
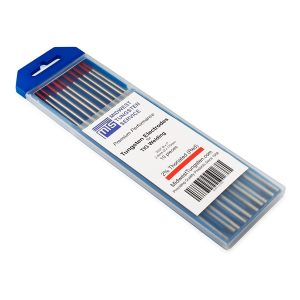
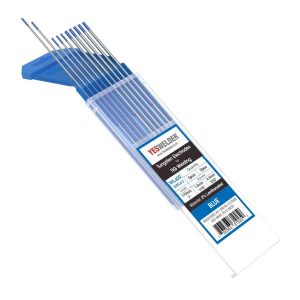
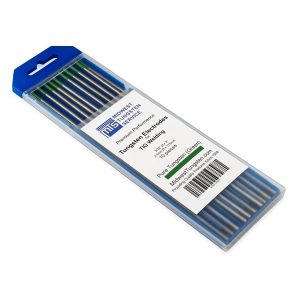
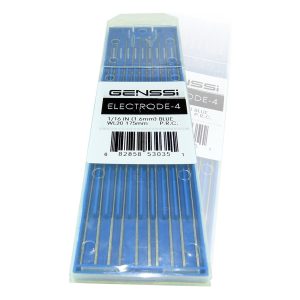
Choose the Best Tungsten Electrode for Aluminum
Customer’s Choice: the Best Rated Tungsten Electrodes for Aluminum
105 users answered this survey. Please help us improve this review!
Tungsten as a term comes from the Swedish word “tung sten”. It means “heavy stone”. The element can be found in the minerals scheelite, huebnerite, wolframite, and ferberite. It is extracted from minerals by decreasing tungsten oxide with carbon or hydrogen.
Once obtained, tungsten is often blended into alloys. Diamonds are used to form the toughest alloys. Only diamonds are softer than other tungsten alloys.
Why should you choose tungsten?
Tungsten is regarded as one of nature’s hardest elements. It is very thick and almost difficult to melt. Tungsten is a silver-white metal that. Being ground into a fine powder, this metal is combustible. Also, it may spontaneously ignite. There are 5 stable isotopes and 21 unstable isotopes of natural tungsten.
Tungsten is applied in a variety of applications due to its high strength and durability. It is extremely corrosion resistant and has the highest melting point and tensile strength of any element. However, it gains power when combined with other elements to form compounds. Tungsten is a very delicate metal.
Its heat resistance is advantageous when used as a heating element in spacecraft applications, electrical furnaces, welding, and other high-temperature uses. For this purpose, it was often used in the manufacture of various forms of lighting.
Tungsten does not have the luster of gold. It has the density (within 0.36 percent) that ensures that if you sprinkle a tungsten brick with gold.
Properties of aluminum welding with tungsten electrodes
Tungsten Inert Gas (the short is TIG) in the specific aluminum welding is the process of delivering current to the welding arc using a non-consumable tungsten electrode.
The fact that you would use both hands when welding is what most people find difficult with this method of welding. However, the endeavor is worthwhile because the end product is outstanding, excellent, and visually appealing welds.
TIG welding relies on precision and professionalism. You will improve the efficiency of your welding by using the best TIG welding tungsten electrode form.
Below, the experts recommend the best tungsten electrodes recommended for aluminum welding. Read the comparison table, buying guide and product reviews.
Midwest Tungsten 2% Lanthanated Electrodes 10-Pack – the best for wide application!
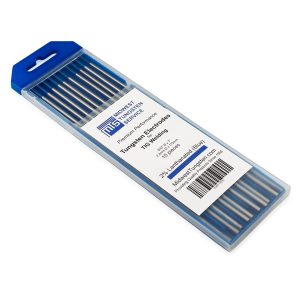
Midwest 2 percent Lantanated Blue electrodes are ideal for welding titanium, magnesium, aluminum, nickel, copper, low-alloyed steel, and stainless steel in both AC and DC applications.
There is a size difference. If you choose to use thin aluminum, you would use the 18-inch size. If you need a thinner one, there are 0.040”, 1/16”, and 3/32” sizes usable.
Pros
- Certified by the American Welding Society;
- The high-frequency arc start;
- Cost-effective;
- Great performance for AC and DC applications;
- Durable;
- Low rate of burning off;
- Versatile;
Cons
- Different consistency in a batch;
- May erode while welding aluminum;
- Rods may splinter when you break off the bits;
- May break when sharpening;
These electrodes are common with those who weld regularly or as a hobby due to their flexibility and durability. In reality, they can be used to weld not only aluminum but also mild steel and specific metal alloys.
