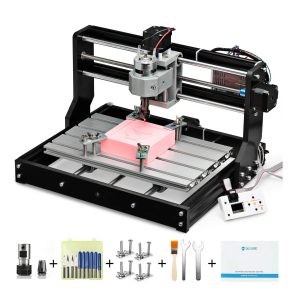
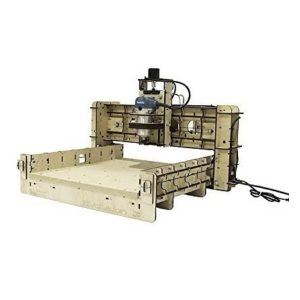
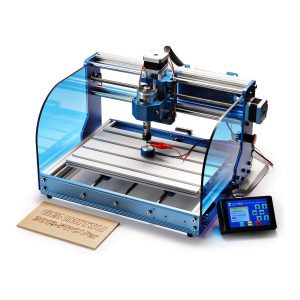
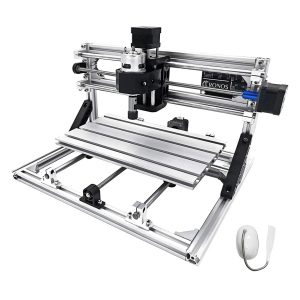
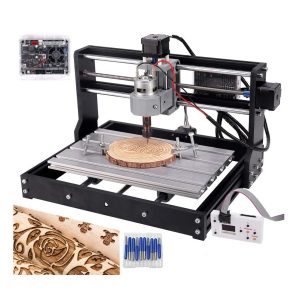
Choose the Best CNC Router for Aluminum
Customer’s Choice: the Best Rated CNC Routers for Aluminum
79 users answered this survey. Please help us improve this review!
There are a lot of factors to consider when purchasing a CNC Router for aluminum. Not only do you need to find a machine that is powerful enough to handle the job, but you also need to make sure that it is configured correctly for your specific needs. In this article, we will review some of the best machines on the market and provide you with some tips on how to get the most out of them.
When it comes to CNC Routers for aluminum, there are a few things that you need to keep in mind. First of all, you need to make sure that the machine is powerful enough to handle the material. Aluminum is a lot harder than other materials like wood, so you will need a machine that is specifically designed for it.
Let’s get started!
Genmitsu CNC 3018-PRO Router Kit GRBL Control 3
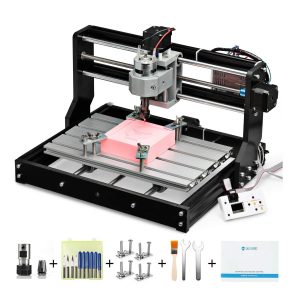
BobsCNC Evolution 3 CNC Router Kit with the Router Included (16″ x 18″ cutting area and 3.3″ Z travel)
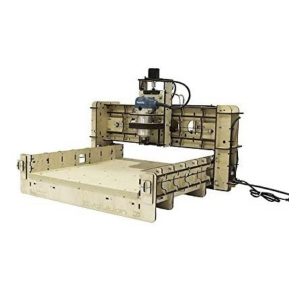
SainSmart Genmitsu 3018-PROVer Desktop CNC Router Machine
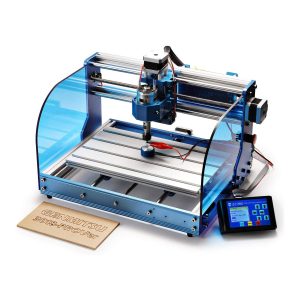
VEVOR CNC 3018 CNC Router Kit 3 Axis CNC Router Machine
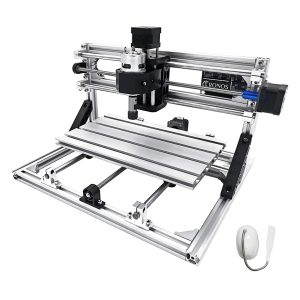
Cenoz Upgrade CNC 3018 Pro GRBL Control DIY CNC Machine
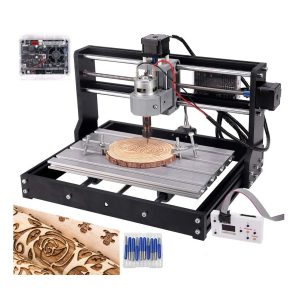
Buyer’s Guide
What you need to consider when buying such a CNC Routers
Drive System
The first thing you need to think about is what sort of drive system the CNC Router has. The three most common types are lead screw, ball screw, and rack and pinion. Lead screw systems are the slowest but most precise option. Ball screw systems are faster and more precise than lead screw systems. Rack and pinion systems are the fastest but least precise option. [1]
Motor System
The motor system of a CNC router is one of the most important aspects to consider. There are three main types of motors used in CNC routers: stepper motors, servo motors, and brushless DC motors. Stepper motors are the most common type of motor used in CNC routers. They are known for their high torque and low speed capabilities. Servo motors are more expensive than stepper motors, but they offer higher speeds and accelerations. Brushless DC motors are the newest type of motor on the market and offer the best performance in terms of speed and accuracy. However, they are also the most expensive type of motor.
