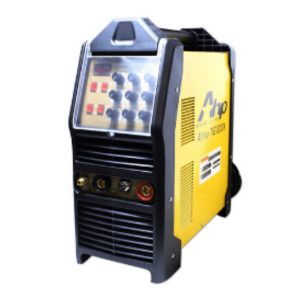
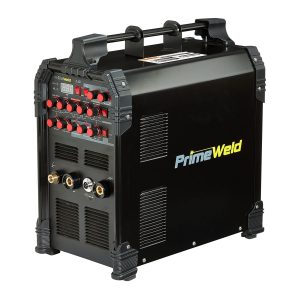
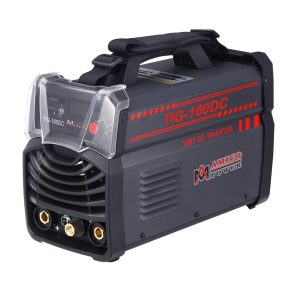
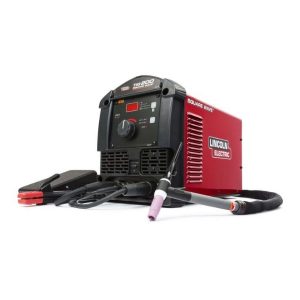
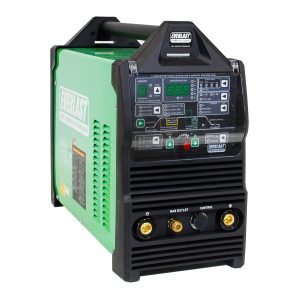
Choose the Best TIG Welder for Aluminum
Customer’s Choice: the Best Rated TIG Welders for Aluminum
26 users answered this survey. Please help us improve this review!
So you’re in the market for a TIG Welder for aluminum? Great choice! TIG welding is an extremely versatile process that can be used on a wide variety of materials, including aluminum. The TIG Welders are effective because they use an arc between a non-consumable tungsten electrode and the material being welded. This process can be used to weld aluminum, stainless steel, mild steel, magnesium, copper alloys, nickel alloys – really any conductive metal. This article will discuss some of the things you need to consider when choosing a TIG Welder for aluminum, and it will recommend some of the best models on the market. This guide will also provide some tips for using your TIG Welder safely and effectively.
AHP AlphaTIG 200X 200 Amp IGBT AC/DC, Tig/Stick Welder
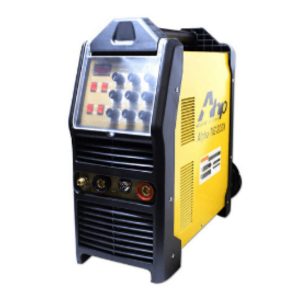
For added convenience, the AHP AlphaTIG 200X comes with a foot pedal for TIG welding operation and process control. So, if you’re looking for a top-quality welder that can handle any project you throw at it, the AHP AlphaTIG 200X is the perfect choice!
PRIMEWELD TIG225X AC DC Tig/Stick Welder with Pulse, 225 Amp
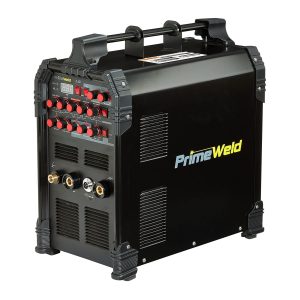
The cleaning control for AC is another great feature, as it ensures that your welds are clean and professional-looking. Overall, this welder is an excellent choice for those looking for a high-quality and versatile welding machine.
Amico TIG-160DC, ARC Stick DC Welder 110/230V, 160 Amp
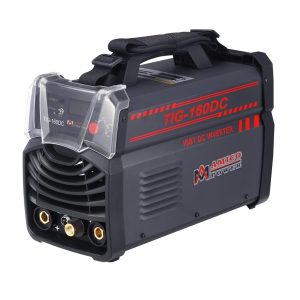
And to top it all off, the machine comes with a 3-m 300-A Electrode holder & cable, ensuring overheating and over/under voltage protection. So, if you’re looking for a top-of-the-line welding machine that can handle any job, the Amico TIG-160DC is the perfect choice.
