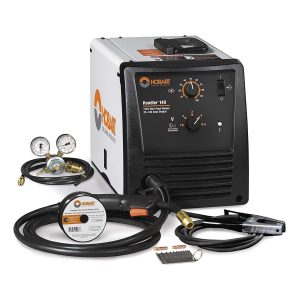
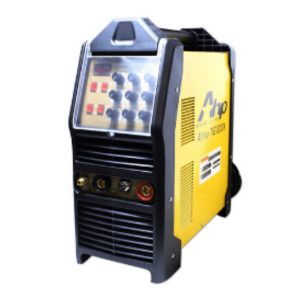
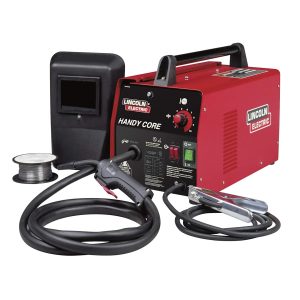
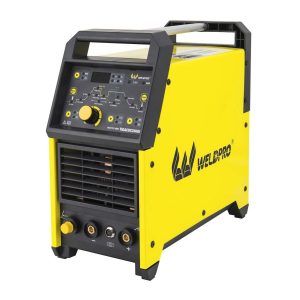
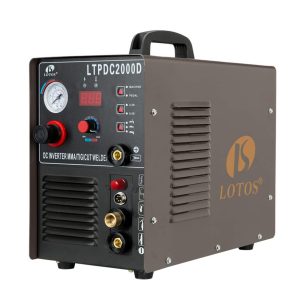
Choose the Best Welder for Aluminum Boat
Customer’s Choice: the Best Rated Welders for Aluminum Boats
98 users answered this survey. Please help us improve this review!
Are you the proud owner of an aluminum boat? If so, then you know that proper maintenance is key to keeping it in good condition for years to come. One of the most important aspects of maintaining your aluminum boat is using a welder that is specifically designed for welding aluminum. This article will discuss the best welders for repairing and maintaining aluminum boats. It will also provide product reviews and useful tips to help you choose the right welder for your needs.
Hobart 500559 Handler 140 MIG Welder, 115 V
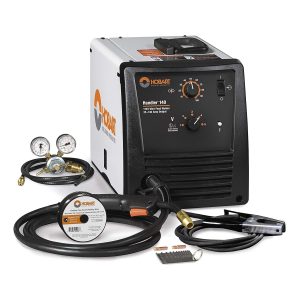
And because it can weld steel, stainless steel and aluminum, this welder is truly versatile. So, if you’re looking for a great all-purpose welder that’s easy to use and provides excellent results, look no further than the Hobart Handler 140 MIG Welder.
AHP Alpha TIG Stick Welder with pulse, 110 v, 220v
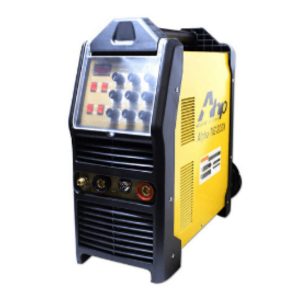
With one plastic handle, this welder is easy to carry around and use. Plus, it comes with the plug wired on the cord end so you can start using it right away. Whether you’re welding on aluminum, stainless or steel, this welder can do the job perfectly.
Lincoln Electric K2278-1 Welder with a Handy Core
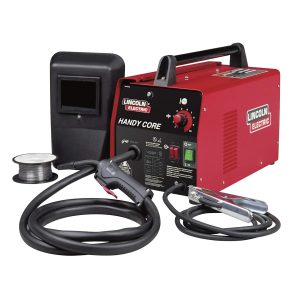
Plus, it comes complete with a welding handshield and chipping hammer/brush. And for your convenience, it includes a spool of self-shielded, flux-cored wire electrode. Get the Lincoln Electric K2278-1 Welder with Handy Core today and be ready to tackle your next welding project with ease.
Weldpro Digital AC/DC 200-Amp Tig/Stick Welder, 220V/110V
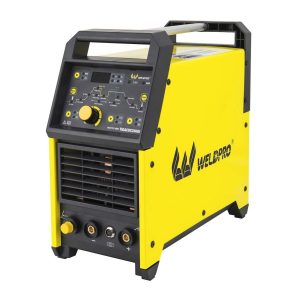
This device also has a flex head number 17F torch with independent trigger switch, and a rocker style foot pedal without annoying intermediate amperage control. You’ll be able to weld like a pro with this machine, thanks to its start and end amps, upslope, downslope control.