When choosing a CNC router, it is important to consider the specific needs of your project. If you need a high-speed machine, then you will want to choose a router with servo motors. If you need a machine that is more accurate, then you will want to choose a router with brushless DC motors. However, if you are on a budget, then a stepper motor router may be the best option for you.[1]
Spindle
The spindle is the part of the CNC router that actually cuts the material. It is mounted on the Z-axis and spins at high speeds to cut through the material. There are two main types of spindles: air-cooled and liquid-cooled. Air-cooled spindles are less expensive than liquid-cooled spindles, but they are not as effective at cooling the motor and can overheat if used for extended periods of time. Liquid-cooled spindles are more expensive, but they offer better cooling and can be used for longer periods of time without overheating.
Weight
The weight of a CNC router is an important consideration for many users. Routers that are too heavy can be difficult to move around, and may require special lifting equipment. Conversely, very light routers may not be as sturdy as their heavier counterparts. A good compromise is to choose a router that is made from aluminum alloy, which is both strong and lightweight.[1]
Another factor to consider is the size of the work area. Some CNC routers have a very large work area, while others are more compact. If you plan on working with larger pieces of aluminum, you will need a router with a correspondingly large work area. On the other hand, if you only need to cut small pieces, a smaller router will suffice.
Table Size
The Size of the table is one of the most important aspects you need to consider when purchasing an aluminum CNC router.
If you plan on working with larger pieces of aluminum, then you’ll need to find a CNC router with a large enough table to accommodate your project.Prices
CNC routers for aluminum come in a wide range of prices. You can find entry-level models for around $300 and high-end models that cost upwards of $5000. The price will largely depend on the features and capabilities of the machine.
CNC Machining Aluminum: A Short Guide
Characteristics of aluminum
However, there are some characteristics of aluminum that can make it challenging to work with. One such characteristic is its ability to chip and break easily. This can lead to problems such as tool breakage, burrs, and uneven surfaces. Another challenge when machining aluminum is its high thermal conductivity. This means that heat generated by the cutting process can quickly build up, leading to tool wear and damage.There are a few things you can do to overcome these challenges and machine aluminum effectively. First, it is important to use sharp cutting tools. This will help to minimize tool breakage and chipping. It is also important to use coolant when machining aluminum. This will help to dissipate heat and prevent damage to the tool or workpiece. Finally, it is important to take light cuts when machining aluminum. This will help to prevent tool breakage and ensure a smooth, even surface. [2]
Types of CNC Routers for machinable aluminum
There are a few different types of CNC routers that can be used to machine aluminum. These include:
- Vertical Machining Centers (VMCs): VMCs are versatile machines that can be used for a variety of applications, including milling and drilling. They typically have a large table that can accommodate larger workpieces. VMCs are well suited for machining aluminum, as they provide good rigidity and precision.
- Horizontal Machining Centers (HMCs): HMCs are similar to VMCs, but they have a horizontally oriented spindle. This allows for more efficient chip removal and better accessibility to the workpiece. HMCs are also well suited for machining aluminum, as they provide good rigidity and precision.
- Bridge Mills: Bridge mills are large, heavy-duty machines that are typically used for machining large workpieces. They have a wide span between the columns, which provides good stability. Bridge mills are well suited for machining aluminum, as they provide good rigidity and precision.
- Gantry Mills: Gantry mills are similar to bridge mills, but they have a movable table that allows them to machine larger workpieces. Gantry mills are well suited for machining aluminum, as they provide good rigidity and precision.
