
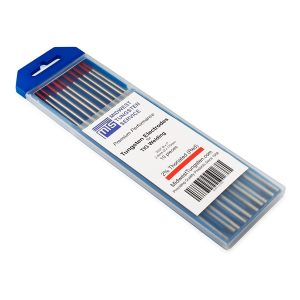
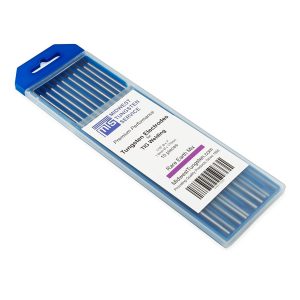
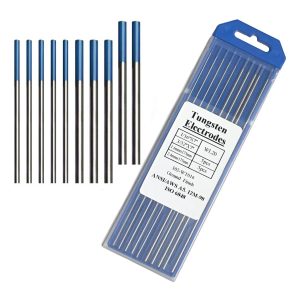
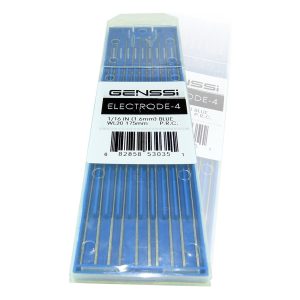
Choose the Best Tungsten for Aluminum
Customer’s Choice: the Best Rated Tungsten for Aluminum
11 users answered this survey. Please help us improve this review!
Now that you know the different types of tungsten electrodes, here’s a list of the top-5 best TIG welders for aluminum.
Midwest Tungsten Service TIG Welding Tungsten Electrodes 10-Pack (Blue – 2% Lanthanated Tungsten (WL20/EWLa-2), 3/32″)
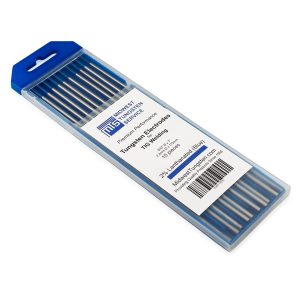
But beware – if you don’t use them properly they may melt too fast or even worse, come with a broken case or missing pieces! While MIDWEST TUNGSTEN SERVICE is not known for low-quality supplies, at this price point, it’s imperative that you check each box before opening it. Doing so will ensure that what you get isn’t faulty or substandard. In any case, make sure to read instructions carefully before using these electrodes to guarantee great results. Don’t settle for second best when you’re relying on a critical component of your welds.
Midwest Tungsten Service TIG Welding Tungsten Electrodes 10-Pack 2% Thoriated
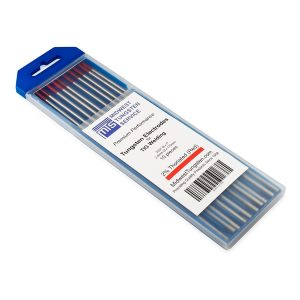
GENSSI TIG Welding Tungsten Electrode 175mm (7″) (1/16 (1.6mm) inch blue WL20)
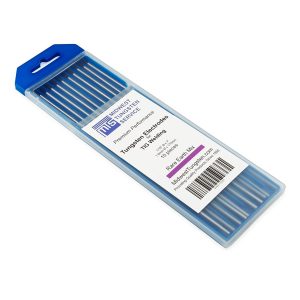
However some customers have reported having issues with the electrodes melting even at low settings. So make sure to read instructions carefully before using these electrodes and keep a close eye on your welds to ensure you’re getting the best results possible.
Midwest Tungsten Service TIG Welding Tungsten Electrodes 10-Pack (Purple)
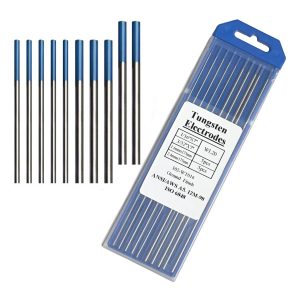
Thanks to Midwest Tungsten, crafting beautiful welds has never been easier. The premium materials used in the construction ensure even distribution of heat when welding and make sure that you achieve maximum bonding strength every time. Whether you’re working on dirty metals or clean projects, you can achieve perfect joins with the help of these purple tungsten electrodes. And when it comes to price, the 10-pack offers unbeatable value!
Still, it’s worth keeping in mind that there are reports of missing pieces however this seems to be a rare occurrence.
