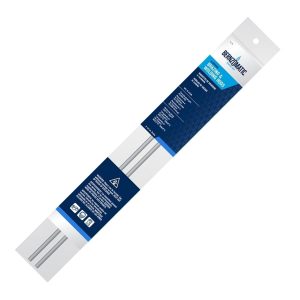
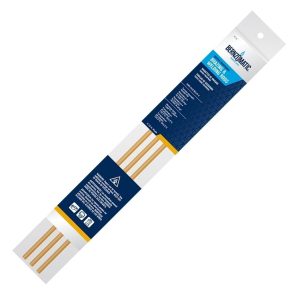
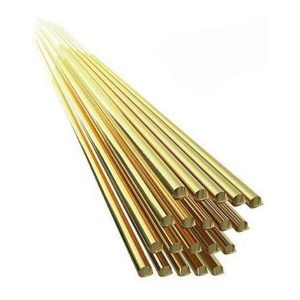
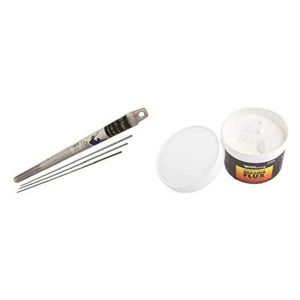
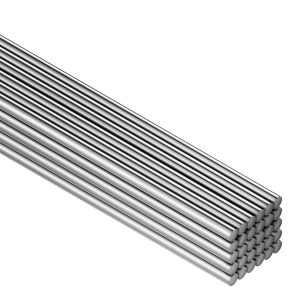
Choose the Best Aluminum Brazing Rod
Customer’s Choice: the Best Rated Aluminum Brazing Rods
321 users answered this survey. Please help us improve this review!
The world of brazing rods can be a confusing one. There are so many on the market, and each has its own set of pros and cons. In this buyer’s guide, we will review some of the best aluminum brazing rods available today. We will also compare these to other types of materials as well as discuss what you should consider when looking for your next rod purchase!
Bernzomatic AL3 Aluminum Brazing
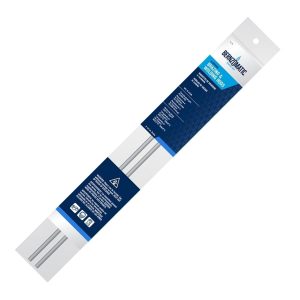
A working temperature of 700-750 degrees may be achieved with this brush, which is produced in the United States.
Bernzomatic PC3 Copper-Phosphorus Brazing
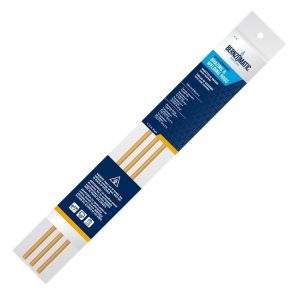
With no flux, joins copper to copper without the use of solder. Also joins copper to copper alloys (brass and bronze).
Blue Demon Low Temp Aluminum-Zinc Brazing Rod with Flux
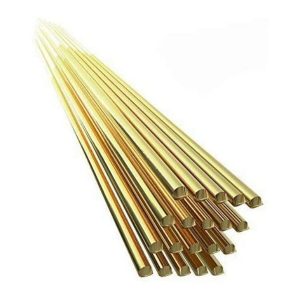
There are around 18-20 sticks in each tube.Borax is a kind of flux that cleans easily to enable for excellent solid brazing jobs.
50 Pieces Aluminum Welding Rods
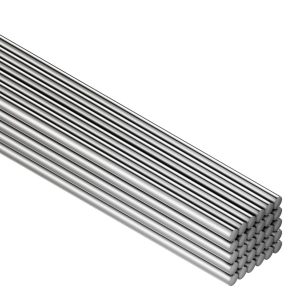
Made of aluminum, which has excellent weldability, thermal conductivity, electric conductivity, and processing capability. The inner part is formed with a powder core for a smooth welding effect. Diameter: 2 mm/ 0.08 inch; Length: 200 mm/ 8 inch.
No additional flux powder is needed: the aluminum welding rod contains solder powder, so you don’t need to use any extra flux with aluminum alloys because of the salt base. It’s convenient and easy to weld.
It’s simple to operate: heat the base metal, not the rod, to a temperature of 716-752 degrees Fahrenheit (380-400 degrees Celsius) until the wire cools enough for you to weld it safely.