If you’re looking for a CNC router to machine aluminum, any of these types would be a good choice. However, it is important to consider the specific requirements of your application before making a purchase. [2]
Other options for machining aluminum
You can machine aluminum on any CNC router, but if you’re looking for a machine that’s designed specifically for the material, you have a few different options. There are three main types of CNC routers that are well-suited for machining aluminum:
- Fiber laser machines: These machines are equipped with a fiber laser that is designed to cut through metal quickly and efficiently. Fiber laser machines are some of the most expensive on the market, but they’re also some of the most powerful and accurate.
- Plasma machines: Plasma machines use high-powered jets of plasma to cut through metal. Plasma machines are less expensive than fiber laser machines, but they’re not as precise or as fast.
- Waterjet machines: Waterjet machines use high-powered jets of water to cut through metal. Waterjet machines are less expensive than plasma and fiber laser machines, but they’re also not as precise or as fast.
If you’re looking for a machine that’s specifically designed for machining aluminum, one of these three types of CNC routers is the best option. In general, fiber laser machines are the most expensive and the most powerful, while waterjet machines are the least expensive and the least powerful. Plasma machines fall somewhere in the middle, in terms of both price and performance.
Of course, there are other factors to consider when choosing a CNC router, such as accuracy, speed, and features. But if you’re looking for a machine that’s specifically designed for machining aluminum, one of these three types is the best option.
Tips for CNC Machining Aluminum with a CNC Router
CNC machining aluminum is a popular application for CNC routers. When done correctly, it can produce parts with a high level of precision and accuracy. However, there are a few things to keep in mind when machining aluminum with a CNC router.
Use lubrication
Aluminum is a difficult material to work with and can cause wear and tear on your CNC router bit.
A good lubricant will help to cool the bit and reduce friction.There are a few different types of lubricants that can be used when cutting aluminum. Water-based coolants are the most common type of lubricant used with CNC routers. These coolants can help to keep the bit cool and reduce friction. Oil-based coolants are also an option, but they can be messier to work with and may require more cleanup afterwards.
No matter which type of lubricant you choose, it is important to make sure that it is compatible with your CNC router. Some lubricants can damage the components of your machine, so it is always best to consult your owner’s manual or the manufacturer before using any new products on your machine.
Use carbide end mills — either 3 flute or 2 flute
Aluminum is a difficult material to cut and machine, which is why you need to use the best tools for the job. Carbide end mills are made specifically for cutting aluminum and will make your life a lot easier. Use either a three flute or two flute end mill, with the latter being slightly better suited for softer metals. [3]
Avoid using high speeds — keep it around 600 RPM
If you try to cut aluminum too quickly, you’re just asking for trouble. The metal will heat up and start to deform, making it difficult (if not impossible) to get a clean cut.
Instead, take your time and keep the speed around 600 RPM. This may seem slow, but trust us – it’s much better than trying to go too fast.
Use a coolant — it will help to prevent chips from sticking.
Another way to prevent chips from sticking is to use a coolant while you’re cutting. This will help keep the aluminum from heating up and will also make it easier to remove any chips that do stick. Just be sure to use a non-petroleum based coolant, as the petroleum can actually cause aluminum to degrade over time. [3]
Use a smaller end mill
Another way to make cutting aluminum easier is to use a smaller end mill. The smaller the end mill, the less material you have to remove with each pass. This will help to keep the aluminum from heating up and will also make it easier to get a clean cut. Just be sure not to go too small – you don’t want the end mill breaking in the middle of your project!
Metal CNC Spindle
If you’re looking for a powerful and precise CNC router for aluminum, then you’ll want to consider one with a metal spindle. Metal spindles are much more durable than their plastic counterparts and can handle heavier workloads. They also tend to be more precise, so if you need extremely accurate cuts, then a metal spindle is the way to go.
There are a few things to keep in mind when shopping for a CNC router with a metal spindle. First, make sure that the spindle is properly supported. A poorly supported spindle can cause vibration and poor cuts. Second, check the speed of the spindle. The faster the better, as this will help you get your work done quickly. [3]
Rigidity
Another important factor to consider when choosing a CNC router for aluminum is rigidity. A well-built machine will be able to handle heavy cuts without flexing or vibrating. This is especially important if you’re doing precision work, as any vibration can lead to inaccuracies in your cuts.