Lincoln K5126-1 Electric Square Wave TIG 200 Welder
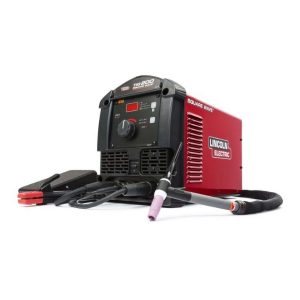
The user-friendly interface and portable design make it easy to take this welder anywhere, while the adjustable AC balance ensures clean action every time. Get the job done right with the Lincoln K5126-1 Electric Square Wave TIG 200 Welder.
Everlast Power Digital AC / DC TIG Stick Pulse Inverter Welder, 110v/220v
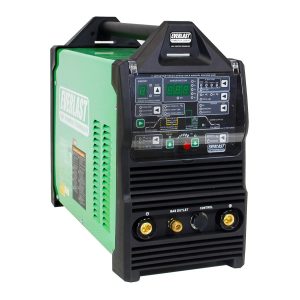
The billet brass regulator and 1,82-m power input cable make this welder even more durable and long lasting. For added convenience, the welder comes with hot-start intensity settings and a compact foot pedal. Pulse up to 500 Hz in DC mode for different welding applications.
Buyer’s Guide
When Do You Need a TIG Welder for Aluminum?
A TIG Welder For Aluminum is a modern device that is used in the industry for joining two pieces of aluminum. TIG Welders can also be used to weld other metals such as stainless steel and magnesium. TIG Welders are usually used in the aerospace industry and automotive industry. If you are working with aluminum or any other metals, then you need a TIG Welder that can weld those materials.
The TIG Welder For Aluminum can be effective for such projects as repairing an aluminum boat hull or creating a custom motorcycle frame. Moreover, the TIG Welder is precise and provides neat results. Additionally, the TIG Welder is a versatile device, and you can use it for various professional projects like auto body repairs and metal fabrication.
Consider the following before you explore and decide on your TIG welder
What do you aim to do?
The first question you should ask yourself is what you aim to achieve with your welder. Are you a professional who needs it for work? Do you need it for a one-time project? Or do you just want to have one around the house in case you need to make repairs? Your level of expertise will also play a role in deciding which welder is best for you. If you’re a beginner, it might be best to choose a model that is easy to use and doesn’t require too much setup. On the other hand, if you’re more experienced, you might want something that has more features and is more versatile.
What metals do you want to weld?
The next question to consider is what metals you want to weld. Different welders are better suited for different materials.
However, if you think you might need to weld different metals in the future, then it might be worth investing in a more versatile welder.
TIG welding aluminum is generally considered to be more difficult than welding other materials. This is because aluminum has a lower melting point and is more prone to oxidation. As a result, it’s important to choose a welder that has enough power to heat the metal properly. You’ll also need a model with adjustable settings so that you can control the heat output.
Where do you want to use your Aluminum TIG machine?
Another important consideration is where you’ll be using your welder. If you only need to use it occasionally, then a portable model might be a good choice. However, if you plan on using it regularly, then a more powerful and durable model might be a better investment.
You can use TIG Welders For Aluminum in a variety of settings, including:
- Automotive shops
- Construction sites
- Fabrication shops
- Garages
- Home workshops
No matter where you plan on using your welder, it’s important to make sure that you have a safe and sturdy work surface. This will help to prevent accidents and injuries.
What is your budget?
As with any purchase, it’s important to consider your budget when choosing a welder. There are many different models on the market, and the price can range from a few hundred dollars to several thousand. It’s important to find a balance between quality and cost. If you’re just starting out, then it might be best to choose a less expensive model. This way, you can get a feel for how to use the welder without spending too much money. Once you become more experienced, you can upgrade to a more expensive model that has more features and is better suited for your needs. Keep in mind that cheaper welders might not have all the features that you want or need. They also might not be as durable or reliable.
Duty cycle
The duty cycle is the amount of time that a welder can be used before it needs to cool down. This is an important consideration, especially if you plan on using your welder for extended periods. If you only need to use your welder occasionally, then a lower duty cycle might be fine. However, if you plan on using it frequently or for long periods, then you’ll need to choose a model with a higher duty cycle.
Duty cycles are usually expressed as a percentage.
In general, TIG welders have a lower duty cycle than MIG welders. This is because TIG welding uses more heat, which can overheat the welder.
The next question is multi-process welder or only TIG welder?