ZINGER TIG Welding Tungsten Electrodes 2% Lanthanated (WL20/EWLa-2) Blue,10-Pack
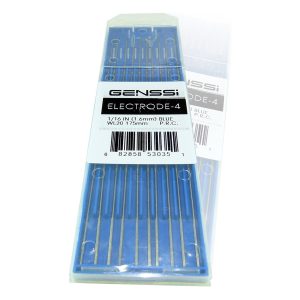
Say goodbye to unreliable electrodes with ZINGER TIG Welding Tungsten Electrodes 2%. With these trustworthy tools in your arsenal, you’ll never have to worry about an unsatisfactory weld job again. Plus, these electrodes come in packages of 10 so you can rest assured that you’re always prepared for whatever welding project comes your way.
Just keep in mind that these rods, while reliable, can shatter easily if you aren’t careful. So be sure to always wear protective gear, like a welding helmet and gloves when using these electrodes!
Are you looking for the best tungsten for aluminum? You’ve come to the right place! In this article, we will discuss everything you need to know about tungsten and aluminum. We’ll cover common questions such as “What is the difference between tungsten and aluminum?” and “Which material is better for my application?” We’ll also review some of the best tungsten for aluminum products on the market. By the end of this article, you’ll be able to choose the right tungsten alloy for your needs!
What is Tungsten Inert Gas Welding Used For?
Tungsten Inert Gas (TIG) welding is an arc welding process that uses a non-consumable tungsten electrode to produce the weld. The weld area is protected from atmospheric contamination by an inert shielding gas, typically argon or helium. A filler material may be used, but TIG welding can also be done without it.
At its most basic level, TIG welding involves creating an electric arc between a pointed tungsten electrode and the metal being welded to generate heat that melts both materials and produces a strong joint. A hand-held torch holds the tungsten electrode in place at a set distance from the metal being welded. When current passes through the circuit and arcs across this gap, the metal melts and produces a weld.
Additionally, the low heat input limits the amount of distortion caused by welding, making it ideal for producing high-precision joints. As a result, TIG welding is often used in applications where strength and accuracy are key factors such as aerospace or medical device manufacturing.To ensure quality welds, proper technique must be employed when using TIG welding equipment. This includes maintaining a consistent arc length between the tungsten electrode and the metal being welded, controlling filler material addition rate by hand, and monitoring the shielding gas flow rate at all times. With the right technique and high-quality equipment, operators can produce strong and reliable welds with TIG welding.[1],[2]
What TIG Welding is Used For?
TIG welding is widely used in many industries, including automotive and shipbuilding. The process is used to weld aluminum, stainless steel, brass, titanium, copper alloys and a variety of other metals. It’s also commonly employed for making pipe joints, fabricating sheet metal structures and creating structural components for aircraft.
In addition to being used for fabrication purposes, TIG welding can be utilized in repair operations as well. Since the process operates at a much lower temperature than other welding processes (around 6500°F) it does not cause warping or distortion on the surrounding material. This makes it ideal for repairing thin materials that would otherwise be difficult to work with due to warping caused by higher heat input processes like oxy-fuel welding.
Finally, TIG welding can be used to co-weld multiple materials together such as aluminum and steel. This is especially useful for applications where two or more metals need to be joined that would otherwise require multiple welding processes. By combining the materials into one weld puddle, operators can save time and increase efficiency in the fabrication process.[1],[2]
Types of Tungsten Electrodes
Now that we have a better understanding of the TIG welding process, let’s take a closer look at tungsten electrodes.
Ceriated
Ceriated tungsten electrodes, also known as thoriated tungsten electrodes, are one of the most popular types of electrodes. These electrodes contain a small amount of cerium oxide in their composition, which increases the electrical conductivity and enables better arc starts on low-amperage settings. Ceriated tungsten is ideal for welding aluminum and mild steel and can be used with AC power sources.
Lanthanated
Lanthanated tungsten electrodes are a type of welding electrode composed of tungsten and alloyed with 1.5-2.4% lanthanum oxide (La2O3). The addition of lanthanum oxide to a tungsten electrode increases its arc stability, allowing the welder to achieve higher levels of current density and lower heat input when welding aluminum. These unique properties make lanthanated electrodes ideal for applications where high levels of precision and accuracy is needed, such as in aluminum manufacturing processes.
Thoriated
Thoriated (thorium-tungsten) electrodes are one of the most common types of tungsten used in welding. This particular type of electrode is made by adding a small amount of thorium to pure tungsten, and it’s known for being more durable than other types.
The main benefit of thoriated electrodes is that they provide superior arc stability when compared to pure tungsten electrodes. The addition of thorium helps to reduce arc wander and creates a cleaner, more consistent weld. It also allows the user to set current levels lower than with regular tungsten, which means less heat build-up and less risk of burning through the workpiece.