Midwest Tungsten Electrodes 2% Thoriated – the best for the price!
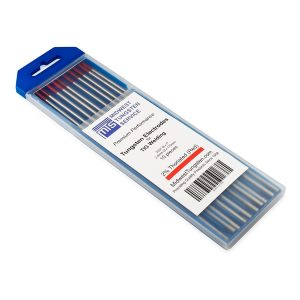
It is safe to use for welding copper, nickel and titanium alloys, and stainless steel. Midwest 2 percent thoriated electrodes are well-known for the low burn-off rate, consistent arc-striking, and longevity while meeting ANSI and AWS requirements.
Pros
- Stability for melted metals;
- Budget-friendly;
- Good customer service;
- Free materials safety data sheets;
Cons
- May split easily;
- Damaged packages are possible;
The Midwest tungsten electrode assists in arc stabilization and directs heat to the puddle. This makes for consistent welding without inclusions when making custom parts. These are simple to mill and do not ball.
Yeswelder Tungsten Electrode 2% Lanthanated – the best for quick sparking!
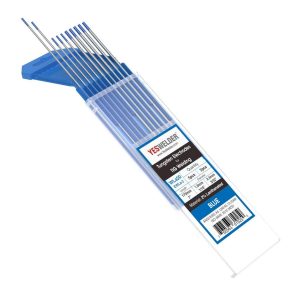
There are 5 sets of 1/16 inch electrodes and 5 pieces of 3/32 inch electrodes.
These electrodes spark up easily, provide strong arc durability, and maintain a pointed tip for a long period. They conveniently split apart and grind. That is what you ever require from an electrode. This is a high-quality electrode at a low cost.
Pros
- Great vacuum-sealed package;
- Breaks off quickly;
- Great arc stability;
- Can be preserved for a long time;
- No oxidation;
Cons
- The quality is average;
The electrodes are common due to the ease with which an arc can be struck and the lower amperage needed. They work admirably in both AC and DC applications.
Midwest Electrodes Pure Tungsten – the best for AC welding!
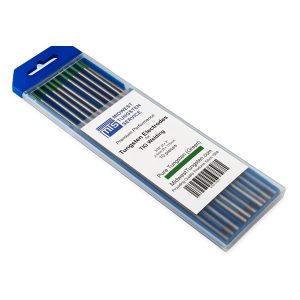
It is mostly used for AC welding. Since there aren’t enough arcs in DC. They are 7 inches long. The price is relatively lower than that of other alloys, but it is almost the same. It is not toxic, compared to thoriated tungsten. As a result, it is not as dangerous.
Pros
- Made in the United States;
- Budget-friendly;
- Less radioactive than other types;
- The burn-off is low;
- Awesome arc stability in AC welding;
Cons
- Limited compatibility with metals;
- Doesn’t fit for all types of DC current;
- Not enough arcs in DC;
These MTW tungsten electrodes are well-known for their excellent conductivity, longevity, and efficiency. They work well in alternating current applications and are ideal for welding magnesium and aluminum alloy.
GENSSI Tungsten Electrode Blue WL20 – the best for long service!
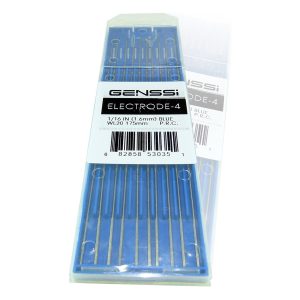
Since these electrodes are extremely durable, they can have a steady arc all the way around, resulting in smooth, spatter-free welds. The Genssi electrodes are 2% lanthanated and are ideal for welding aluminum. Also, you may use it for welding stainless steel, carbon steel, and mild steel.
Above everything, this machine is cost-effective – you won’t have to split the bank.
Pros
- Affordable;
- Long service;
- Good arc production;
- Suitable for DC and AC;
- Premium product;
- Full duty cycle at lowered amperage;
Cons
- Only one size;
- Not very versatile;
If you’re hunting for the right tungsten for aluminum welding electrodes that can accommodate both AC and DC uses, the Genssi electrodes are the way to go.
The Buyer’s Guide
Uses
Welding, or arc welding, is one of the most popular applications for tungsten. When welding, consumers can use the tungsten that is ideally suited to their technique, as well as a material such as tungsten for aluminum or stainless steel. They can also be familiar with the application of tungsten on top of aluminum.
Aside from welding, this kind of electrode is commonly used in the lighting industry. They can also be seen on the TV tube. The capacity to tolerate very high temperatures is one of these electrodes’ distinguishing features. As a result, they are often seen in X-ray either.