Multi-process welders are becoming increasingly popular because they offer the flexibility to weld different materials. If you think you might need to weld other materials in the future, then a multi-process welder might be a good choice. However, if you only plan on welding aluminum, then a TIG welder would be sufficient. TIG welding is considered to be the best method for welding aluminum.
This is because it produces a high-quality weld that is less likely to crack or break. It’s also more precise than other methods, which makes it ideal for delicate projects. However, TIG welding is more difficult than other methods and requires more skill and experience.
Weight and portability
Another important consideration is the weight and portability of the welder. If you plan on using your welder in different locations, then a portable model might be a good choice. However, if you only need to use it in one place, then a heavier model might be fine. Keep in mind that portable welders might not be as powerful as stationary models. Portable welders are available in both gas and electric models. Gas-powered welders are usually more powerful but also heavier and more expensive. Electric welders are lighter and less expensive but might not have as much power.
The stationary models can weigh upwards of 90 kg, so keep that in mind when deciding where you’ll be using your welder. The portable welding devices can weigh as little as 7 kg but their power output is significantly lower.
Warranty
Another important consideration is the warranty. Most welders come with a one-year warranty, but some companies offer extended warranties for an additional cost. It’s important to read the fine print of any warranty before you purchase a welder. This way, you’ll know what’s covered and what isn’t.
Some warranties only cover defects in materials or workmanship, while others might cover more. It’s also important to register your welder with the manufacturer. This way, you’ll be able to take advantage of any recalls or repairs that might be necessary. Welding can be a dangerous activity, so it’s important to choose a welder that is durable and reliable. A good warranty can give you peace of mind in knowing that your welder will be covered in case of any problems [1].
TIG Welder Features to look for
Scratch Start vs. Lift Start
The next thing you’ll want to consider is how the torch starts the arc. Scratch start TIG welders are going to have a higher amperage output than lift start models. That means they can weld thicker materials, but it also makes them more difficult to use on thinner materials. If you’re welding aluminum that’s less than 18 gauge, you’re going to want a lift start model.
Lift start TIG welders use lower amperages and have a softer arc, making them easier to control on thinner materials. They’re also easier to use if you’re new to TIG welding. However, they aren’t able to weld as thick of material as scratch start models. If you’re planning on welding anything thicker than 18 gauge aluminum, you’ll want to go with a scratch start model.
High-Frequency Start
Another feature to look for in a TIG welder is a high-frequency start. This feature helps to reduce the amount of time it takes to start an arc. It also makes it easier to strike an arc on thinner materials. If you’re welding aluminum that’s less than 18 gauge, you’ll want a welder with high-frequency start. A high-frequency start is a great feature to have if you’re welding thin materials. However, it’s not necessary if you’re only going to be welding thicker materials. If you plan on welding both thick and thin materials, then you’ll want a welder that has both high-frequency starts and lift start capabilities.
What is the 2T/4T Torch Control Feature on a Welder?
The next thing you’ll want to consider is the torch control feature.
Two-trigger torches have a separate button for starting the arc and another for welding. Four-trigger torches have a single button that does both functions. Two-trigger torches are more difficult to use than four-trigger torches, but they give you more control over the welding process. If you’re new to TIG welding, you’ll probably want to start with a four-trigger torch. As you get more experience, you can switch to a two-trigger torch if you feel like you need more control over the welding process.
Pulse TIG Feature
The last thing you’ll want to consider is the pulse TIG feature. This feature allows you to control the welding current in pulses, which can help reduce heat build-up and improve weld quality. Pulse TIG is a great feature to have if you’re welding aluminum. However, it’s not necessary if you’re only going to be welding steel or stainless steel. If you plan on welding both aluminum and steel, then you’ll want a welder that has both pulse TIG and lift start capabilities [2].
How to use TIG Welder on aluminum?
There are a few things you need to keep in mind when using TIG welders on aluminum. Make sure the welder is set to AC, as this will help reduce oxidation. You’ll also want to use a non-essential gas like Argon, as it will create a cleaner weld. And finally, be sure to use an aluminum-specific welding rod – using steel or iron rods will contaminate the weld and make it weaker. To weld aluminum with a TIG device you should follow these steps:
- Set your welder to AC
- Use a non-reactive gas like Argon
- Use an aluminum welding rod
- Use a lower amperage
- Go slowly with long passes
- Keep the welding torch at a shallow angle
- Use filler rod sparingly
By following these simple steps you’ll be able to weld aluminum with ease and produce strong, high-quality welds [3].