LOTOS LTPDC2000D Non-Touch Pilot 3-in-1 Combo Welding Machine, Brown
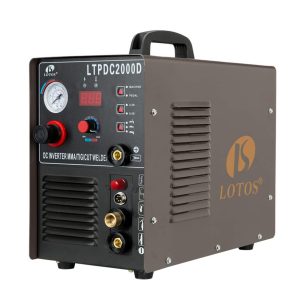
Plus, with a pre-installed NPT industry type-D plug, it’s easy to get started. And because it can cut stainless steel, alloy steel, mild steel, copper, and aluminum, it’s versatile too. Plus, with a maximum severance thickness of 19 mm, it can handle even the most challenging jobs. For added convenience, the HF arc start hand torch control allows for easy operation.
The non-hazardous compressed air means you can use it anywhere. And finally, the precise foot pedal welding heat control means you can get the perfect weld every time. Plus, the handle makes it easy to carry from one job to the next.
Buyer’s Guide
What is a Welder for Aluminum Boats?
An Aluminum Boat Welder is a specialized machine used to permanently join two pieces of aluminum together using heat and pressure. The process is similar to welding other materials, but some key differences make it important to use the right type of welder for the job.
Aluminum boats are often made with thin sheets of aluminum alloy that are welded together at the seams. This makes them lighter and more durable than boats made from other materials, but it also means that they require a different type of welding machine.
Aluminum has a lower melting point than steel, so it requires less heat to weld. It also has a higher thermal conductivity, which means that heat is conducted away from the welding area more quickly. This makes it more difficult to create a strong weld, and it also means that the welder needs to be able to adjust the amount of heat it produces.
Aluminum also has a higher expansion rate than steel, so it tends to warp when heated. This can make it difficult to produce a neat, finished weld.
List of the Basic Equipment for Welding an Aluminum Boat
If you have a Welder for Aluminum Boat, there are a few other things you will need to have to get started. Here is a list of the basic welding equipment for an Aluminum Boat:
- An AC welder that has at least 150 amps
- A DC welder with at least 40 volts
- A TIG welder with at least 20 amps
- MIG welder with at least 30 volts.
You will also need some safety gear, which includes:
- Welding gloves
- A welding helmet or face shield
- Safety glasses or goggles
Once you have all of the necessary equipment, you will be ready to start welding your aluminum boat!
What To Consider Before Buying a Welder For Aluminum?
Nature of Metal
Different metals have varying properties that affect how they react to heat and electricity. This is why it’s important to know the nature of the metal you’re working with before choosing a welder. Aluminum, for example, is a highly reactive metal that tends to melt quickly when exposed to heat or electricity. This means that you’ll need a welder that can generate high levels of heat without melting the aluminum.
Additionally, aluminum boats are often made with thin sheets of aluminum alloy. This makes them more susceptible to damage from welding than other materials like steel. As a result, you’ll need a welder that can provide a precise, controlled weld without causing too much damage to the surrounding area.
Finally, it’s important to consider the size and shape of the aluminum boat when choosing a welder. Some welders are better suited for working with large pieces of metal, while others are more precise and can be used on smaller projects.
Voltage and Amperage Range
The voltage and amperage range is one of the most important things to consider when choosing a welder. The voltage determines the amount of heat that the welder can generate, while the amperage determines the amount of electricity that the welder can use. You’ll need a welder with a high voltage and amperage range if you’re working with large pieces of aluminum or if you’re welding for extended periods.
However, if you’re only working on small projects or you only need to weld for short periods, you can get by with a lower-powered welder. On average, most welders range from 100 to 240 volts and can handle between 30 and 200 amps.
Duty cycle
The duty cycle is the amount of time that the welder can be used before it needs to cool down. This is important because it determines how long you can weld without taking a break.
However, some welders have a duty cycle of 50% or more, which means they can be used for four minutes before they need to cool down.If you’re going to be welding for extended periods, it’s important to choose a welder with a high-duty cycle. Additionally, it’s important to consider the amperage range when choosing a welder with a high-duty cycle. A welder with a high duty cycle but a low amperage range won’t be able to handle large projects [1].
Operating Processes
There are three main types of welding processes: MIG, TIG, and Stick. MIG welding is the most common type of welding. It’s a semi-automatic process that uses a wire feeder to supply the electrode. The electrode is then passed through a gas-filled chamber, which protects the weld from contamination.