Pure tungsten
Pure tungsten electrode is the most basic type of tungsten electrode and is made from pure tungsten metal. It’s typically used for relatively low-amperage welding jobs that require a strong, reliable arc and minimal heat input.
Pure tungsten electrodes are often used in aluminum welding because they provide good arc stability with low current settings. The drawback to this type of electrode is that it has a shorter lifespan than other types, making it less suitable for high-heat applications where wear resistance is needed. [1],[2],[3]
TIG Welder Buyers Guide
To help you with making a choice, we have put together a comprehensive TIG Welder Buyers Guide. In this guide, we will provide you with important points to consider before making a purchase, along with our roundup of the best tungsten for aluminum available on the market today.
When selecting a TIG welder for aluminum, it’s essential to know that all brands and models are not created equal. To make sure you get the right product for your welding needs, take into account these factors:
AC/DC inverter
The TIG welding process uses either alternating current (AC) or direct current (DC). AC can change the flow of current with time which doesn’t happen in DC. This can provide more flexibility for welding but does require a more powerful machine.
AC welding is ideal for thinner aluminum materials, such as sheet and tubing. DC welding works better on heavier sections of aluminum. To weld aluminum effectively with a TIG welder, you will need an AC/DC inverter, which can switch between the two currents.
Tungsten rods have varying degrees of heat resistance depending on the elements they are composed of. When utilizing an Alternating Current, this is not a concern; however, when using Direct Current, certain tungsten rods can be destroyed by excessive heat.
AC welding also requires larger–diameter tungsten electrodes. This means that you must use a specific type of tungsten rod for AC welding. For DC welding, most types of tungsten will work just fine.
Type of metal/alloy
The type of metal you choose for a tungsten material is important, as it can significantly impact the performance and quality of your welding project. When selecting a tungsten for aluminum, it’s important to understand that different types of metals contain varying levels of impurities and alloys which can affect overall weld puddle control, arc starting ability, and current carrying capacity.
For aluminum applications, pure tungsten is the most common choice. Pure tungsten has a low contamination level and provides excellent arc stability at higher amperage settings than other types of metals.
Zirconiated tungsten is also a solid choice for aluminum welding, and it offers several benefits over pure tungsten. Zirconiated tungsten has a slightly higher contamination threshold than pure tungsten, which means it can tolerate a bit more impurity before the weld starts to become unreliable.
It’s important to consider the metal composition and impurities in a tungsten material before selecting it for use in aluminum welding projects. The type of tungsten chosen should provide the best balance of arc performance, weld puddle control and current carrying capacity for your application. Additionally, it should reduce contamination risk as much as possible.
Electrode size
The size of the electrode you choose for your TIG welder is important for two reasons: it determines how much current is needed to effectively conduct heat, and it affects the weld pool shape. Generally speaking, larger electrodes will require more current but will also create a wider weld pool, which can be beneficial when welding aluminum.
When selecting an electrode size for aluminum, keep in mind that small diameters are typically used with thin metals and large diameters are best suited for thicker materials.
Price
Price is another important factor to consider when shopping for tungsten for aluminum. Tungsten electrodes can range in price from a few dollars each up to several hundred dollars per electrode.
Generally speaking, higher-priced electrodes will offer improved performance and better arc stability. However, there are some lower-cost alternatives that can deliver good results as well. It’s best to shop around and compare prices before making a purchase to make sure you get the best value for your money.
The cost of tungsten electrodes should be factored into the overall budget for any welding project. If cost is an issue, then selecting lower-priced options may be the way to go; however, it’s important to make sure that the quality of the tungsten is not compromised.
It’s also worth noting that purchasing electrodes in bulk can often result in significant discounts compared to buying individual units. This is something to consider if you plan on doing a lot of aluminum welding projects in the future. [1],[2],[3],[4]
Comparison of Indicators for Choosing Tungsten for Aluminum
The following table presents a comparison of various indicators to consider when choosing tungsten for aluminum. Tungsten is commonly used as an electrode material in welding applications, particularly for aluminum welding. Different indicators, such as melting point, thermal conductivity, and price, can help in determining the suitability of tungsten for welding aluminum. The table below provides a concise overview of these indicators for making an informed decision.
Indicator | Tungsten | Aluminum |
---|---|---|
Melting Point (°F) | 6192 | 1220 |
Thermal Conductivity (BTU/(hr·ft·°F)) | 100.1 | 138.2 |
Price ($/lb) | $13.64 – $22.05 | $0.68 – $1.14 |
The table above compares three important indicators for choosing tungsten as an electrode material for aluminum welding: melting point, thermal conductivity, and price.
