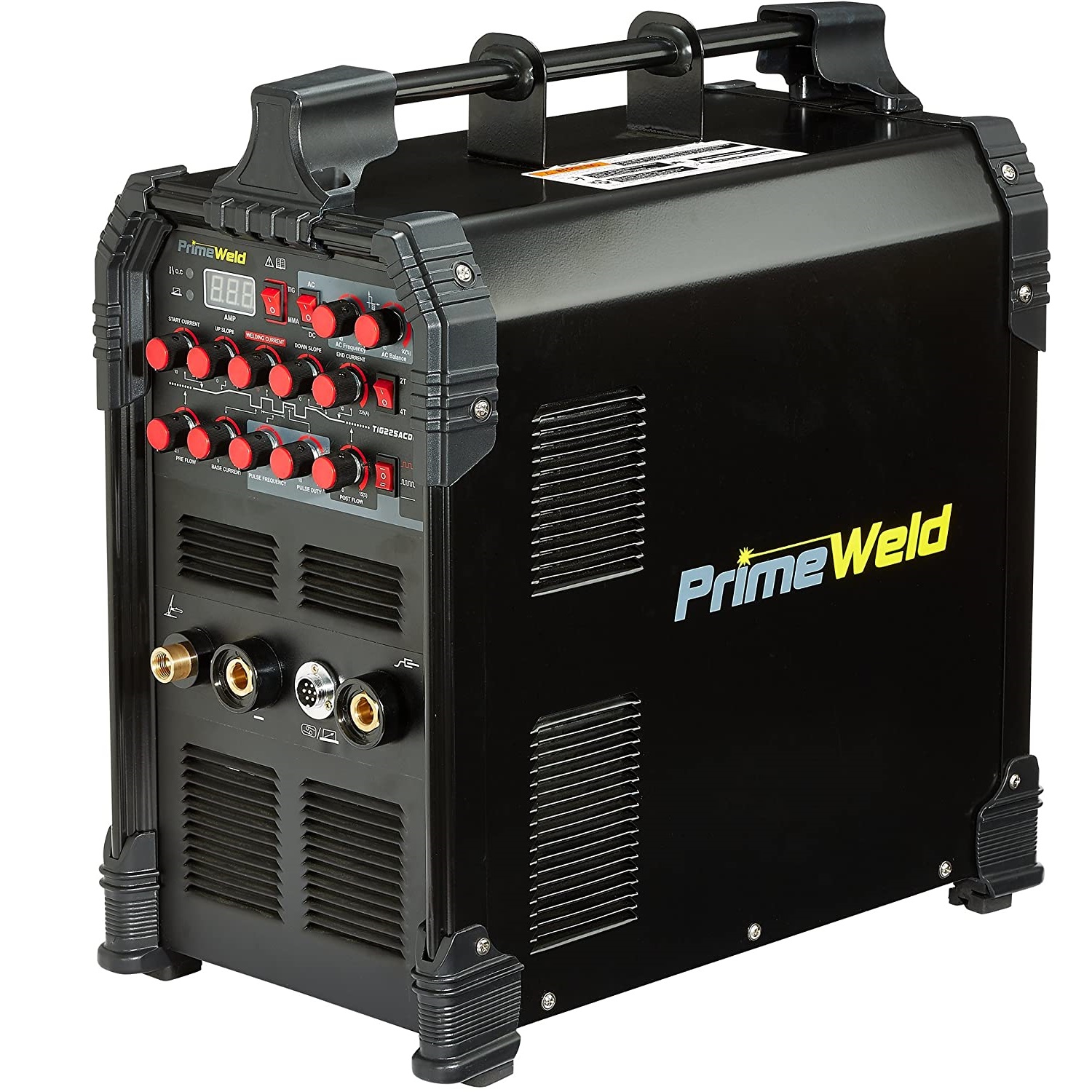
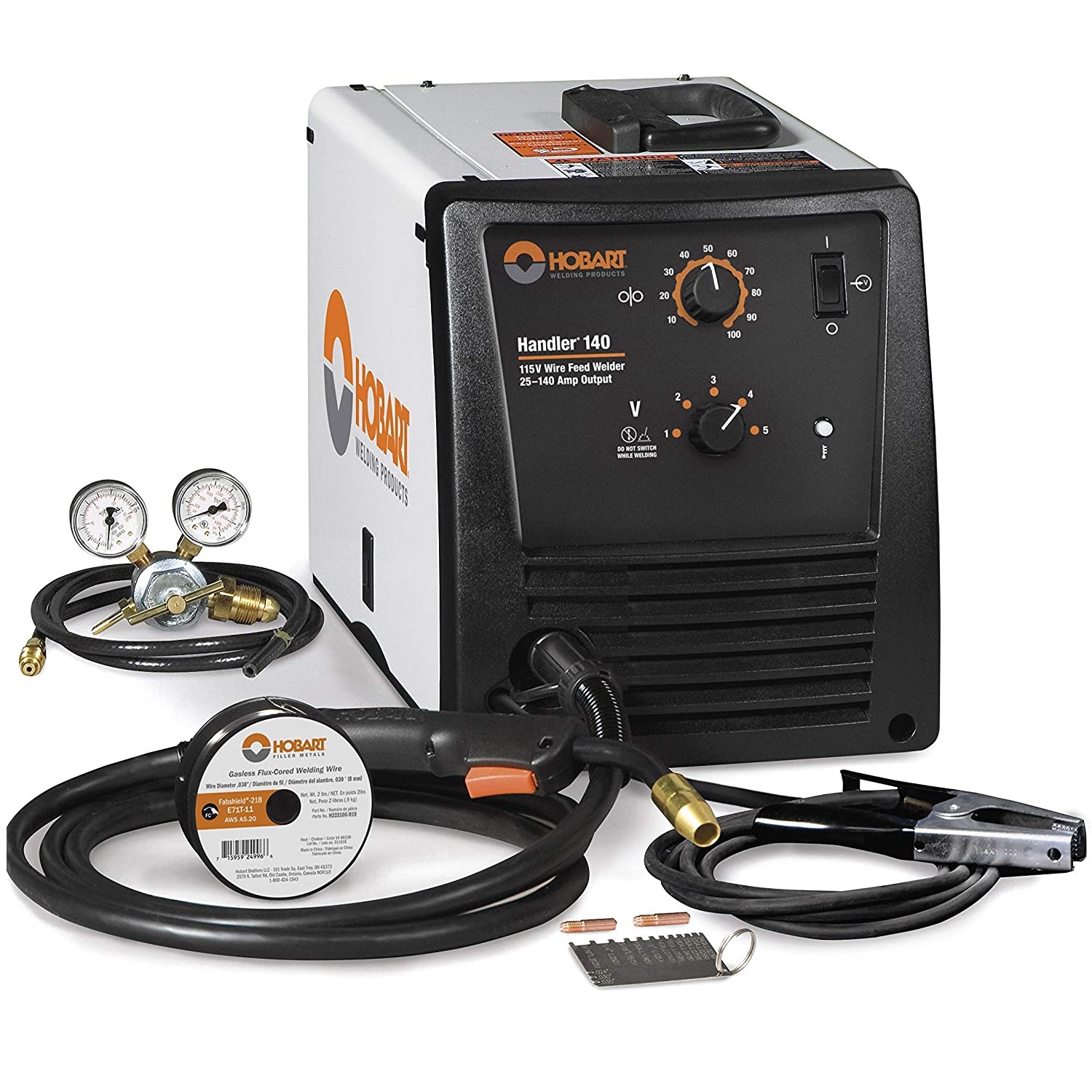
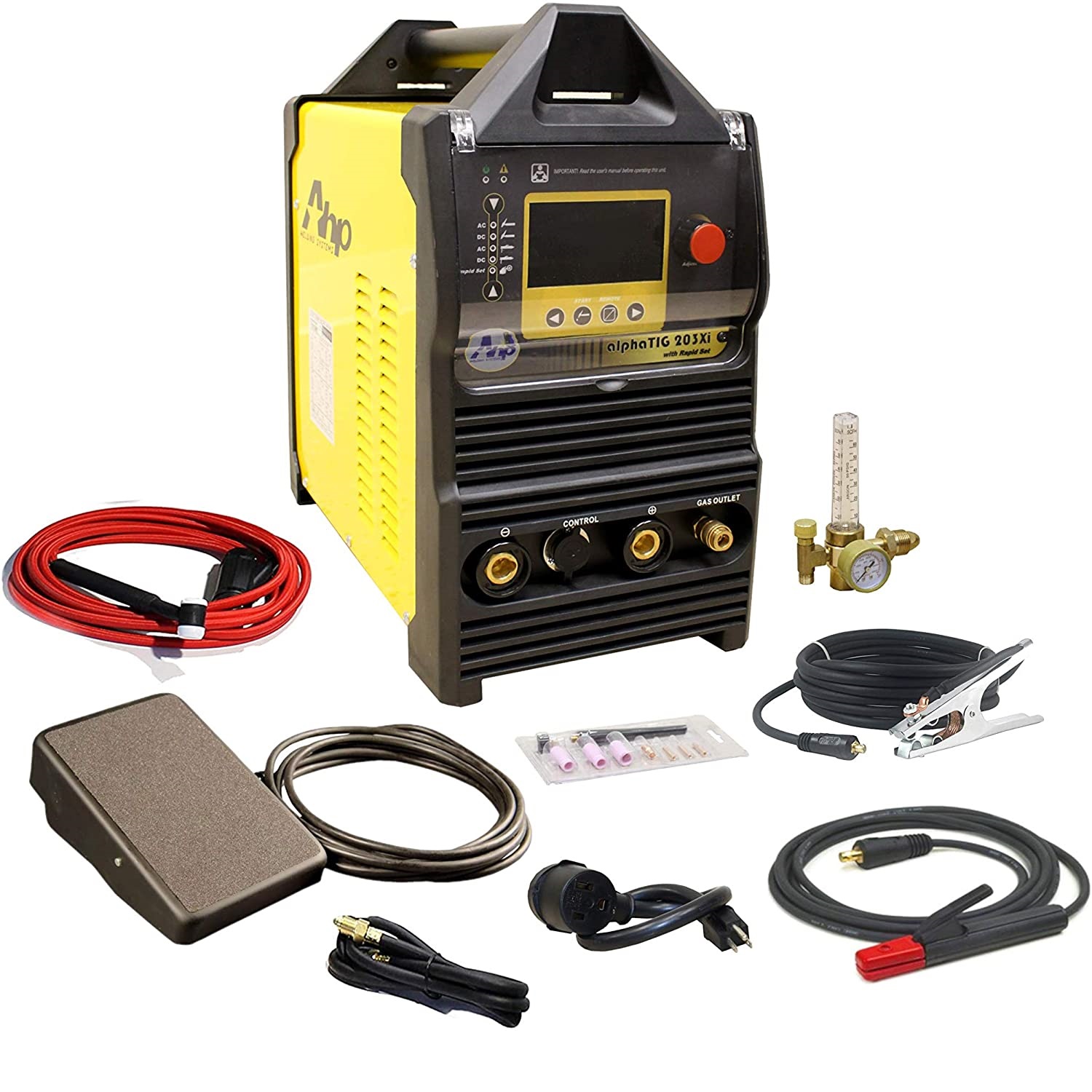
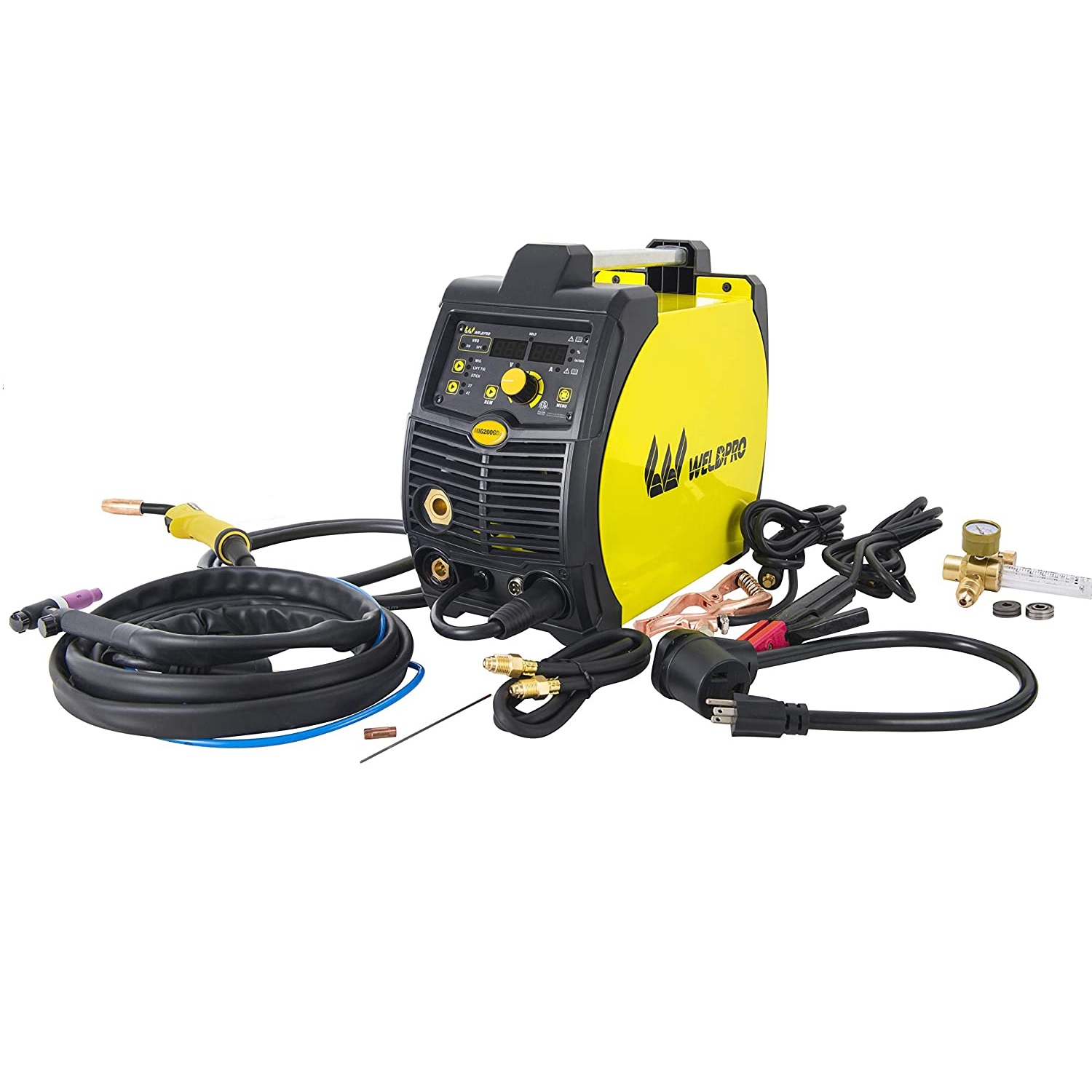
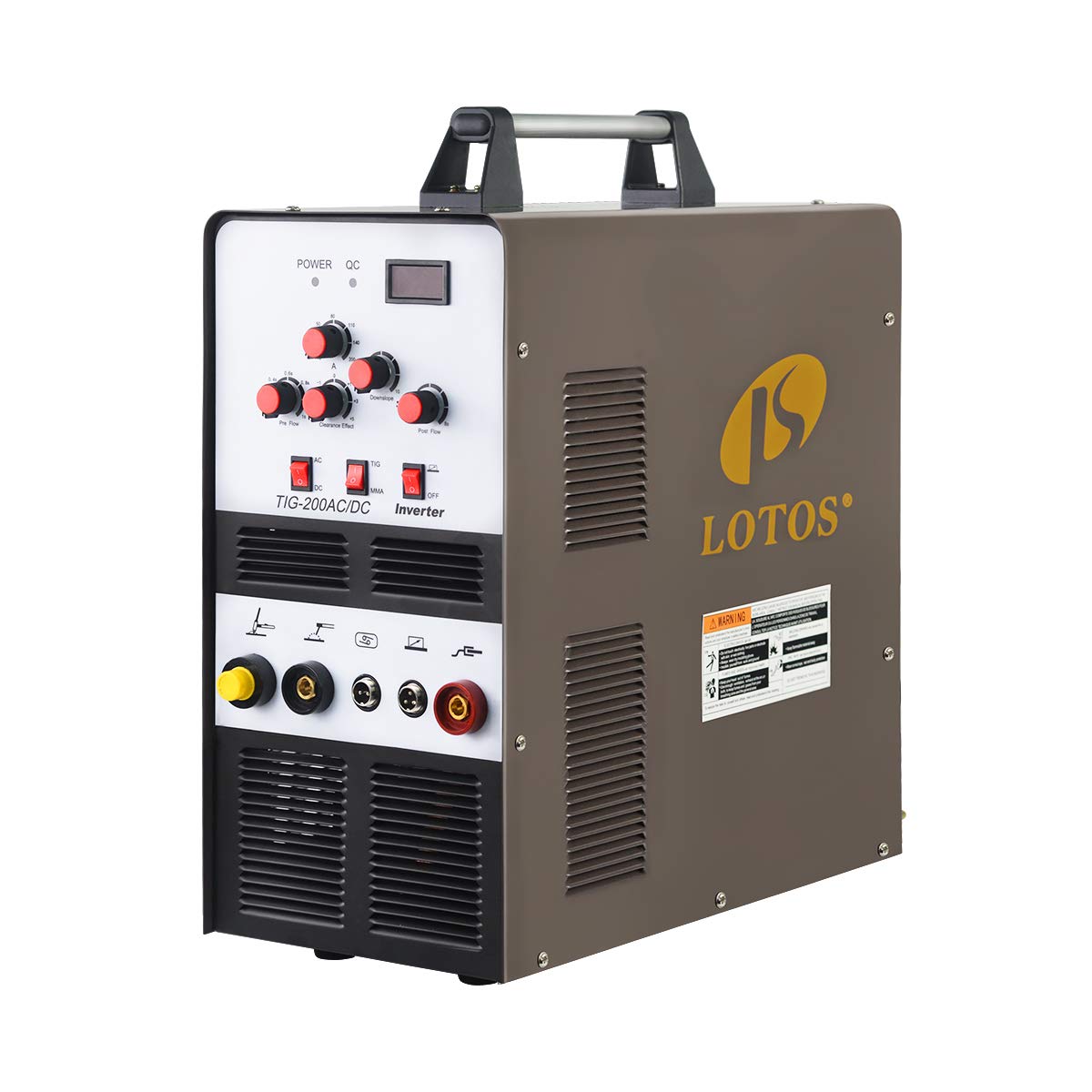
Choose the Best Welder for Sheet Metal
Customer’s Choice: the Best Rated Welders for Sheet Metal
13 users answered this survey. Please help us improve this review!
Welding is a process that joins two pieces of metal together by melting and fusing the base metals together. The welders use an electric arc or a gas flame to create this fusion. Welders are used in a variety of applications, from automotive repair to construction.
Welders for sheet metal come in all shapes and sizes, with a variety of features that can be confusing for the first-time buyer. In this article, we will discuss the best welders for sheet metal. We will provide product reviews and useful tips to help you choose the right welder for your needs!