How to take care of TIG Welder for Aluminum?
You should always keep your TIG welder for aluminum in a clean and dry place. If you are not using it, make sure to cover it with a cloth or tarp to protect it from the elements. When you are ready to use it again, wipe down the machine with a damp cloth to remove any dust or debris that may have accumulated on it. It is also important to regularly check the condition of your TIG welder’s power cord and consumables. Make sure to replace them if they show signs of wear or damage. following these simple tips will help ensure that your TIG welder for aluminum lasts for many years.
You should also know how to use your TIG welder for aluminum properly. Make sure to read the manual that came with your machine. Familiarize yourself with the different controls and settings. Practice on some scrap pieces of aluminum before you start working on your project. This will help you get a feel for how the machine works and how to control it.
Always wear the proper safety gear, including a welding mask, gloves, and long sleeves. Weld in a well-ventilated area to avoid inhaling fumes. By following these tips, you can be sure that your TIG welder for aluminum will last for many years and provide you with excellent results [4].
Comparison of Indicators for Choosing TIG Welders for Aluminum
Choosing the right TIG welder for aluminum welding is crucial to ensure optimal performance and high-quality welds. This table presents a comparison of various indicators that can help in the selection process. The indicators considered in this table provide important insights into the capabilities and specifications of TIG welders specifically designed for aluminum welding.
Indicator | Explanation |
---|---|
Amperage Range | The range of current (amperage) settings available on the TIG welder, indicating its versatility in handling different aluminum thicknesses. |
Duty Cycle | Represents the percentage of time a TIG welder can operate within a 10-minute cycle without overheating. Higher duty cycles indicate longer continuous welding periods. |
AC/DC Capability | Indicates whether the TIG welder can switch between alternating current (AC) and direct current (DC) welding modes. AC is used for aluminum welding, while DC is suitable for other metals. |
Pulse Frequency | Refers to the frequency at which the TIG welder pulses the current during welding. Higher pulse frequencies enable better control and reduced heat input, ideal for thin aluminum sheets. |
High-Frequency Start | Presence of a high-frequency start feature enables easy and consistent arc initiation, especially for aluminum welding, resulting in clean and precise weld starts. |
Gas Control | The ability to control the flow of shielding gas, typically argon, which protects the weld pool from atmospheric contamination during the welding process. |
Foot Pedal Control | Offers the option to control amperage settings using a foot pedal, providing more precise control over the welding process, especially during intricate aluminum welds. |
Post Gas Flow | Refers to the duration for which the shielding gas continues to flow after the welding arc is extinguished, ensuring proper cooling and preventing oxidation of the weld. |
Weight | The weight of the TIG welder, which can influence its portability and ease of handling, especially in various work environments. |
Price | The cost of the TIG welder, which is an important factor to consider based on the budget and requirements of the welding project. |
This table provides a comprehensive overview of the indicators to consider when selecting a TIG welder for aluminum welding. The indicators cover various aspects such as amperage range, duty cycle, AC/DC capability, pulse frequency, high-frequency start, gas control, foot pedal control, post gas flow, weight, and price. By comparing these indicators, welders can make informed decisions based on their specific aluminum welding needs, ensuring the chosen TIG welder meets the necessary requirements for successful aluminum
FAQ
What is the best use of TIG welding?
There are many different ways to utilize TIG welding, but some of the most popular uses include fabricating race cars, repairing aircraft, and creating art pieces. TIG welding is also commonly used in the manufacturing industry for tasks such as joining stainless steel pipes or aluminum tubing. In general, TIG welding is a versatile process that can be used for a variety of projects.
What is the welding current used in TIG welding?
The welding current used in TIG welding can range from 40 to 400 amps. The power required for the weld depends on the thickness of the metal being welded, as well as the type of filler material used. In general, thicker metals require more power and may need to be welded at higher currents.
Can you weld aluminum with a DC TIG welder?
Yes, you can weld aluminum with a DC TIG welder. DC TIG welders are often the preferred choice for welding aluminum, as they provide more consistent results. AC TIG welders can also be used to weld aluminum, but they may produce more sparks and spatter.