- Melting Point: Tungsten has a significantly higher melting point (6192°F) compared to aluminum (1220°F). This high melting point makes tungsten suitable for welding applications as it can withstand the extreme temperatures involved in the process.
- Thermal Conductivity: Aluminum exhibits higher thermal conductivity (138.2 BTU/(hr·ft·°F)) than tungsten (100.1 BTU/(hr·ft·°F)). While aluminum’s high thermal conductivity is beneficial for efficient heat transfer during welding, tungsten’s lower thermal conductivity can provide better control and concentration of heat in specific areas.
- Price: Tungsten is relatively more expensive, with prices ranging from $13.64 to $22.05 per pound, while aluminum is more cost-effective, typically priced between $0.68 and $1.14 per pound.
Considering these indicators, tungsten is often preferred for welding aluminum due to its high melting point and the ability to concentrate heat effectively. However, the choice of electrode material ultimately depends on the specific requirements of the welding application and the budgetary considerations.
FAQ
What TIG welding is used for?
TIG (Tungsten Inert Gas) welding is a popular type of welding used by many professionals and hobbyists alike. It is versatile and suitable for many different applications, such as structural steel fabrication, automotive repair, aluminum repair and fabrication, thin sheet metal work, jewelry making, and more. TIG welding produces clean welds, is easy to learn, and offers good control.
TIG welding uses a torch and non-consumable tungsten electrode to create an arc between the metal parts that need to be joined. The heat generated by the arc melts the base material and filler rod which, once melted together, creates a strong bond. TIG welding is most commonly used to weld thin sheets of aluminum and stainless steel, but it can also be used on other materials such as copper, brass, titanium, cast iron and magnesium.
What tungsten is best for welding cast aluminum?
Pure tungsten is the best tungsten for welding cast aluminum. Pure tungsten is preferred because it provides a sharper arc, making it easier to control and more efficient when welding aluminum. Additionally, pure tungsten has a low melting point which means it melts quicker and provides greater heat transfer to the workpiece. This can be beneficial in situations where material needs to be welded quickly or at lower temperatures. When using pure tungsten for cast aluminum welding, it’s important to use an AC welder with low amperage settings (around 60A). Higher current levels can cause excessive burn-off of the electrode, resulting in wasted time and money.
What is the best TIG wire for aluminum?
The best TIG wire for aluminum depends on several factors including the base material, application, and desired results. Currently, there are three primary types of tungsten for aluminum: 2% thoriated (red or yellow), pure tungsten (green), and ceriated (gray).
As for the alloys, each type has its own properties and should be chosen according to the application. We recommend you use 4043, 4047, 4943 and 5356 for general purpose welding.
What type of electrode is best for aluminum?
The best electrode for aluminum is a tungsten electrode, as they have superior critical current levels and provide a smooth arc transfer when welding. Tungsten electrodes are also preferred due to their high melting point, making them ideal for use in aluminum welding applications.
When selecting the best tungsten electrode for your aluminum welding application, you need to consider its properties such as electrical conductivity, oxidation resistance, thermal conductivity and other characteristics that will affect the performance of your application. The most commonly used types of tungsten electrodes are pure tungsten (WP), thoriated (WT) and ceriated (WC) electrodes. Each type has its own unique characteristics that make it better suited to certain tasks than others.
Is purple tungsten suitable for aluminum?
Purple tungsten is not generally suitable for welding aluminum, as it does not produce deep penetration. However, purple tungsten can be used in certain cases if the welder has experience with it and takes special precautions to reduce the risk of burning through the material and creating a weak weld joint. When using purple tungsten for aluminum, the amperage should remain low (15-20 amps) and the arc length should be kept to a minimum. Additionally, preheating the workpiece before welding may help reduce porosity and improve overall weld quality.
For more complex or difficult applications, a different type of tungsten may be better suited for welding aluminum.
What is the role of tungsten in aluminum welding?
Tungsten is primarily used as an electrode material in aluminum welding. It acts as a non-consumable electrode and provides the necessary heat for the welding process. Tungsten’s high melting point and excellent heat resistance make it suitable for withstanding the intense heat generated during aluminum welding.
How does tungsten affect the quality of aluminum welds?
Tungsten plays a crucial role in determining the quality of aluminum welds. It helps to create a stable arc and provides precise control over the heat input during welding. Proper selection of tungsten type, diameter, and tip preparation can greatly influence the weld penetration, bead appearance, and overall weld quality.