There are a few things you can do to ensure that your CNC router is as rigid as possible. First, make sure that it has a strong frame. The heavier the better, as this will help to dampen any vibrations. Second, check the quality of the linear bearings. Higher quality bearings will allow the machine to move more smoothly and with less vibration. Finally, make sure that the spindle is properly supported. A poorly supported spindle can cause vibration and poor cuts.
Consider what upgrades or accessories you need
The first step is to consider what upgrades or accessories you need for your specific application. A few general things to keep in mind are the type of router bit, end mill, or spiral you’ll be using (carbide versus high-speed steel is better for aluminum), and the size and power of the router. Also, think about any special features that might be helpful, such as an automatic tool changer or a dust collector.
How large a table size and travel area do you need for CNC cutting metal?
The table size is one of the most important specifications of any CNC router. It determines how large a piece you can cut, as well as how big your setup will be. If you’re only looking to cut small pieces of aluminum, then a small table size will suffice. However, if you want to be able to cut larger pieces or even sheets of aluminum, then you’ll need a larger table size.
As for travel area, this is the amount of space that the cutting head has to move around in. Again, if you’re only looking to cut small pieces of aluminum, then a smaller travel area will do just fine. But if you want to be able to Cut larger pieces or even sheets of aluminum, then you’ll need a larger travel area.
Comparison of Indicators for Choosing CNC Routers for Aluminum
The following table provides a comparison of various indicators to consider when selecting CNC routers for aluminum machining. These indicators can help in evaluating and choosing the most suitable CNC router for your specific requirements. The table includes key factors such as spindle power, maximum feed rate, accuracy, and price range, which are crucial for efficient and precise aluminum cutting.
Indicator | Explanation |
---|---|
Spindle Power | The power rating of the router’s spindle, influencing cutting efficiency. |
Maximum Feed Rate | The maximum speed at which the router can move the cutting tool. |
Accuracy | The precision with which the router can execute cutting operations. |
Price Range | The approximate cost range for the CNC router. |
The table provides a general overview of the indicators to consider when choosing a CNC router for aluminum machining. It does not compare specific router models but instead focuses on the key indicators that are important for selecting an appropriate CNC router.
- Spindle Power: This indicator represents the power rating of the router’s spindle, which has a direct influence on the cutting efficiency. Higher spindle power generally allows for faster and more efficient cutting of aluminum.
- Maximum Feed Rate: The maximum feed rate indicates the speed at which the CNC router can move the cutting tool while machining aluminum. A higher feed rate allows for faster machining operations and increased productivity.
- Accuracy: Accuracy refers to the precision with which the CNC router can execute cutting operations. A higher accuracy ensures precise and consistent cutting of aluminum parts, leading to better quality and reduced wastage.
- Price Range: The price range indicates the approximate cost range for the CNC router. It is essential to consider the price range in relation to the specific requirements and budget constraints to ensure a cost-effective choice.
When selecting a CNC router for aluminum machining, it is important to evaluate these indicators and prioritize them based on your specific needs and budget. Consider consulting with industry experts or CNC router manufacturers to identify the most suitable machine for your aluminum machining applications.
FAQ
What Can You Do with a CNC Router?
A CNC router is a versatile machine that can be used for a wide range of projects. With the right attachments, you can use a CNC router to mill aluminum, wood, and even plastic.
In addition to milling, CNC routers can also be used for engraving and cutting. With the proper bit, you can use your CNC router to cut intricate designs into aluminum sheets. You can also use it to engrave text or logos onto metal or wood surfaces.
Finally, CNC routers can also be used for routing. Routing is the process of cutting grooves or channels into a material. This is often done in order to create decorative edges on furniture or cabinets. With a CNC router, you can easily create routered edges on aluminum sheets.
Overall, CNC routers are extremely versatile machines that can be used for a wide variety of projects. With the right attachments and bits, you can use your CNC router to mill, engrave, cut, or route aluminum.[4]
How to Cut Aluminum?
There are several ways to cut aluminum with a CNC router. The most common and popular method is using an end mill. End mills come in all shapes and sizes, but for aluminum, you’ll want to use one that has at least four flutes.