Our aluminum brazing rods can be used to mend just about any metallic item, from pots and pans to vessels and fences. They’re also suitable for filling material for pure aluminum cooking, connection with aluminum bus and guide rod of an electrolytic aluminum plant, electric power, chemistry (filling material), food (connection with aluminum bus and guide rod.
Buyer’s guide
Will the brazing rod stick to aluminum? How?
If the stick will not attach to aluminum, it is likely that you have a bad alloy or dirty base metal. To test this theory , put some flux on your rod and apply heat from an acetylene torch. If the brazing material won’t stick, use another brand of materials for brazing aluminum a professional Brazer will use a flux-coated rod, as the coating helps the molten metal flow and adhere to the base metal.
The best aluminum brazing rods are those that have a higher melting point than the alloy being joined. A lower-melting-point rod will cause the alloy to liquefy, which can lead to contamination and poor quality joints.
The rod should also have a higher tensile strength than the alloy being joined. This will help ensure that the joint doesn’t break under stress.
When selecting a brazing rod, it is important to consider the base metal you are working with. Different alloys require different types of rods in order to create a strong and durable joint.
A rod that can`t stand up to these conditions will result in a weaker joint and an unreliable connection between your alloy pieces.
While there are many factors involved when choosing the best aluminum braze rods for your project, following these simple tips should get you started on the right track.
How to braze with aluminum rods
Aluminum brazing rods are a great way to join aluminum parts. Brazing differs from welding in that it does not involve melting the base metal, but rather heating alloy filler wire until it liquefies and then allowing the melted material to flow into joint gaps of two or more pieces of metal. It is ideal for joining thin materials, such as sheet metal and tubing, because it does not cause the base metals to become molten.
The filler wire used for brazing alloys may contain tin, silver, copper and other metals. The most common filler wire for aluminum brazing is a copper-zinc alloy, which has a low melting point and therefore requires lower heating temperatures than other alloys.
When using an aluminum brazing rod to join two pieces of metal, it is important to clean the surfaces of both parts thoroughly. Any contaminants on the surface will prevent the filler wire from bonding to the metal. The best way to clean the surface is with a wire brush.
Once the surfaces are clean, it is important to flux them properly. Flux helps to remove any oxides that may have formed on the surface of the metal and also acts as a protective coating against corrosion. There are many types of flux available, but the most common is a paste flux.
After fluxing the surfaces, it is time to braze. First, heat the parts to be joined until they are bright red. then apply the filler wire using either a welding rod or an aluminum brazing rod. Gently tap the filler wire into place with a hammer. After the metal has cooled, inspect it to make sure that there are no gaps between the parts and that they remain securely joined together.
How to use aluminum brazing rods?
When you are brazing aluminum, first heat the metal until it becomes hot to touch. This should be done slowly and gradually for two reasons: the thermal expansion of the alloy may cause cracking if heated too quickly; secondly, overheating can create gas pockets which might weaken or even prevent a sound joint from forming. Once hot enough, apply the flux to both surfaces to be joined. The flux will clean the metal surface and help the molten brass to adhere.
Next, melt some brass rod on a gas flame or propane torch until it is fluid (not too hot, as overheating could damage the aluminum). Apply the brass carefully and evenly over the joint, using tongs. Once enough molten brass has been applied, allow the alloy to cool and solidify for a few minutes before removing any excess metal with a file or sandpaper.
When you are brazing aluminum rods, first heat the rod until it becomes hot to touch. This should be done slowly and gradually for two reasons: the thermal expansion of the alloy may cause cracking if heated too quickly; secondly, overheating can create gas pockets which might weaken or even prevent a sound joint from forming.
Next, melt some brass rod on a gas flame or propane torch until it is fluid (not too hot, as overheating could damage the aluminum). Apply the brass carefully and evenly over the joint, using tongs. Once enough molten brass has been applied, allow the alloy to cool and solidify for a few minutes before removing any excess metal with a file or sandpaper.
How strong is aluminum brazing ?
Aluminum brazing is very strong. The two parts are joined together with a layer of aluminum, which makes the joint stronger than either part alone. This means that you can use thinner material or less expensive metals for your project without worrying about whether it will be strong enough. Because aluminum has excellent toughness and strength-to weight ratio, it can be used for brazing parts that are too large, heavy or bulky to weld.
How strong is aluminum brazing ?
Aluminum joints have good ductility and are less likely to fail by cracking under stress than steel or cast iron. The strength of aluminum alloys makes them ideal materials for building bridges, cranes and other structures where high strength combined with light weight is important.