PRIMEWELD TIG225X 225 Amp IGBT AC DC Tig/Stick Welder
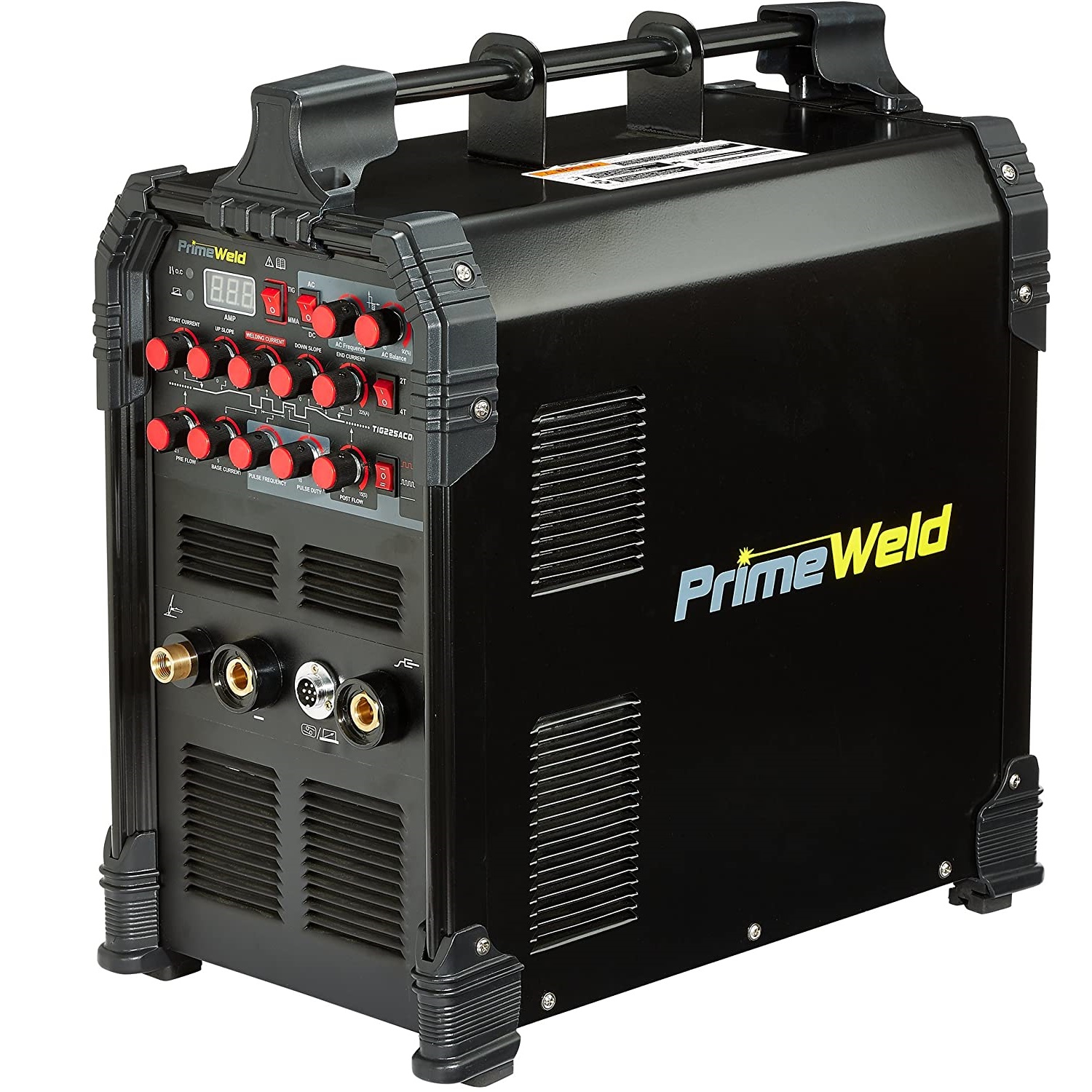
However, the foot pedal may be difficult to use at first and needs to be trained. The manual may also provide insufficient information on how to fully set up the equipment.
Hobart 500559 Handler 140 MIG Welder
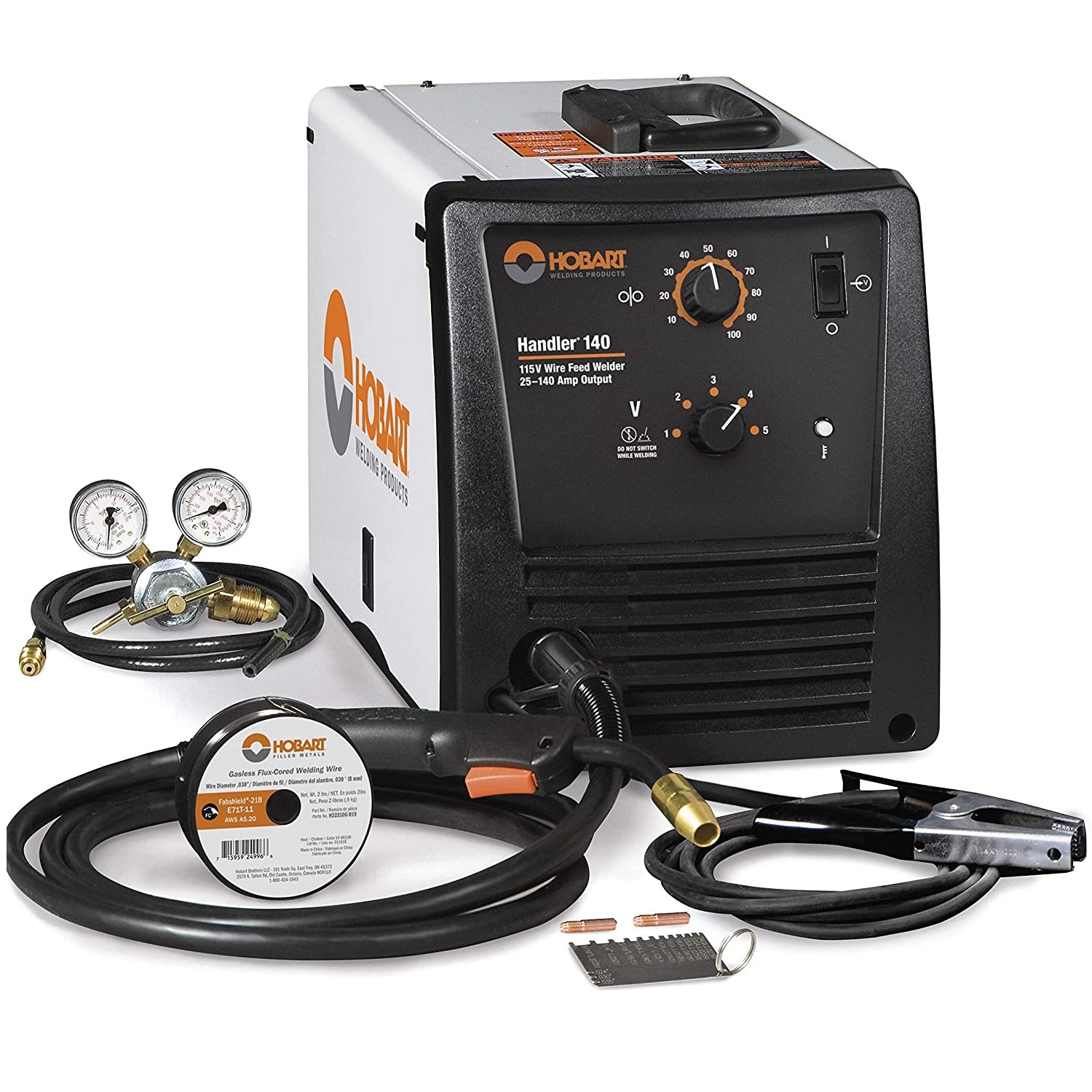
Unfortunately, the Hobart 500559 Handler 140 MIG welder has some shortcomings. The wire feed knob is excessively mobile, and it may flip at any moment during welding. The cooling fan is noisy and its hard to ignore that.