Color-coding
Tungsten electrodes can be distinguished from one another by their distinct color, among other factors:
1) Blue
The 2 percent Lanthanated blue color denotes a general purpose electrode for AC and DC current power sources dependent on inverters or transformers. Low-alloyed steels, non-corroding steels, aluminum, magnesium, titanium, nickel and copper alloys are all suitable for these electrodes. Arc stability is excellent. They offer the medium to high amperage range along with decreased erosion rate.
2) Green
This color represents pure tungsten. Furthermore, these electrodes have the largest concentration of tungsten. They contain 99.5 percent tungsten, to be precise. That is why they are among the most popular electrodes for TIG welding. However, it is not recommended for DC welding. Pure tungsten electrodes perform extremely well for arc welding.
3) Orange
They are commonly referred to as ceriated tungsten electrodes because they have a considerably lower percentage of tungsten, 97.3 percent. Aside from this element, they contain 2.2 percent cerium. These electrodes are more useful for DC welding, as opposed to green electrodes.
4) Red
The color red is synonymous with thoriated electrodes. It is fair to assume that these are the most often employed electrodes. One explanation for this is the various beneficial characteristics they exhibit. To start, users may weld both DC and AC with them. Because of the low rate of burial, they would be less polluted when doing so. Having said that, they are user-friendly, easy to use, and long-lasting. These electrodes are constructed of 1.7 percent thorium (which gives them their name) and 97.3 percent tungsten.
5) Gold
TIG welding aluminum with gold lanthanated electrodes is possible in both AC and DC environments. Depending on the mission, they may be balled or sharpened. 1.5 percent Lanthanated tungsten electrodes have consistent arc starts while still maintaining a smooth and steady arc throughout. Since they have no radioactive materials, many welding professionals choose them as a substitute for thoriated electrodes due to their longevity and flexibility.
6) Brown
A natural mix of brown zirconiated electrodes of 99.10 percent tungsten and 0.15 to 0.40 percent zirconium. The key characteristics that everybody searches for are a stable arc and defense from tungsten spitting. It has a balled tip that can be used for AC welding. Contamination won’t probably occur in the presence of strong resistance activity. If there is no time constraint, you should even try it for DC welding.
7) Gray
Rare Earth gray tungsten electrodes produce several oxide combinations in one location. The percentage of every oxide is mentioned in the package. As a consequence, depending on the ratio of the additive, you’ll get varying effects. Check for the additive forms and percentages to see how they will operate a reliable arc in both AC and DC welding. Rare Earth electrodes have a higher life cycle than thoriated tungsten electrodes. Otherwise, they’re useful for reducing tungsten spitting.
8) Purple
The Rare Earth Mix purple electrodes are a suitable replacement for the 2% thoriated (red) electrodes. This can work during the most demanding welding application because they are quick and accurate arc-striking, durable, and highly robust. Aluminum, magnesium, titanium, nickel and copper alloys, non-corrosive steels and low-alloyed steels are all excellent candidates.
9) White
The 0.8 percent white zirconiated electrodes are well-known for their exceptionally robust arc, strong resistance to contamination and tungsten splitting. Ideally suited for arc welding. For magnesium and aluminum alloys, they may accommodate higher amp speeds.
The color coding is determined by the chemical structure of these electrodes, and every has its own set of applications, laws, and benefits. The electrodes mentioned above can be applied for TIG welding aluminum.
AC and DC compatibility:
- 2% thoriated red electrodes for DC only;
- 2% ceriated orange tungsten electrodes for AC only;
- 2% lanthanated blue tungsten electrodes for both DC and AC;
- 1.5% lanthanated gold – both for DC and AC;
- Pure green tungsten for DC only;
Never apply pure tungsten electrodes on alternating current because pure tungsten will ball up, particularly if an inverter is used. Every welder has a favorite kind of tungsten; some choose thoriated tungsten, whereas others choose pure tungsten. Whichever choice you choose, it will all function flawlessly as long as you have the proper settings and program.
Size
When buying tungsten electrodes, most welders make a mistake with this element. The form and size of the electrodes present on the market vary. Whether this is to account for the consternation felt by many welders.
Nonetheless, the general recommendation is to consider using very tiny electrodes. This is because they always result in a sloppy welding technique.
When using somewhat elevated temperatures, the minimum suggested size is about 1/8 inch. If you’re into AC welding, the size will go up to 3/32 inches, making it one of the biggest categories of electrodes in terms of tungsten content for aluminum.