Another way to cut aluminum is by using a laser cutter. Laser cutters work by burning through the material with a high-powered laser beam. This method is very precise and can produce very intricate designs. However, it is also very expensive and requires special training to operate.
If you’re looking for a more affordable option, you can try using a plasma cutter. Plasma cutters work by heating up the metal until it melts and then blowing. it away with a high-powered stream of air. This method is less precise than laser cutting but can still produce good results.
Finally, you can also use waterjet cutters to cut aluminum. Waterjet cutters work by using a high-pressure stream of water to cut through the metal. This method is very precise and can produce detailed designs. However, it is also very expensive and requires special training to operate.
No matter which method you choose, always be sure to wear proper safety gear when working with any type of machinery.[5]
How Much is a CNC Router?
You can find a quality desktop CNC router for around $300. These will have a smaller bed size which is perfect for aluminum projects. If you need a larger bed size, you can expect to pay around $100000 for a commercial-grade machine.
Keep in mind that you will also need to purchase software and bits separately. aluminum is a very soft metal, so you will need to get carbide or diamond-tipped bits. These can be expensive, but they will last much longer than traditional bits.
You may also want to consider getting a dust collector for your CNC router. Aluminum produces a lot of dust when it’s cut and this can quickly clog up your machine. A dust collector will help prolong the life of your CNC router and keep it running smoothly.
In general, you can expect to spend anywhere from $300-$100000. [6]
What is a CNC Router?
A CNC router is a computer-controlled machine that can be used to cut aluminum (and other materials). They are often used in manufacturing and woodworking.
CNC routers come in all shapes and sizes. Some are small enough to fit on a desktop, while others are large commercial-grade machines.[1]
Is it better to cut aluminum fast or slow?
When it comes to cutting aluminum, there is no definitive answer as to whether it is better to cut fast or slow. It really depends on the specific project and what you are hoping to achieve with your cuts. If you need precision cuts, then cutting slowly may be the best option. However, if you are looking for speed, then cutting quickly may be the way to go. Ultimately, it is up to you to decide what will work best for your particular project.
One thing to keep in mind is that cutting aluminum can generate a lot of heat. This means that if you are cutting quickly, you will need to be extra careful not to overheat your material. Otherwise, you could end up damaging your aluminum or even causing it to catch fire.
Another thing to consider is the type of saw you are using. Some saws are designed for cutting aluminum specifically, while others may not be as well-suited for the task. If you are unsure about which saw to use, it is always best to consult with an expert before beginning your project.
Finally, it is important to have the right blades on hand before beginning your cut. Aluminum can be a difficult material to cut, so having sharp blades is essential. You will also want to make sure that your blades are designed for cutting aluminum specifically. Otherwise, you could end up causing damage to your saw or even injuring yourself.[5]
Can you CNC 6061 aluminum?
Yes, you can CNC 6061 aluminum with a good quality CNC router. However, it is important to note that aluminum is a softer metal and therefore requires more care when machining. In addition, aluminum produces a lot of dust and chips when machining, so it is important to have proper ventilation and chip removal system in place.[6]
What is the difference between 6063 and 6061 aluminum?
6061 aluminum is one of the most versatile heat treatable alloys available. It can be welded, riveted, or bolted in construction applications. 6063 aluminum is widely used in architectural applications such as window and door frames because of its good structural properties and aesthetically pleasing appearance.
The two alloys share many similarities, but they also have several important differences that affect their suitability for certain applications. The main difference between 6061 and 6063 aluminum is that 6063 is more malleable and easier to extrude than 6061. This makes it ideal for use in complex shapes and intricate designs. It’s also why 6063 aluminum is often used for electrical applications where it needs to be bent or formed into specific. [6]
What kind of blade do I need to cut aluminum?
Aluminum is a soft metal, so it can be cut with just about any type of blade. However, for the best results, you should use a blade specifically designed for cutting aluminum. These blades are typically made from high-speed steel or carbide and have teeth that are spaced more closely together than those on general-purpose blades.
When choosing a blade, keep in mind that the number of teeth per inch (TPI) will determine how fast the blade can cut. The higher the TPI, the faster the cut. However, blades with more teeth also produce a smoother finish. So if you’re looking for a clean cut with minimal burrs, choose a blade with fewer teeth. For thicker pieces of aluminum, you’ll need a blade with more teeth to avoid excessive binding.