2018 AHP AlphaTIG 200X 200 Amp IGBT AC DC Tig/Stick Welder
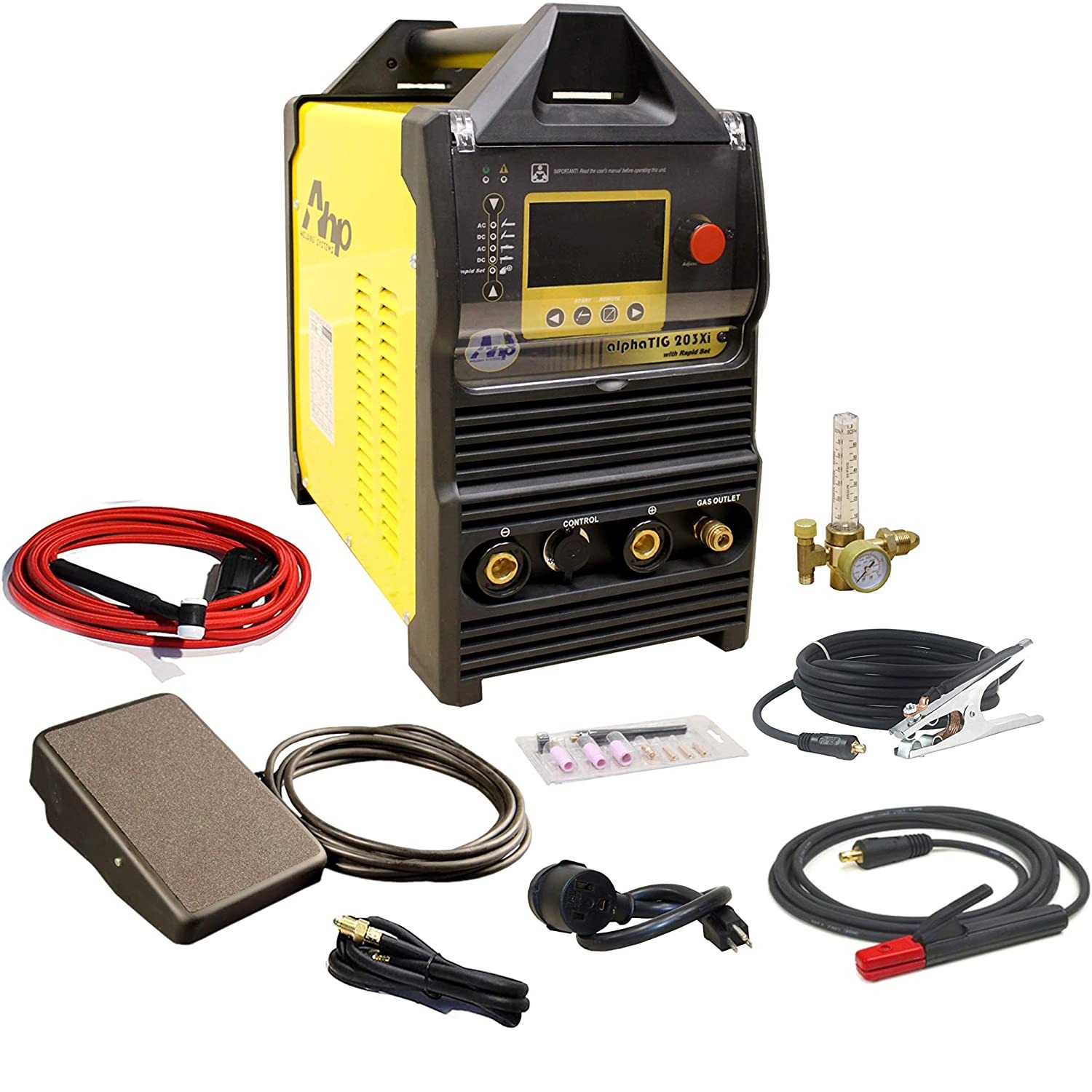
The positioning of the welding machine’s clamps and a delicate foot pedal are two reasons it’s difficult to use. Because there is no lift arc, they are uncomfortable to operate for lengthy periods on carpentry or building tasks where your feet must be near the ground at all times.
Weldpro 200 Amp Inverter Multi Process Welder
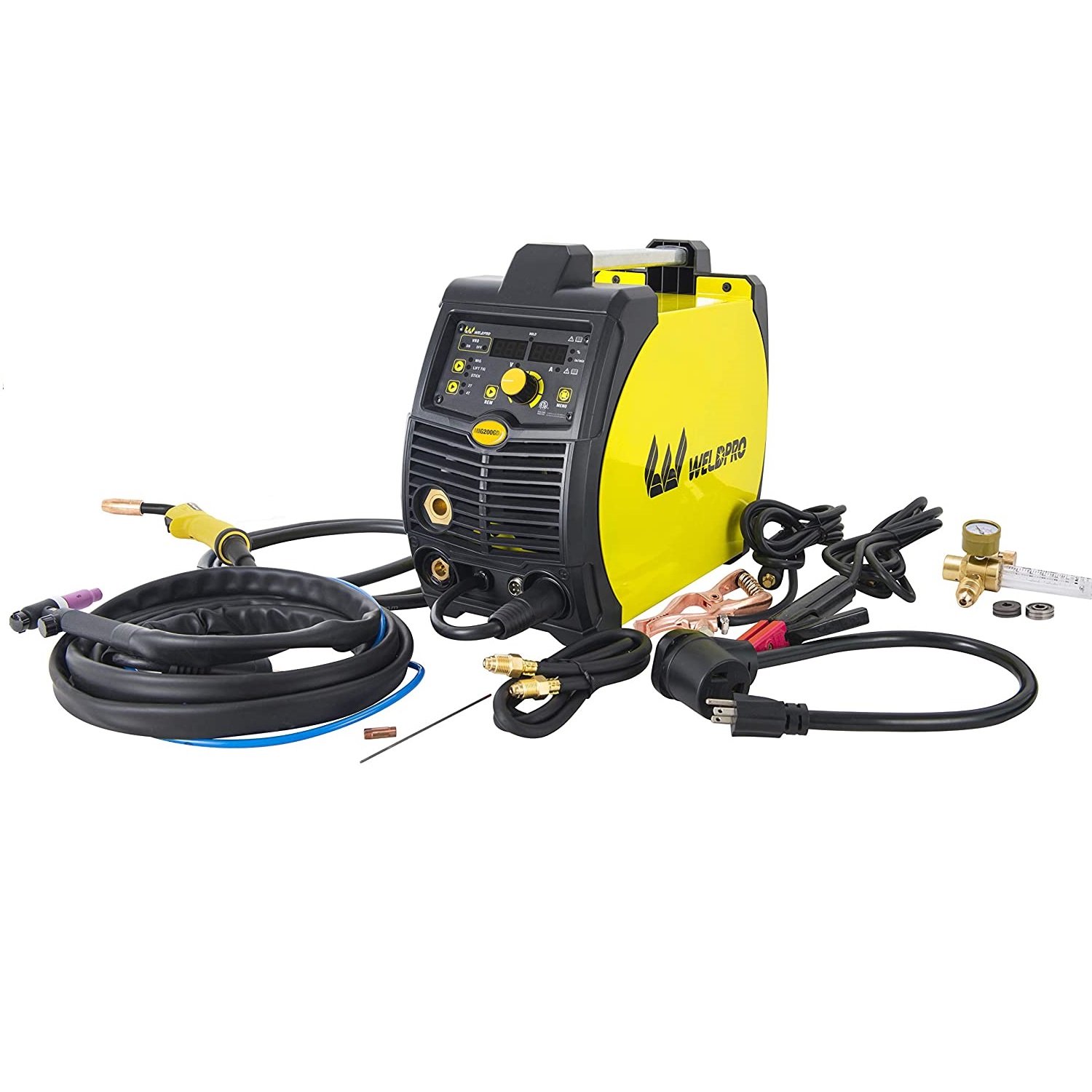
This welder also includes both Stick and MIG welding modes, so you can tackle any project with ease. Plus, the voltage adjustment feature lets you customize your welds according to your specific needs. Whether you’re a beginner or a pro, this welder is sure to help you get the job done right. Plus, it’s backed by a friendly customer service team that’s always happy to help.
But this welding machine still comes with negatives. For one thing, the wire speed can overrun the heat output if you’re not careful, so make sure you’re paying attention because it may be hard to control the welding process perfectly. Second