Lanthanated vs thoriated tungsten electrodes for aluminum
You don’t have to worry twice about it; lanthanated electrode is much superior for a plethora of reasons. But don’t get us wrong: we’re not saying the thoriated tungsten electrode is totally useless; it has benefits over the lanthanated electrode as well.
Lanthanated electrodes can accommodate more amperage than any other electrode available on the market. As a result, they are the most used tungsten electrode for heavy-duty uses.
Lanthanated electrodes often display no differences in terms of welding machine type; they are consistent with TIG welding machines. Lanthanated electrodes need the least voltage to be broken down, making arc formation very simple.
Finally, lanthanated electrodes are not toxic, unlike thoriated tungsten and other alloys.
Most metal collectors would inform you that the Blue 2 percent Lanthanated Tungsten Electrode is the best tungsten.
It’s also worth noting that ceriated electrodes aren’t ideal for TIG welding at high amps. Because heat will induce differences in the electrode structure. At lower temperatures, this method of welding electrode is widely used for pipe fabrication, welding thin metals, and small, specific sections.
FAQ
What is the best tungsten type for aluminum welding?
Aluminum is used in three thicknesses: medium, dense, and mid-thick. Aluminum may be weld fluently by a skilled hand using the proper welder unit. To work with aluminum compounds, you’ll require pure tungsten electrodes. So, for aluminum and magnesium, use green electrodes. Green electrodes are ineffective for DC welding. They are unable to generate deep arcs like ceriated or thoriated electrodes.
Can tungsten trigger allergy?
It is determined by the state of your skin’s wellbeing. There is no issue and no reason to be concerned if you have good skin. However, if the skin is too sensitive, it can cause irritation.
Can you apply the purple tungsten electrodes for aluminum welding?
Yes, you can. Even if this color isn’t one of the top three most common, that doesn’t imply it’s ineffective. On the opposite, these electrodes are picked for a wide range of metals, from aluminum and steel. You may also use it for welding carbon, titanium, copper, and everything in between.
What color tungsten is best for aluminum?
The best color for tungsten when welding aluminum is green. Green tungsten offers the best performance and stability, as it allows for higher amperage when welding aluminum and has a lower risk of arc wander. Additionally, green offers better visibility during welding; its bright color makes it easier to see the puddle when welding in confined spaces. If you’re looking to get the best results when welding aluminum, green tungsten is definitely your best bet.
What type of electrode is best for aluminum?
Use a pure tungsten or zirconiated tungsten electrode when AC welding aluminum. These electrodes don’t contain any thorium or cerium, which are found in some other tungsten varieties. For DC welding aluminum, you can use either a pure tungsten or thoriated tungsten electrode. Thoriated electrodes provide better arc starting and stability than pure ones. However, they do contain small amounts of radioactive material that must be handled with caution. It is important to note that you should never attempt to AC weld with a thoriated electrode. Doing so can cause excessive spatter and poor arc performance due to the high levels of current required for this type of welding. Always look at the packaging information when purchasing electrodes and follow safety precautions when working with them.
What size tungsten is best for welding aluminum?
For welding aluminum, it’s best to use a tungsten that is in the range of 1.6mm to 3.2mm (1/16” – 1/8”). Thinner tungstens may be used for aluminum welding but will not provide as much arc stability, whereas on thicker aluminum alloys, you may need a larger tungsten with increased current and amperage settings. Ultimately, it depends on the specific type of aluminum alloy being welded and what kind of results are desired. Generally speaking, it is always best to begin with a smaller size electrode and increase the size until the desired results are achieved.
Is blue tungsten good for welding aluminum?
Blue tungsten is not the best choice for welding aluminum. It can be used in a pinch, but there are better options available. Tungsten electrodes with a higher melting point such as red or green are much better suited for the job. They will create an arc that’s more stable and reliable when welding aluminum, resulting in a stronger weld overall. If you’re serious about welding aluminum, it’s best to invest in these higher-quality tungsten electrodes. You won’t be disappointed! Good luck with your project!
Is purple tungsten good for aluminum?
Yes, purple tungsten is an excellent choice for aluminum. It’s a good conductor of heat and electricity, and its hardness allows it to cut through the metal with ease. It also leaves a smooth finish that gives your project a professional look. Purple tungsten is great for intricate details like engraving and drilling small holes. Plus, it’s relatively easy to find in most hardware stores or online! So if you need a reliable cutting tool for your aluminum projects, purple tungsten should be your go-to choice.
Why does my tungsten ball up on aluminum?