Comparison of Indicators for Choosing Aluminum Brazing Rods
The table below provides a comparison of various indicators to consider when choosing aluminum brazing rods. Aluminum brazing rods are commonly used in joining aluminum components and structures, and selecting the right type of rods is essential for achieving strong and reliable brazed joints. The indicators discussed in the table can help in evaluating and selecting the most suitable aluminum brazing rods for specific applications.
Indicator | Description | Importance | Criteria |
---|---|---|---|
Alloy Composition | The chemical composition of the brazing rod alloy. | High | Compatibility with base metal, joint strength, corrosion resistance. |
Melting Temperature | The temperature at which the brazing rod melts. | High | Compatibility with base metal, heat input, distortion control. |
Fluidity | The ability of the molten brazing rod to flow and fill gaps. | Medium | Joint quality, gap filling ability, void formation. |
Corrosion Resistance | The resistance of the brazed joint to corrosion. | Medium | Long-term durability, environmental conditions, service life. |
Tensile Strength | The maximum load the brazed joint can withstand without breaking. | High | Mechanical strength, load-bearing capability. |
Compatibility | The suitability of the brazing rod for specific base metals. | High | Adhesion, metallurgical bonding, intermetallic formation. |
The table presents several indicators that are crucial for choosing the appropriate aluminum brazing rods. These indicators help in evaluating the performance and suitability of the brazing rods for specific applications. Here is a brief explanation of each indicator:
- Alloy Composition: This indicator refers to the chemical composition of the brazing rod alloy. The alloy composition plays a significant role in determining the compatibility with the base metal, joint strength, and corrosion resistance.
- Melting Temperature: It represents the temperature at which the brazing rod melts. The melting temperature is essential for assessing the compatibility with the base metal, controlling heat input during the brazing process, and minimizing distortion of the components.
- Fluidity: Fluidity refers to the ability of the molten brazing rod to flow and fill gaps between the joined components. It affects the quality of the joint, the ability to fill gaps effectively, and the formation of voids or defects.
- Corrosion Resistance: This indicator reflects the resistance of the brazed joint to corrosion. It is crucial for evaluating the long-term durability of the joint, considering the environmental conditions in which the assembly will be used and the expected service life.
- Tensile Strength: Tensile strength indicates the maximum load the brazed joint can withstand without breaking. It is essential for assessing the mechanical strength and load-bearing capability of the joint in the intended application.
- Compatibility: Compatibility refers to the suitability of the brazing rod for specific base metals. It considers factors such as adhesion, metallurgical bonding between the brazing rod and base metal, and the formation of intermetallic compounds.
By considering these indicators and their importance in the specific brazing application, one can make an informed decision while selecting aluminum brazing rods to achieve strong and reliable joints.
FAQs
What type of brazing rod is used for aluminum?
Aluminum is a great metal to work with and also has many applications, including in the medical field. Brazing aluminum rods can come as either solid or flux core depending on your needs and the type of welding you use.
Using a brazing rod for aluminum will result in added strength that cannot be achieved when only using filler wire alone. Aluminum filler rods are made of high purity aluminum and have a higher melting point so they can be used with other types of metals.
When using a brazing rod for aluminum, you will need to use flux in order to protect the metal from oxidation. The flux core on the welding rod will help keep the metal clean and free from impurities that can cause a weak weld.
There are many different types of welding rods on the market and it can be difficult to decide which one is right for your needs. The best way to find the right rod is to read reviews from other users who have already tried them.
What is the best way to braze aluminum?
If you want to know the best way to braze aluminum, then keep reading. Aluminum is perhaps one of the easiest metals for people who are just beginning their brazing journey because it’s less expensive than most other metal options and also quite softer. If you have experience with steel or stainless steel welding, then learning how to braze aluminum should come quite naturally to you.
After reading this article, learn about the different types of rods that are available for brazing aluminum and what each type is best suited for! As always, remember to select a rod with an alloy composition that matches your needs in order to achieve maximum strength or corrosion resistance.
Is brazing aluminum as strong as welding?
The short answer is, “it depends.” Brazing aluminum produces a much weaker joint than welding, but it can still be strong enough for many applications. The main advantage of brazing over welding is that it doesn’t require the same level of skill or equipment.
Welding and brazing are both processes that involve melting metal, but they use different methods and produce different results. Welding uses heat to fuse two pieces of metal together, while brazing uses a filler material that is melted between the two pieces of metal.