TIG welding is a more precise form of welding that’s often used on thin metals like aluminum. In TIG welding, the welder holds the electrode in one hand and uses the other hand to hold a torch that produces an arc. The heat from the arc melts the metal, which joins the two pieces together. Stick welding is another common type of welding that’s often used on thicker metals. In stick welding, the welder passes an electrode through a gas-filled chamber and then touches it to the metal. The heat from the electrode melts the metal, which joins the two pieces together.
When choosing a welder, it’s important to consider the type of projects you’ll be working on. If you’re only going to be working on small projects, MIG welding is probably the best option. However, if you’re working on larger projects or more precise welds, TIG welding is a better choice. Stick welding is best suited for thick metals like steel [2].
Accessories
There are a few accessories that you’ll need to weld aluminum. First, you’ll need a gas tank and regulator. The gas tank supplies the welding gas, which protects the weld from contamination. The regulator controls the flow of gas to the welder. Second, you’ll need an electrode holder and cable. The electrode holder holds the electrode in place while you’re welding, and the cable connects the electrode holder to the welder. Finally, you’ll need a face shield or helmet to protect your eyes from the bright light produced by welding.
When choosing a welder, it’s important to make sure that it comes with all of the necessary accessories. Otherwise, you’ll have to buy them separately. Additionally, it’s important to choose a welder that’s easy to use and set up. Otherwise, you’ll waste a lot of time fumbling with the controls. Welders are an essential tool for anyone who works with aluminum boats.
Budget
When choosing a welder, it’s important to consider your budget. Welders can range in price from 90 euros to 1000 euros. However, the price doesn’t necessarily reflect the quality of the welder. In general, more expensive welders are more powerful and have more features. Moreover, they’re often easier to use and set up. However, there are plenty of high-quality welders that are available at a lower price.
Follow these steps while welding aluminum boats
Clean your environment
Before you weld, you always want to have a clean work area. That way there’s no chance of anything getting caught on fire and ruining your project. Make sure to clear the area around you and sweep up any dust or debris that could be flammable.
If you’re welding outdoors, be aware of your surroundings and make sure there’s nothing close by that could catch on fire. Once you’re confident in the safety of your workspace, it’s time to begin the work.
Before welding, cut pieces to fit
Cutting the aluminum to the right size is important for two reasons. First, it will make your welding job easier since you won’t have to manipulate the metal as much. Second, it will help you avoid wasting any material. Use a measuring tape and mark the pieces you need to cut with a pencil. Then, use a saw or grinder to cut the aluminum to size. If you’re using a power tool, be sure to wear safety goggles and gloves. Once you’ve cut all your pieces, it’s time to start welding!
Welding
Now that you have your environment set up and your pieces cut, you’re ready to start welding. If you’re a beginner, it’s always best to practice on some scrap metal first. That way, you can get a feel for the welder and how it works before moving on to your project.
When you’re ready to start welding, be sure to wear all the proper safety gear. This includes a welding helmet, gloves, and long sleeves. You should also have a fire extinguisher close by in case of any accidents. Turn on your welder and set it to the correct setting for aluminum. Then, begin welding your pieces together! Start at one end and work your way down until all the pieces are welded together. Once you’re finished welding, turn off the welder and let the pieces cool. Once they’re cool to the touch, you can remove your safety gear and admire your work!
Clean all equipment with solvent
After you’re done welding, it’s important to clean all your equipment. This includes the welder itself, as well as any hoses or other tools you used.
Welding can create a lot of fumes and debris, so it’s important to clean everything thoroughly before putting it away. The best way to clean your welder is with a solvent like acetone. Simply wipe down the machine with a rag soaked in solvent and let it dry completely before storing it away.
Remove aluminum oxide
Aluminum oxide is a substance that forms on the surface of aluminum when it’s exposed to air. This can make welding more difficult, so it’s important to remove it before beginning your project.
Simply scrub the surface of the metal until the oxide is gone and you’re ready to weld! Welding aluminum boats isn’t as difficult as it may seem. With the proper tools and safety gear, anyone can do it! Just be sure to take your time and practice on some scrap metal first. And always clean your equipment thoroughly after use [3].What Is the Difference Between TIG Welding & MIG Welding?
There are two main types of welding: MIG (Metal Inert Gas) and TIG (Tungsten Inert Gas). Both can be used to weld aluminum, but they each have their advantages and disadvantages. MIG welding is the more common of the two and is generally considered to be easier to learn. It is also faster than TIG welding, which makes it ideal for large projects or repairs. However, one downside of MIG welding is that it can be difficult to get a clean weld on thinner materials.