This is a common problem when machining aluminum with tungsten. The extreme heat that is generated between the two metals causes them to adhere together, resulting in what is called “tungsten balling.” To reduce this effect, you need to use a different tool material like carbide or high-speed steel. You can also try increasing the speed of your cutting process, as well as using coolants like water or oil to help keep the temperature down. Lastly, make sure that the aluminum surface you are working on is clean and free from debris, as any build up can cause the two metals to stick more easily. With these tips, you should be able to lessen or eliminate tungsten balling on aluminum.
Which tungsten can only be used on aluminum?
Tungsten alloy can be used on aluminum, but pure tungsten should not be used. The reason for this is that aluminum melts at a lower temperature than tungsten, which means the molten aluminum will dissolve the tungsten and cause it to corrode. This corrosion will weaken the joint between the two metals and make it much less effective. Therefore, an alloyed or blended tungsten should be used when welding aluminum to ensure proper performance and long-term durability. Alloys of tungsten are also softer and more malleable than pure tungsten, making them easier to work with and shape into various forms for specific applications.
Why is my tungsten melting when welding aluminum?
When welding aluminum, it’s important to use a tungsten that has been specifically designed for the job. If the wrong tungsten is used, it can cause melting due to improper heat transfer. Additionally, if the tungsten is contaminated with other metals or chemicals, this can also contribute to melting during welding. It’s important to ensure that only clean and specialized tungstens are being used in order to avoid any unnecessary melting. Also make sure that you’re using the correct current setting for your welding project – if it’s too high it can easily cause excess heat which will lead to melting of your tungsten! Finally, always wear appropriate safety equipment when welding and be aware of any potential sparks or debris flying around. Doing all of these things will help ensure your tungsten doesn’t melt during welding.
Do I need to ball tungsten for aluminum?
No, you don’t need to ball tungsten for aluminum. Tungsten is a much harder metal than aluminum and it’s not necessary to use it in order to weld aluminum successfully. Instead, you can use a mild steel or stainless steel electrode for welding aluminum, which will be more effective and cost-efficient. Additionally, tungsten is not recommended for welding aluminum because it can cause the weld to be brittle and prone to cracking. Therefore, if you’re planning on welding aluminum, it’s best to stay away from tungsten electrodes.
How far should the tungsten stick out when welding aluminum?
When welding aluminum, the stick-out should be kept to a minimum. Generally speaking, it’s best to keep the stick-out between 1/8″ and 1/4″. If the stick-out is too short or too long, it can cause problems with welding. Too short of a stick-out can cause inconsistent arc starts and can make it difficult to maintain a stable arc. Too long of a stick-out may cause excessive spatter and poor penetration. It’s important to use the right size contact tip for your application in order to ensure proper welding performance. Additionally, keeping the tungsten sharpened is also essential for quality welds on aluminum. Using clean (non-oxidized) tungsten helps reduce contamination and sticking. With proper technique, you can achieve beautiful welds that are strong and durable!
Should you preheat aluminum before welding?
The answer to this question depends on the type of aluminum you are welding. If you are working with thin-gauge aluminum, such as that used in auto body repair or sheet metal fabrication, then preheating is not necessary and may even weaken the joint. However, if you are welding thicker pieces of aluminum or those with a higher alloy content, then preheating can help to ensure a strong bond between the pieces.
When preheating aluminum for welding, it is important to use an even heat and not exceed 400-500°F (204-260°C). This helps to keep the metal soft and malleable, which will make it easier to work with. It also helps to reduce the risk of cracking or warping during the welding process. Additionally, preheating will allow you to weld more quickly and accurately since it can reduce the amount of heat needed to melt the metal.
It is important to remember that aluminum needs a different kind of welding than other metals and requires the right tools and techniques to ensure a strong bond. With the right preparation and preheating, you can achieve professional results when welding aluminum.
What frequency is best for welding aluminum?
When it comes to welding aluminum, the best frequency is usually from 120 to 200 Hz. This range provides enough power for successful welding while avoiding any risk of overheating the metal or causing excessive sparking. Higher frequencies can be used but should be done with caution and expertise as they may cause too much heat buildup during welding.
Useful Video: How to choose the correct Tungsten for TIG Welding
Final thoughts
TIG welding aluminum with tungsten has shown to be positive. It is appropriate for both domestic and industrial use. Although each tungsten electrode has advantages and disadvantages, the 2% lanthanated tungsten electrode is one of the better tungsten for aluminum welding. Although most welders choose this electrode because it is durable and offers a great stable arc for a nice and clean weld, some choose it for other purposes.