When should I use air-cooled and water-cooled TIG torches?
Air-cooled TIG torches are typically used for welding applications that do not require high levels of power. They are lighter in weight and more comfortable to use, making them a good choice for projects that involve welding for extended periods.
Water-cooled TIG torches are typically used for welding applications that require higher levels of power. The water helps to keep the torch cool, which prevents damage to the torch and extends its lifespan. However, water-cooled TIG torches are heavier and more expensive than air-cooled models.
Can I use TIG welding for outdoor work?
Yes, you can use TIG welding for outdoor work. However, it is important to choose a welder that is designed for outdoor use. Outdoor welders are typically more durable and have higher duty cycles than indoor welders. They also often have features that make them easier to use in windy or dusty conditions, such as enclosed cabinets and filters.
Why are TIG welders so expensive?
TIG welders are often more expensive than other types of welders because they offer a higher level of precision and control. TIG welding is a delicate process that requires a steady hand and a great deal of practice to master. As such, TIG welders are typically only used by experienced welders or those who are willing to invest the time and effort into learning how to use them properly.
Is TIG stronger than MIG? (TIG vs MIG)
There is no definitive answer to this question as the strength of a weld depends on many factors, such as the type of metal being welded and the welding technique used. In general, TIG welding is considered to be a more precise process than MIG welding, which can result in stronger welds. However, MIG welding is typically faster and easier to learn, making it a good choice for less experienced welders. TIG welding is a versatile process that can be used for a variety of projects. The power required for the weld depends on the thickness of the metal being welded, as well as the type of filler material used. DC TIG welders are often the preferred choice for welding aluminum, as they provide more consistent results.
Can All TIG Welders weld aluminum?
No, not all TIG welders can weld aluminum. In order to weld aluminum, you need a welder that is specifically designed for that purpose. Aluminum welding requires high levels of power and can be very challenging, so it is important to choose a welder that is up to the task. Some of the best TIG welders for aluminum include the Miller Maxstar 150 STH, the Lincoln Electric Power MIG 210 MP, and the Hobart EZ-TIG 165i.
Do you TIG Weld Aluminum on AC or DC?
You can weld aluminum on both AC and DC. However, DC is often the preferred choice as it provides more consistent results. AC TIG welders can also be used to weld aluminum, but they may produce more sparks and spatter.
What is the best entry-level TIG welder?
The best entry-level TIG welder is the Lincoln Electric Power MIG 210 MP. This welder is a versatile, all-in-one machine that can be used for a variety of projects. It is easy to set up and use, making it a good choice for those who are new to welding. The Power MIG 210 MP also has an impressive duty cycle and comes with a wide range of accessories, making it a great value for the money. If you’re looking for a more budget-friendly option, the Hobart EZ-TIG 165i is a good choice. This welder is specifically designed for aluminum welding and offers many of the same features as the Lincoln Electric model.
Is TIG welding stronger than stick welding?
Again, there is no definitive answer to this question as the strength of a weld depends on many factors. In general, TIG welding is considered to be a more precise process than stick welding, which can result in stronger welds. However, stick welding is typically faster and easier to learn, making it a good choice for less experienced welders.
Can you TIG weld without gas?
No, you cannot TIG weld without gas. TIG welding requires an inert gas, such as argon or helium, to protect the weld from oxygen and other contaminants.
How long does a TIG welder last?
With proper care and maintenance, a TIG welder can last for many years. However, the lifespan of a welder will vary depending on the brand, model, and how often it is used. On average, a TIG welder has a lifespan of about 15 years.
What metals cannot be welded together?
Some metals cannot be welded together. For example, aluminum and stainless steel cannot be welded together because they expand and contract at different rates when heated. This can cause the weld to crack or break. Additionally, certain metals, such as lead and zinc, should not be welded because they release toxic fumes when heated.
Can you teach yourself to TIG weld?
Yes, you can teach yourself to TIG weld. However, it is important to note that welding is a potentially dangerous activity. It is always best to seek out professional instruction before attempting to weld on your own. There are many welding schools and classes available, or you can find online tutorials and resources.
Can you weld titanium to steel?
Yes, you can weld titanium to steel. However, it is important to use the correct type of filler material. Titanium is a difficult metal to weld and requires a special set of skills and knowledge. As such, it is always best to seek out professional help when welding titanium.