TIG welding, on the other hand, produces cleaner welds on all materials – including thin aluminum sheets. It also doesn’t require as much cleanup afterward. However, TIG welding is a more difficult process to learn and is much slower than MIG welding. So, which type of welding is best for aluminum boats? The answer depends on the project at hand. If you’re working on a large repair or building a new boat from scratch, MIG welding is probably your best bet. But if you’re looking for a cleaner weld on thinner materials, TIG welding is the way to go [4].
Comparison of Indicators for Choosing Welders for Aluminum Boats
When selecting a welder for aluminum boat fabrication, several indicators need to be considered to ensure optimal welding performance. This table provides a general comparison of key indicators such as amperage range, duty cycle, welding process, and power source. These indicators can guide you in selecting a welder that aligns with the requirements of aluminum boat welding.
Indicator | Recommended Range |
---|---|
Amperage Range (A) | 50-400 |
Duty Cycle (%) | 30-60 |
Welding Process | TIG or MIG |
Power Source | AC/DC or AC |
This table provides a general recommendation for the key indicators when choosing a welder for aluminum boat fabrication.
- Amperage Range (A): It is recommended to select a welder with an amperage range between 50 and 400. This range allows for welding a wide variety of aluminum thicknesses commonly encountered in boat construction.
- Duty Cycle (%): The duty cycle range of 30-60% ensures that the welder can operate for extended periods without overheating. This range provides a good balance between productivity and cooling requirements.
- Welding Process: TIG (Tungsten Inert Gas) or MIG (Metal Inert Gas) welding processes are commonly used for aluminum boat fabrication. Both processes offer excellent control and quality welds for aluminum.
- Power Source: It is advisable to choose a welder with either an AC/DC or AC power source. These power sources provide the necessary flexibility and compatibility for welding aluminum effectively.
Considering these general indicators will assist you in selecting a welder that meets the requirements for welding aluminum boats, ensuring the desired welding performance and structural integrity of the fabricated vessels.
FAQ
Which welder is best for aluminum?
There is no one-size-fits-all answer to this question, as the best welder for aluminum will vary depending on the specific needs of the boat owner. However, some of the best welders for aluminum boats feature quick-change tips, dual voltage capability, and a wide range of power settings.
In general, MIG welders are the best choice for welding aluminum boats. This is because they provide a strong, consistent weld that is less likely to crack or break than other types of welds. However, TIG welders can also be used for aluminum boat welding, and they offer the advantage of being able to create very precise welds.
What are the benefits of using an aluminum welder?
Aluminum welders have many benefits over other types of welders. They are more lightweight and portable, which makes them ideal for use on boats. They also have a lower risk of producing sparks and heat damage to nearby surfaces. In addition, aluminum welders are less likely to distort the metal, and they can be used to create very strong and precise welds.
What size welder do I need for aluminum?
The size of welder you need for aluminum will depend on the thickness of the metal you are welding. For most boat applications, a welder with at least 200 amps of power will be sufficient. However, if you are welding thicker materials, you may need a welder with more power.
What is the strongest weld for aluminum?
The strongest weld for aluminum is typically a MIG weld. This is because MIG welds are less likely to crack or break than other types of welds.
However, TIG welders can also be used for aluminum boat welding, and they offer the advantage of being able to create very precise welds.
Do you need AC or DC to weld aluminum?
AC or DC power can be used to weld aluminum. However, AC is typically the better choice because it provides a more stable arc. In addition, AC welders are less likely to cause damage to the aluminum.
Why is it difficult to weld aluminum?
Aluminum is a difficult material to weld because it is very sensitive to heat. If the aluminum gets too hot, it will melt and become unusable. In addition, aluminum is also very conductive, which means that it can easily cause sparks and heat damage to nearby surfaces. Welding aluminum boats can be a challenging task, but with the right welder and some practice, it can be done successfully. Be sure to consult a professional if you are unsure about any aspect of the welding process. With proper care and maintenance, your welded boat will provide years of enjoyment on the water.
Should I preheat aluminum before welding?
Yes, you should always preheat aluminum before welding. This is because aluminum is very sensitive to heat and can easily melt if it gets too hot. Preheating the aluminum will help to prevent this from happening. Welders are an essential tool for anyone who owns an aluminum boat.
What is the hardest metal to weld?
The hardest metal to weld is typically titanium. This is because titanium is very difficult to heat evenly, and it can easily become damaged if the welding process is not done correctly. However, with the right welder and some practice, it is possible to weld titanium successfully.
Can you weld aluminum with a stick welder?