In general, a 24-40 TPI blade is good for most applications. If you’re cutting very thick aluminum or aluminum that’s difficult to work with, you may need a blade with as few as 18 TPI.
Once you’ve chosen the right blade, make sure it’s properly installed and tensioned in your saw before beginning any cuts. A dull or improperly installed blade will cause the saw to bind and may damage both the saw and the material you’re trying to cut. [5]
What factors should I consider when choosing a CNC router for aluminum?
When selecting a CNC router for aluminum, you should consider factors such as spindle power, rigidity of the machine frame, feed rates, and the ability to control chip evacuation. These factors will determine the machine’s ability to handle aluminum cutting tasks effectively.
Which spindle speed is recommended for cutting aluminum on a CNC router?
For cutting aluminum on a CNC router, it is generally recommended to use high spindle speeds. Higher spindle speeds help prevent the material from galling or sticking to the cutting tool, resulting in smoother cuts and reducing the risk of tool breakage.
What type of cutting tool is best suited for machining aluminum on a CNC router?
For machining aluminum on a CNC router, carbide cutting tools are widely used and recommended. Carbide tools offer excellent durability and can withstand the high speeds and cutting forces associated with aluminum machining. They provide better performance and longer tool life compared to other materials.
How should I control the feed rate when cutting aluminum on a CNC router?
When cutting aluminum on a CNC router, it is essential to maintain an optimal feed rate. Too high of a feed rate can cause excessive tool wear and vibration, while too low of a feed rate can result in poor surface finish. It is recommended to consult the machine manufacturer’s guidelines or conduct tests to determine the ideal feed rate for your specific CNC router and aluminum cutting requirements.
What techniques can I use to improve chip evacuation when cutting aluminum on a CNC router?
To ensure efficient chip evacuation while cutting aluminum on a CNC router, you can employ techniques such as using compressed air or a vacuum system to remove chips from the cutting area. Additionally, using cutting tools with proper chip flute designs and employing appropriate coolant or lubrication methods can help enhance chip evacuation and prevent chip buildup.
Are there any safety considerations when using a CNC router for aluminum cutting?
Yes, there are several safety considerations when using a CNC router for aluminum cutting. It is important to wear appropriate personal protective equipment (PPE), such as safety glasses, gloves, and hearing protection. Additionally, ensuring proper ventilation to control the aluminum dust and chips, and following safe operating procedures and guidelines provided by the machine manufacturer are crucial for a safe working environment.
Useful Video: Best CNC Router Machine Cutting Aluminum
Final thoughts
Routers are an important part of any woodworking or CNC shop. They come in all shapes and sizes, but when it comes to working with aluminum, there are a few things you need to keep in mind. In this article, we’ve gone over some of the best CNC routers for aluminum, as well as some tips and tricks for getting the most out of your machine.
We hope that this article has been helpful in your search for the perfect CNC router for your aluminum work. If you have any questions or comments, please feel free to leave them below. As always, thanks for reading!
References:
- https://mellowpine.com/cnc/best-aluminum-milling-cnc-machines-desktop/
- https://www.cncsourced.com/rankings/best-metal-cnc-machines-aluminum/
- https://handtoolsforfun.com/best-cnc-router-for-aluminum/
- https://all3dp.com/2/cool-cnc-router-projects-ideas/
- https://www.hlsmetal.com/?gclid=CjwKCAjwrNmWBhA4EiwAHbjEQET0aAj-lFT0gin0Ndc4i1LIV7wbCClxA_XyprpCw7FVA0mVbpQKwhoCLngQAvD_BwE
- https://www.kloecknermetals.com/blog/comparing-6061-vs-6063-aluminum/.
- https://www.amazon.com/Genmitsu-3018-PRO-Control-Engraving-300x180x45mm/dp/B07P6K9BL3
- https://www.amazon.com/dp/B01M7VBAQN
- https://www.amazon.com/SainSmart-Genmitsu-3018-PROVer-Switches-Emergency-Stop/dp/B07ZFD6SKP
- https://www.amazon.com/VEVOR-Machine-Control-Extension-Engraving/dp/B08425BG33
- https://www.amazon.com/dp/B07HN68FTX