of all, the weld still runs for a few seconds after you finish your work. Last but not least, the instructions are pretty vague, so make sure you do your research before using this machine.
LOTOS TIG200ACDC 200A AC/DC Aluminum Tig Welder
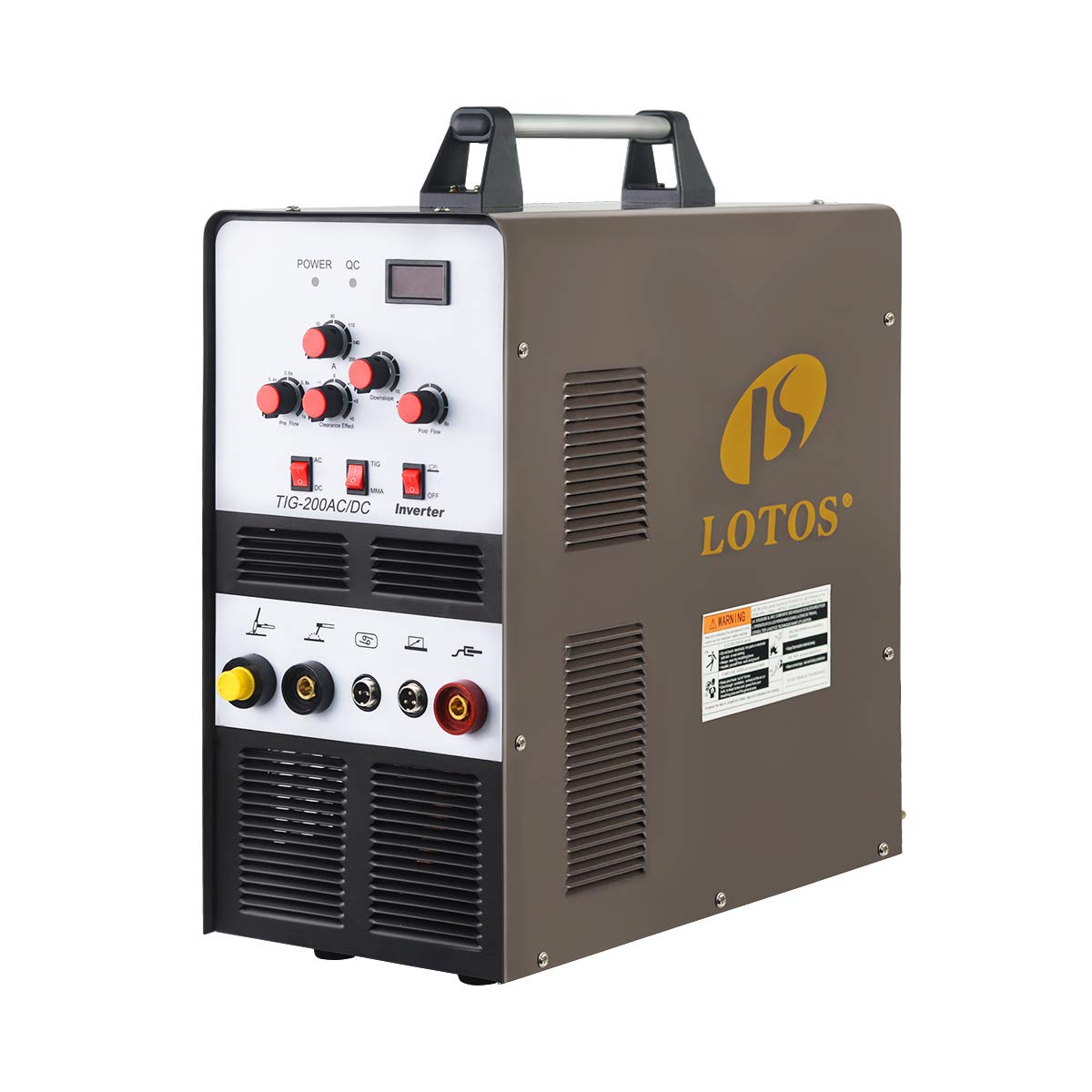
But there are a few things you should know before you buy it. First, you have to turn it off when switching between modes. Second, the foot petal cord is located a little too low for some people’s comfort. And finally, the numbers displayed on the digital display may not match the numbers on the amps dial – but that’s nothing you can’t figure a workaround for.
Buyer’s Guide
Basics of the Sheet Metal Welding Process
Sheet metal welding is a process where the welder uses an electric arc to join two pieces of metal together. Welders usually wear protective equipment, including glasses and masks that protect them from sparks or hot particles flying out during operation. Ears can also be protected with damp cloths so you can still hear sound without issues when working near machines set on loud noises.