What are the commonly used tungsten types for aluminum welding?
For aluminum welding, two commonly used tungsten types are pure tungsten (WP) and rare-earth tungsten (e.g., ceriated tungsten, thoriated tungsten). Pure tungsten is suitable for welding aluminum at lower amperages, while rare-earth tungsten offers better performance at higher amperages and is preferred for applications requiring increased arc stability.
What factors should be considered when selecting tungsten for aluminum welding?
Several factors should be considered when selecting tungsten for aluminum welding. These include the base metal thickness, welding current, desired arc characteristics, and specific application requirements. Additionally, factors such as tungsten diameter, tip geometry, and the presence of any impurities in the tungsten should be taken into account for optimal welding results.
Can I use a different tungsten for aluminum welding than for other metals?
While tungsten selection can vary depending on the specific application, it is generally recommended to use a dedicated tungsten for aluminum welding. Aluminum has unique characteristics and requires a tungsten electrode that can withstand the high thermal conductivity and oxide formation associated with aluminum welding. Using a separate tungsten electrode for aluminum helps maintain weld quality and prevent contamination.
What are the benefits of using pure tungsten for aluminum welding?
Pure tungsten electrodes offer several benefits for aluminum welding. They have a high melting point, good thermal conductivity, and provide a stable arc with low burn-off rate. Pure tungsten is suitable for low-amperage welding applications and is less prone to balling at lower current settings. It is commonly used for thin aluminum sheets or when precise heat control is required.
When should I consider using rare-earth tungsten for aluminum welding?
Rare-earth tungsten electrodes, such as ceriated tungsten or thoriated tungsten, are recommended for aluminum welding when higher amperages are involved. These tungsten types offer excellent arc stability, better electrode life, and improved performance at higher currents. They are particularly useful for thicker aluminum sections or when welding at higher heat inputs.
What are the potential risks of using the wrong tungsten for aluminum welding?
Using the wrong tungsten for aluminum welding can lead to various issues. It may result in poor arc stability, difficulty in initiating or maintaining the arc, excessive electrode consumption, or weld contamination. Additionally, using a tungsten unsuitable for aluminum may negatively impact the weld quality, such as poor penetration, inadequate fusion, or inconsistent bead appearance.
How can I properly prepare the tungsten electrode for aluminum welding?
Proper preparation of the tungsten electrode is essential for aluminum welding. It typically involves grinding the tungsten to a specific point and removing any oxide or contamination from the surface. The most common tungsten tip geometries for aluminum welding are a truncated cone or a pointed tip. It is crucial to avoid cross-contamination with other metals during preparation to maintain weld integrity.
Are there any safety precautions I should follow when using tungsten for aluminum welding?
When using tungsten for aluminum welding, it is important to follow standard safety precautions. Ensure proper ventilation in the welding area to prevent the inhalation of tungsten fumes. Use appropriate eye protection, such as welding helmets with the correct shade level for aluminum welding. Additionally, handle and store tungsten electrodes properly to avoid injury or damage.
Useful Video: TIG Welding: Tungsten Selection and Preparation
Conclusion
When it comes to welding aluminum, the best tungsten for aluminum is one that’s pure and sharp. Pure tungsten works better than alloyed types because it helps reduce contaminants in the weld pool and reduces arc wander. Sharpening your tungsten on a grinding wheel also helps to ensure accuracy and precision when welding, so you can get the job done faster and with fewer issues.
Tungstens are available in a variety of sizes and styles, each offering different levels of performance, so it’s important to choose the right size for your particular application. The type of filler metal used should also be taken into consideration when selecting a tungsten, as some work better than others depending on the material being welded.
In this article, we’ve discussed the best tungsten for aluminum and offered helpful tips for choosing the right one. We’ve also reviewed some of the top products on the market to help you make an informed choice. With this information, you’ll be well-equipped to find the perfect tungsten for your welding project!
If you have any questions or need more help selecting a tungsten, feel free to contact us at any time. Our team of experienced professionals is always happy to assist with any welding needs. Thanks for reading our Best Tungsten for Aluminum Epic Guide!
References:
- https://weldgears.com/best-tungsten-for-aluminum-welding/
- https://www.millerwelds.com/resources/article-library/all-about-tungsten-in-tig-welding-types-selection-and-use
- https://bakersgas.com/blogs/weld-my-world/the-best-tungsten-for-tig-welding-aluminum
- https://www.thefabricator.com/thewelder/article/aluminumwelding/choosing-tungsten-electrode-type-size-for-aluminum-gtaw