The biggest difference between welding and brazing is the strength of the joint. A welded joint is much stronger than a brazed joint. This is because brazing produces a very thin layer of metal, which isn’t as strong as the base material surrounding it. While welding creates two pieces that are functionally one piece, brazing only joins the materials at their interface.
Despite this difference, there are some applications where both processes can be used successfully to join aluminum. If you’re looking for a strong, permanent joint, welding is the better choice. But if you need to join two pieces of aluminum quickly and without specialized equipment, brazing is a good option.
There are a number of different factors that can affect the strength of a brazed joint, including the type of metal being joined, the filler material being used and even how clean each piece of metal is before joining.
Can I braze aluminum with a propane torch?
Propane is not the best choice for brazing aluminum. You should use a MAPP or MAP gas torch instead of propane. This type of fuel provides better heat and results in less oxidation than does propane, which can damage your metal joint if it is exposed to oxygen too long.
What’s the best epoxy for aluminum?
Aluminum is a great metal to work with, but it can be tricky. Aluminum’s low melting point means that you need an epoxy that will bond quickly and easily without too much pressure or heat. There are many different types of aluminum alloys out there, so make sure your adhesive works for the alloy you have before buying.
Can I use acid core solder on aluminum?
Acid core solder is not recommended for welding aluminum. It can cause unsightly stains on your metal and does not make the best joints when it comes to strength or appearance. You should use a milder, more basic flux with aluminum that will produce an attractive weld bead without discoloring your workpiece.
There are many rods on the market that are designed specifically for aluminum brazing, and it is important to select the right one for your project. Some of the factors you need to consider when choosing a rod include:
- The thickness of the material you will be welding.
- The type of flux required for your specific application.
- The amount of strength you require for your finished workpiece.
- The best aluminum brazing rods will be a combination of all three.
What type of flux is used for aluminum?
It is not possible to use regular fluxes for aluminum because they will corrode and become useless. The solution is using a special type of flux called “aluminum brazing” or sometimes referred to as “spelter”. This works by removing the oxygen from the metal surface so that it does not interfere with any other elements in the alloy.
How do you bond aluminum without welding?
One way is to use aluminum brazing rods. Brazing is a process that uses a filler metal to join two pieces of metal together. The filler metal is melted and then drawn into the joint between the two metals. aluminum brazing rods are made specifically for bonding aluminum.
There are several factors you need to consider when choosing the right brazing rod. The first is the type of aluminum you are bonding. There are three types of aluminum: 1100, 3000, and 5000. Each type has a different melting point. The second factor to consider is the thickness of the metal you are bonding. thicker metals require a higher temperature to melt the filler metal. The third factor is the type of filler metal. There are three types of filler metals: silver, copper, and brass. Each one has a different melting point and corrosion resistance.
What is the strongest adhesive for aluminum?
The strongest adhesive for aluminum is a metal-to-metal bond. This can be achieved through welding, brazing, or soldering. Each of these methods uses a different type of heat to join the two metals together. Welding uses a high temperature to melt the metals and fuse them together. Brazing and soldering use a lower temperature to heat the metal until it becomes a liquid. This liquid is then drawn into the joint between the two metals, creating a bond.
All three of these methods have their advantages and disadvantages. Welding creates the strongest bond, but it can be difficult to learn and requires specialized equipment. Brazing and soldering are both easier to learn and can be done at home, but these methods leave a visible joint in the metal. Your choice between brazing and soldering will depend on what you are making from your aluminum alloy. If it needs to look seamless when complete, then welding is the right choice for you.
If appearance does not matter, either method of joining metals together will work. The final decision comes down to the type of metal you are using and what you need it to do.
Why are fluxes necessary in brazing?
Fluxes are necessary in brazing because they clean the metal surfaces to be joined and protect them from oxidation. The flux also helps the filler metal flow into the joint, providing a strong bond. There are many different types of fluxes available, so it is important to select the one that is best suited for the specific application.
What kind of solder works on aluminum?
Aluminum brazing rods, also known as hard solder, work on aluminum. The most common types of solder used for welding and repairing aluminum are silver braze alloy (90% tin, .05% magnesium) or nickel-based alloys such as Monel and Inconel, which have similar compositions to the copper/nickel alloys used for brazing stainless steel.
There are two types of aluminum soldiers: high-temperature and non-high temperature. High-temperature solder melts at a higher or more fluid range than standard 60/40 rosin core electrical solder, which is typically the type recommended by manufacturers to use on aluminum components.
What temperature should you braze at?