There’s a lot of different types welding machines out there, but they can be broken down into two categories: gas and stick. MIG welders are typically used for metal with less grease-cutting resistance like aluminum or zinc sheets. TIG welding is a type of welding that works better with thicker steels. This is because it creates cleaner joints without adding too much heat. This can cause the steel to expand and contract when it’s used in elevated temperatures, for example on bridges. TIG welding also has greater application versatility because you can use the same setup whether you’re working from above ground level or underwater. Each type has its own advantages and disadvantages. [1],[2],[3]
The most important factor in choosing a welder for sheet metal is determining the thickness of the metal you will be welding. The welder should be able to generate an arc with a heat output that is high enough to melt the metals, but not so high that it damages them.
Types of Welding Methods
The three most common welding methods are Stick Welding, MIG Welding and TIG Welding:
- Stick welding is the most common type of welding. It uses a consumable electrode that is stick-shaped. The electrode is placed in the weld puddle. When welding two pieces of metal together, an electric arc is created between the two pieces. This arc produces high temperatures, up to 6500oF, which melts the electrode and the metal.
- MIG welding is a process that uses a gun, continuously fed with a consumable electrode. This electrode creates the welded metal while an external gas shields it from environmental factors like oxygen. This makes the weld continuous and quick. MIG welding is easy to learn, produces less welding fumes, has high electrode efficiency and requires less heat input.
- TIG welding is a difficult process that takes a lot of skill and focus. An autogenous weld is created by melting two pieces of metal together without using filler metal. TIG produces high-quality welds of different types of alloys, but it requires a skilled operator and external shielding gas. It also doesn’t work on rusty or dirty materials.
Each of these welding methods has its own advantages and disadvantages. For sheet metal welding, the best method depends on the thickness of the metal being welded and the type of metals being used.[1],[2],[3]
TIG welding
TIG welding is the best method for welding thin sheet metal. It produces a very clean weld with no spatter, and it is mostly used for aerospace welding, tubing, vehicle and bike manufacturing. TIG welding also requires the least amount of post-weld cleanup but it does require the skill.
TIG welders have been around for a long time and can be used to make almost anything. They’re also very versatile, so it’s no surprise that they would find popularity among hobbyists as well! However such versality comes at an expense, as TIG welding is the most expensive type of welder out there.
So if you are looking for the welder that leaves the least mess, TIG welding is the way to go. It produces a clean weld with no spatter, and it can be used to weld a variety of metals. [1],[2],[3]
MIG welding
MIG welds are excellent for welding thicker sheet metal. They produce a strong, durable bond with little or no spatter and they’re easy to use.
MIG welders are one of the most popular types of welding machines. They are easy to use and produce high-quality welds. However, they can be expensive compared to other types of welders and require a shielding gas to protect the weld from contamination.
With its versatility, MIG welding is a great choice for anyone looking to produce strong welds with minimal effort. It can be used on any number of different types metals including aluminum and stainless steel.
In some cases, you might not need an adapter because most welders already have a built-in transformer that provides them with enough volts of power. [1],[2],[3]
Stick welding and spot welding
Stick welding is the best method for joining thicker sheet metal. It produces a strong, durable weld with minimal spatter and it’s easy to learn too! The only drawback? You need gas protection.
Stick welders are the most affordable type of welding machines and are a good option for beginners. However, they can be difficult to use and produce less-quality welds than other types of welders.
Stick welding is also often too hot and forceful for brittle sheet metal, but it is ideal when working with thicker metals like steel. [1],[2],[2]
So to summarize it all up:
- MIG welding is a popular choice for those who need to work with different types of metals. It’s easy enough that even beginners can learn it, but you do have the cost issue of equipment – which may make this form less accessible than stick welderies.
- TIG welding is a good choice for both thin and thick metals because it has a very low heat output. However, TIG welding is more difficult than MIG or Stick welding, and requires more practice to produce a consistent weld bead.
- Stick welding is a good choice for thick metals because it produces high heat output. However, it can be difficult to produce a consistent weld bead with stick welding. The electrode also produces fumes that are harmful to breathe.
In the end, choosing the best welder for sheet metal depends on the thickness and type of metal being welded. If you are unsure which welding method is best for your project, consult a professional welder or welding supplier. They can help you choose the right welder for your needs and give you tips on how to use it safely and effectively.
So now you know the basics, but which welder should you buy? It’s difficult to answer this question because their strengths differ drastically. Here are some of the best welders for sheet metal that are available on the market today.
What to Consider When Buying the Best Welder for Sheet Metal
Now that you know some of the best welders available on the market, it’s time to decide which one is right for your needs. Here are some basic factors to consider before making your purchase:
The type of metal you’ll be welding: Aluminum requires a different welding process than steel, so make sure to choose a welder that is designed for the type of metal you’ll be working with.
The thickness of the metal: Thicker metals require more power and may need a different welding process altogether. Be sure to take this into consideration when choosing a welder.
Your budget: Welders can range in price from a few hundred dollars to several thousand, so it’s important to know how much you’re willing to spend before making a purchase.
Your level of experience: If you’re a beginner, it’s important to choose a welder that is easy to use and has clear instructions. More experienced welders may want to opt for a more powerful machine. [4],[5],[6]
Let’s dig a little deeper into some more factors to consider before making a purchase.
Welding Process Capabilities
The welding process capabilities of a machine are important to consider because some machines are only good for specific types of welding. If you want a machine that can do it all, then you’ll have to spend a little bit more money. But, if you know what type of welding you’ll mostly be doing, then you can save some money by choosing a machine that is designed specifically for that process. [4],[5],[6]
Some welders are only good for stick welding while others can do both MIG and TIG. There are even some machines that can do all three. If you know you’ll only be doing one type of welding, then there’s no need to spend the extra money on a machine that can do all three. All-in-one welders typically have a higher price tag, but they are worth the investment if you are completely set on doing a variety of welding projects.[4],[5],[6]
Amperage concerns
The next factor to consider is amperage. Amperage is the unit of measurement used to determine the strength of an electrical current. In welding, it’s important to choose a machine with enough amperage to get the job done. If you’re working on thicker metals, you’ll need a machine with more power and thus, more amps.
If you’re planning on doing any heavy-duty projects, then you’ll need a machine with 200 amps or more, for smaller projects around 140 amps will do fine. [4],[5],[6],[10]
Input Voltage
Another thing to consider is input voltage. Welders require a higher voltage than what your standard home outlet can provide, so you’ll need to use an adapter or welding machine transformer to increase the voltage.
The input voltage of a welder ranges from 110 volts to 220 volts. If you have a standard home outlet with 120-volt service, then you’ll need an adapter or transformer that increases the voltage to 220 volts in order for the welder to work properly.
