essential to ensure a steady flow of shielding gas throughout the welding process to maintain a protective atmosphere around the weld area.
What type of wire should I use for MIG welding aluminum?
Choosing the right wire is vital for successful aluminum MIG welding. For welding aluminum, you should use aluminum wire specifically designed for MIG welding. Aluminum welding wire is softer than steel wire to accommodate the unique characteristics of aluminum. It is typically available in a variety of alloys, such as ER4043 or ER5356, each offering different properties and suitability for specific applications. Consult the wire manufacturer’s recommendations or seek guidance from welding experts to select the most appropriate wire for your aluminum welding project.
Why is pre-cleaning the aluminum surface important before MIG welding?
Prior to MIG welding aluminum, it is crucial to thoroughly clean the surface of the aluminum to remove any dirt, oil, grease, or oxidation. Aluminum forms a layer of oxide on its surface, which can hinder proper weld penetration and lead to weak or flawed welds. Pre-cleaning the aluminum surface using a stainless steel brush or an aluminum-specific cleaner helps remove these contaminants and ensures a clean surface for optimal weld quality. It is essential to clean the surface immediately before welding to prevent recontamination.
Do I need to use a spool gun for MIG welding aluminum?
Using a spool gun is highly recommended for MIG welding aluminum. Aluminum wire is relatively soft and prone to tangling or bird-nesting when fed through a regular MIG gun with a long cable. A spool gun, which holds the wire spool near the gun, minimizes the distance the wire travels and reduces the likelihood of wire feeding issues. The shorter distance also helps maintain better control over the wire feed speed and improves the overall welding performance when working with aluminum.
What techniques can I use to prevent distortion while MIG welding aluminum?
Aluminum has a high thermal conductivity, which makes it more susceptible to distortion during the welding process. To minimize distortion, you can employ various techniques:
- Use proper fit-up and tack welds to ensure precise alignment before welding.
- Use clamps or fixtures to hold the workpiece in place, reducing the likelihood of movement.
- Employ a stitch or skip welding technique, which involves welding short sections at a time, allowing each section to cool before continuing.
- Consider using a back purging technique when welding thicker aluminum sections to prevent excessive heat buildup and reduce distortion.
By employing these techniques, you can help minimize distortion and maintain the desired shape and dimensions of the aluminum weld.
What safety precautions should I take when MIG welding aluminum?
When MIG welding aluminum, it is important to prioritize safety. Here are some essential safety precautions:
- Wear appropriate personal protective equipment (PPE), including a welding helmet with a shade suitable for aluminum welding, welding gloves, a welding jacket, and safety glasses.
- Ensure proper ventilation in the welding area to remove fumes and gases generated during the welding process.
- Keep a fire extinguisher nearby and be aware of potential fire hazards, such as combustible materials.
- Avoid touching the electrode or workpiece with bare skin immediately after welding, as they can remain hot and cause burns.
- Follow electrical safety guidelines and ensure proper grounding of the welding equipment.
Always prioritize safety and follow recommended practices to protect yourself and others while MIG welding aluminum.
Useful Video: MIG Welding Aluminum – Weld Training
Conclusion
The MIG Welders for Aluminum that we’ve looked at today are all great machines that will get the job done, no matter what your requirements are. With these devices, you can fulfill such projects as fixing a broken table leg, creating a new mailbox, or even building a brand new car. Just remember to take your time in choosing the welder that’s right for you so that you can enjoy years of flawless welding performance. The effective models allow for a cleaner, more consistent weld, which is essential when you’re working with such a difficult metal. With the right machine, you can create beautiful projects that will stand the test of time – so don’t wait any longer, get welding!
References:
- https://www.uti.edu/blog/welding/aluminum-welding
- https://makemoneywelding.com/mig-welding-aluminum-for-beginners/
- https://www.lindedirect.com/about-us/blogs/productivity-matters/productivity-matters
- https://dirtydragonfab.com/mig-welder-buying-guide-10-welder-shopping-tips/
- https://www.instructables.com/Basics-of-MIG-Welding/
- https://americantorchtip.com/blog/10-mig-welder-maintenance-tips/