The temperature for brazing aluminum depends on the alloy you are using. If you do not know what alloy your rods contain, use a rod that contains magnesium in it at all times when brazing aluminum.
What is a brazing filler rod made of?
Brazing filler rods are made of a variety of materials, but the most common are copper and brass. They are available in different diameters and lengths to fit your needs.
What types of brazing filler rods are available?
There are two main types of aluminum filler rod: hard and soft. Hard rods usually have a silver or gray coating that provides added protection against oxidation during the heating process, as well as increased strength for applications such as joining dissimilar metals. Soft aluminum rods do not contain any protective coating and are best used for applications that require a higher degree of corrosion resistance.
How do I choose the right brazing filler rod?
When choosing a filler rod, you need to consider the type of metal you will be brazing, as well as the thickness and composition of the materials. You also need to take into account the temperature at which the brazing will take place. For example, if you are joining two pieces of aluminum together, you would use a soft aluminum filler rod. If you are joining a piece of aluminum to a steel component, you would need to use a hard aluminum filler rod in order to prevent oxidation.
What is aluminum brazing?
Aluminum brazing is a joining process that involves the use of a filler metal rod to bond aluminum parts together. It is a method commonly used to create strong and durable connections between aluminum components.
What are the benefits of using aluminum brazing rods?
Aluminum brazing rods offer several advantages. They provide excellent bonding strength, high corrosion resistance, and good electrical conductivity. Additionally, aluminum brazing rods have a lower melting point compared to aluminum itself, making them suitable for joining aluminum parts without compromising their structural integrity.
How does aluminum brazing differ from welding?
Aluminum brazing and welding are distinct processes. While welding involves melting the base metal and filler material to form a fusion weld, brazing creates a joint by melting only the filler metal. Brazing does not melt the base metal, minimizing the risk of warping or distortion. It also allows the joining of dissimilar metals, which is not easily achievable through welding.
What are the common applications of aluminum brazing rods?
Aluminum brazing rods find applications in various industries, including automotive, aerospace, HVAC (heating, ventilation, and air conditioning), and electronics. They are commonly used to join aluminum heat exchangers, radiators, condensers, air coolers, and electrical components.
How do I prepare the aluminum surfaces for brazing?
Before brazing, it is essential to properly prepare the aluminum surfaces. This typically involves removing any dirt, oil, or oxide layers from the surfaces to ensure good adhesion. The surfaces can be cleaned using a degreaser or a suitable solvent, followed by mechanical abrasion or chemical etching to remove oxides.
What equipment is required for aluminum brazing?
Aluminum brazing can be performed using various equipment depending on the scale and complexity of the project. Commonly used tools and equipment include a propane or oxy-acetylene torch, a flux applicator, a heat source, and protective gear such as gloves and goggles.
What types of flux are used in aluminum brazing?
Fluxes play a crucial role in aluminum brazing as they help remove oxides from the metal surfaces, promote wetting, and enhance the flow of the filler metal. Fluxes specifically formulated for aluminum brazing, such as chloride-based or fluoride-based fluxes, are commonly used to achieve clean and strong joints.
How do I select the appropriate aluminum brazing rod?
Choosing the right aluminum brazing rod depends on several factors, including the specific aluminum alloy being joined, the application requirements, and the desired strength of the joint. It is crucial to consider the composition, melting range, and compatibility of the brazing rod with the base metal to ensure a successful brazing process and a strong bond. Consulting technical specifications or seeking expert advice can assist in selecting the appropriate brazing rod.
What precautions should I take during aluminum brazing?
When performing aluminum brazing, it is important to take certain precautions for safety and optimal results. Ensure proper ventilation in the work area, use protective equipment to prevent exposure to fumes and heat, and follow the manufacturer’s instructions for handling and storage of brazing rods and fluxes. Additionally, practice proper brazing techniques and maintain a clean workspace to avoid contamination and achieve high-quality joints.
Can aluminum brazing be done by beginners?
Aluminum brazing can be challenging for beginners due to its specific requirements and techniques. It is recommended to acquire basic knowledge of brazing principles, proper surface preparation, and filler metal selection before attempting aluminum brazing. Seeking guidance from experienced individuals or undergoing training programs can greatly help beginners in mastering the aluminum brazing process.
Useful Video: Brazing Rods Challenge
Conclusion
So, there you have it – our top aluminum brazing rods. We hope that this buyer’s guide has helped you in your search for the perfect rod for your needs. Remember to consider all of the factors discussed above before making your purchase, and happy brazing!