In some cases, you might not need an adapter because most welders already have a built-in transformer that provides them with enough volts of power. [4],[5],[5],[10]
Duty cycle rating
Another thing to consider is duty cycle. Duty cycle is the amount of that a welder can be used in a ten-minute period without overloading. For example, a welder with a 20% duty cycle can be used for two minutes out of every 8 minutes before it needs to cool down.
Duty cycle is important to consider because it will determine how long you can weld before taking a break. If you’re planning on doing any big projects, then you’ll need a machine with a high duty cycle rating so that you can weld for longer periods of time without having to take breaks.
In general, the higher the amp rating, the lower the duty cycle. So, if you’re looking for a machine that can handle big projects, then you’ll have to sacrifice some duty cycle for extra power. [4],[5],[6],[7],[10]
Welding Wire Support
Another factor that is important to consider when choosing a welder is the welding wire support. The welding wire support is what holds the welding wire in place while you are working. Some welders have a built-in support, while others do not. If you choose a welder without a built-in support, you’ll need to purchase one separately.
The type of welding wire support you need will depend on the type of welding you plan on doing. If you’re only going to be doing light-duty projects, then you won’t need a heavy-duty support. However, if you’re planning on doing any heavy-duty projects, then you’ll need a stronger support.
GMAW wire is the most common type of welding wire and it is good for both light-duty and heavy-duty projects. Composite GMAW (metal-cored) wire is a better option for heavy-duty projects because it has a higher amp rating than GMAW wire. Gas-shielded flux-cored arc welding (FCAW) wire is the most versatile and is the best option for heavy-duty projects as it has the highest amp rating of all three types of welding wires.
Each of these have their own pros and cons, so if you’re not sure which type of welding wire support you need, ask the salesperson at your local hardware store. They will be able to help you choose the right one for your needs. [4], [8], [9]
Item Dimensions and Weight
When choosing a welder, it’s important to consider the item dimensions and weight. Some welders are large and bulky, while others are small and lightweight. If you don’t have enough space in your workshop or garage, then you’ll need to choose a smaller welder. Similarly, if you’re planning on taking your welder on the go, you’ll want one that is light and portable.
The size and weight of a welder will also affect how easy it is to use. Larger welders are typically harder to maneuver than smaller ones. So, if you’re not very strong or have joint problems, you’ll want to choose a smaller machine that is easier to handle.
Selecting the right size and weight of a welder is important, but it’s also important to consider the dimensions and weight of the welding wire. Some welders require a large welding wire that is difficult to find and transport. In general, the smaller the machine, the less power it has. So, if you’re looking for a machine with more power, you’ll have to choose one that is larger in size. [4]
Warranty
If you want to ensure that your welder never malfunction or give out on the job-site, it’s best to get a welder with a long warranty. Most welders come with a one-year warranty, but there are some that have a five-year warranty.
It’s important to read the terms and conditions of the warranty before purchasing a welder. Some warranties only cover certain parts of the machine, while others cover the entire machine.
Before you purchase a welder, make sure to ask about the warranty and read the terms and conditions carefully. This way, you’ll know exactly what you’re getting into and won’t be disappointed if something goes wrong with your machine. [4]
Welder Machine Material
When choosing a welder, it’s important to consider the machine material. Some welders are made from plastic, while others are made from metal. If you’re looking for a durable and long-lasting welder, then you’ll want one that is made from metal.
However, if you’re looking for a welder that is lightweight and easy to transport, then you’ll want one that is made from plastic. Plastic welders are also cheaper than metal welders. [4]
Additional Components
In addition to the welder, you will need some other components in order to get started. For example, you will need a welding helmet, gloves, and a welding rod. You especially need these if you are starting out.
You can purchase these items separately or as part of a welder kit. If you’re just getting started with welding, then it’s probably best to buy a welder kit that comes with all the necessary supplies. This way, you won’t have to worry about buying each item separately. [4]
Make sure to read the unbiased reviews of different welders before making a purchase to make sure you are getting the right machine for your needs.
Here are some more tips on choosing the best welder for yourself:
- Welders come in both portable and stationary models. Choose the model that best fits your needs.
- Make sure the welder has an adequate power supply to handle the project you are working on.
- Welding can be dangerous if not done correctly. Make sure to read the safety instructions included with your welder, and always wear protective gear when welding.
FAQ
What welder is best for thin sheet metal?
A welder with a high amp rating and a low duty cycle is best for thin sheet metal.
Can you weld sheet metal with a MIG welder?
Yes, you can weld sheet metal with a MIG welder. Just be sure to use the right settings and have proper ventilation. Actually, MIG welders are one of the best type of welder for sheet metal because they are less likely to cause warping and distortion. They are also easier to use than TIG welders and can be used for a variety of projects. Just be sure to use the right settings and have proper ventilation. Don’t forget to wear safety gear, too!
How thick of metal can a MIG welder weld?
MIG welders can weld up to about ¼ inch of metal. If you need to weld thicker metal, you’ll need a welder with more power.
Is MIG stronger than stick welding?
MIG welding is stronger than stick welding, but both processes have their own advantages and disadvantages. Stick welders are less expensive than MIG welders, while MIG welders are faster and easier to use. Choose the process that best fits your needs.
Useful Video: Welding Sheet Metal
Conclusion
So, what should you look for when purchasing a welding machine? First and foremost, be sure to consider the welding process capabilities of the machine. If you’re not sure what processes the machine can handle, ask the manufacturer or an experienced welder. Additionally, think about how often you plan on using the machine and what types of projects you will be working on. Finally, always compare prices before making your purchase—you may be able to find a good deal on an expanded welding machine that will meet all your needs.
If you’re still not sure which welder is right for you, be sure to read the reviews on Amazon or other welding supply websites. This will help give you a better idea of what each machine is capable of and which one is best suited for your needs. Thanks for reading and happy welding!
References:
- https://www.welderscave.com/best-welder-for-sheet-metal/
- https://www.thomasnet.com/articles/machinery-tools-supplies/best-welder-for-sheet-metal/
- https://blog.swantonweld.com/different-welding-methods
- https://weldzone.org/welders-for-sheet-metal/
- https://weldingvalue.com/2020/10/what-to-consider-when-buying-welding-machine/
- https://www.millerwelds.com/resources/article-library/buying-your-first-welder-a-practical-informative-guide-for-doityourselfers
- https://www.weldclass.com.au/blog/43-welding-machines-what-is-duty-cycle-how-is-it-calculated-
- https://www.corrosionpedia.com/definition/5127/welding-wire
- https://www.lincolnelectric.com/es-es/support/process-and-theory/Pages/mig-vs-flux-cored-detail.aspx
- https://training.esabna.com/mod/page/view.php?id=984