What are the disadvantages of TIG welding?
Some of the disadvantages of TIG welding include the fact that it is a slower process than other welding methods, and it can be more difficult to learn. Additionally, TIG welders are typically more expensive than other types of welders.
What are the benefits of using TIG welders for aluminum?
TIG welders offer several advantages when it comes to welding aluminum. These include:
- High-quality welds: TIG welding produces clean, precise welds with excellent visual appearance.
- Low heat input: TIG welding allows for precise control of heat input, which helps prevent distortion and warping of the aluminum workpiece.
- Good weld fusion: TIG welding provides deep weld penetration and fusion, resulting in strong and durable welds.
- No spatter: Unlike other welding processes, TIG welding does not produce spatter, which means minimal cleanup is required.
- Wide range of applications: TIG welders are versatile and can be used for various aluminum welding applications, including automotive, aerospace, and fabrication.
What type of tungsten electrode should I use for TIG welding aluminum?
When TIG welding aluminum, it is recommended to use a pure tungsten electrode or a tungsten alloyed with a small amount of zirconium. These electrodes have excellent arc stability and resistance to contamination.
What shielding gas should I use for TIG welding aluminum?
Argon is the most commonly used shielding gas for TIG welding aluminum. It provides excellent coverage and protection for the weld pool, preventing oxidation and ensuring clean, high-quality welds. In some cases, helium may be added to the argon to increase heat input and improve welding speed.
What is AC balance and why is it important for TIG welding aluminum?
AC balance, also known as the cleaning action or cleaning effect, is a feature found in many TIG welders. It controls the ratio of time during the alternating current (AC) cycle that is spent on cleaning the aluminum oxide layer and time spent on welding the base metal. Proper AC balance is crucial for TIG welding aluminum because it helps remove the oxide layer, ensuring good weld penetration and preventing defects.
What are some important considerations for TIG welding aluminum?
When TIG welding aluminum, it is essential to keep the following considerations in mind:
- Cleanliness: Aluminum is highly reactive and prone to contamination, so ensure that the workpiece is clean and free from oils, grease, and oxides.
- Fit-up and joint preparation: Proper fit-up and joint preparation are crucial for successful aluminum welding. Make sure the edges are properly beveled, and the gap between the pieces is appropriate.
- Amperage and travel speed: Adjust the welding amperage and travel speed according to the thickness of the aluminum to achieve optimal penetration and prevent burn-through or lack of fusion.
- Torch angle and manipulation: Maintain a slight torch angle and use proper manipulation techniques to ensure even heat distribution and consistent weld bead formation.
- Post-weld cleaning: After welding, remove any post-weld contamination and oxide residue using appropriate cleaning methods to preserve the integrity of the weld.
What are some common joint designs used in TIG welding aluminum?
Common joint designs for TIG welding aluminum include butt joints, lap joints, T-joints, and corner joints. The specific joint design depends on the application and the configuration of the aluminum components being welded.
What are the limitations of TIG welding aluminum?
While TIG welding is an excellent process for aluminum, it does have some limitations:
- Slower welding speed: TIG welding is generally slower compared to other welding processes, which can be a disadvantage when working on large projects.
- Higher skill requirements: TIG welding requires a high level of skill and precision. It can take time to develop the necessary technique and hand-eye coordination for successful aluminum welding.
- Higher equipment cost: TIG welders are typically more expensive than other types of welders, which may be a barrier for some users.
Useful Video: Good TIG Welder for Under $1,000
Conclusion
The TIG Welders for Aluminum are the best in the market and can help you with any welding project. With the proper care and attention, these welders will last for years. The reviewed welder models are of excellent quality and will serve you well. They have a wide range of settings such as amperage and duty cycle that can be adjusted according to the needs of your project. You can also find a welder with an automatic or semi-automatic feature. The TIG Welders for Aluminum are easy to use and offer great value for money. With the right welder, you can complete any welding project successfully. Follow the tips in this guide and choose the best TIG Welder for your needs.
References:
- https://engweld.co.uk/talk/key-things-to-consider-when-choosing-your-tig-welder/
- https://bakersgas.com/pages/how-to-choose-a-tig-welder
- https://weldguru.com/tig-welding-aluminum/
- https://www.millerwelds.com/resources/article-library/tig-welding-aluminum-for-beginners-steps-1-2