Yes, you can weld aluminum with a stick welder. However, it is important to note that stick welders are not typically the best choice for welding aluminum. This is because they tend to be less precise and can cause more damage to the metal. If you decide to use a stick welder for aluminum boat welding, be sure to consult a professional for advice on how to properly set up and use the welder.
How do you weld aluminum cheaply?
One way to weld aluminum cheaply is to use an AC welder. AC welders are less expensive than DC welders and provide a more stable arc. In addition, AC welders are less likely to cause damage to the aluminum. Another way to save money when welding aluminum is to preheat the metal before welding. This will help to prevent the aluminum from melting and becoming unusable.
What are the key considerations when choosing a welder for aluminum boat welding?
When selecting a welder for aluminum boat welding, several factors need to be taken into account. These include the welder’s amperage range, duty cycle, welding process compatibility, and the ability to control heat input. Additionally, it is essential to ensure that the welder is capable of producing clean and consistent welds on aluminum.
What type of welding process is commonly used for aluminum boat fabrication?
TIG (Tungsten Inert Gas) welding is the most commonly used process for aluminum boat fabrication. TIG welding offers precise control over heat input, produces high-quality welds, and allows for better control over the weld pool. The process utilizes a non-consumable tungsten electrode, an inert shielding gas such as argon, and a filler metal rod to create strong and reliable welds on aluminum.
What are some important features to look for in an aluminum boat welder?
When selecting an aluminum boat welder, several features can enhance the welding process. These include a high-frequency start option, pulse welding capabilities, adjustable amperage control, AC balance control, and the ability to connect a foot pedal or remote control. These features provide greater control and precision, enabling the welder to produce high-quality welds on aluminum boat structures.
What are the recommended amperage settings for welding aluminum boats?
The recommended amperage settings for welding aluminum boats depend on various factors, such as the thickness of the material and the welding process used. As a general guideline, TIG welding on aluminum typically requires an amperage range of 100 to 200 amps for thin materials and up to 300 amps for thicker sections. However, it is crucial to consult the welding equipment manufacturer’s guidelines and adjust the settings based on the specific requirements of the boat and the welding project.
What type of gas is commonly used for shielding during aluminum boat welding?
Argon is the most commonly used gas for shielding during aluminum boat welding. It provides an inert atmosphere that protects the weld pool from atmospheric contamination, such as oxygen and nitrogen. Pure argon or a helium-argon mixture can be used, depending on the specific welding process and the desired characteristics of the weld.
How should the aluminum boat be prepared before welding?
Prior to welding, it is essential to properly prepare the aluminum boat for optimal weld quality. This includes removing any surface contaminants, such as dirt, grease, or oxide layers, by cleaning the area to be welded using a stainless steel brush, acetone, or a dedicated aluminum cleaner. Additionally, it is advisable to clamp or fixture the workpiece securely to prevent distortion during the welding process.
What are some common challenges and potential issues when welding aluminum boats?
Welding aluminum boats can present a few challenges and potential issues. These include the formation of oxide layers on the aluminum surface, which can affect weld quality, and the high thermal conductivity of aluminum, which requires precise heat control. Other challenges may include the potential for distortion, the need for proper joint design and fit-up, and the possibility of hydrogen-induced cracking. Addressing these challenges often requires proper preparation, selection of appropriate welding techniques, and adherence to best practices for aluminum boat welding.
What types of filler metals are commonly used for welding aluminum boats?
Filler metals used for welding aluminum boats typically belong to the 5000 or 6000 series aluminum alloys. Common choices include 5356 and 4043 filler wires. 5356 filler wire is well-suited for welding marine-grade aluminum alloys, while 4043 filler wire is often used for general-purpose welding of aluminum. The choice of filler metal depends on the specific application, the base material being welded, and the desired properties of the final weld.
Useful Video: Welding aluminum boat from scratch with PushPull gun on PP200
Conclusion Paragraph
The aluminum boats need proper care and handling. They are an excellent investment, and with the right welder, you can extend the life of your boat significantly. There are many different welders on the market, but not all of them are created equal. This article has reviewed five of the best Welders for Aluminum Boats so that you can make an informed decision about which one is right for you. These models feature different price points, amperage levels, and duty cycles so that you can find the perfect welder for your needs. With the right welder, you can keep your aluminum boat in excellent condition for years to come.
References:
- https://weldguru.com/how-to-choose-a-welder/
- https://www.millerwelds.com/resources/article-library/buying-your-first-welder-a-practical-informative-guide-for-doityourselfers
- https://selectsafety.net/how-to-weld-aluminum-boat-7-steps/
- https://www.fairlawntool.com/blog/mig-vs-tig-welding/